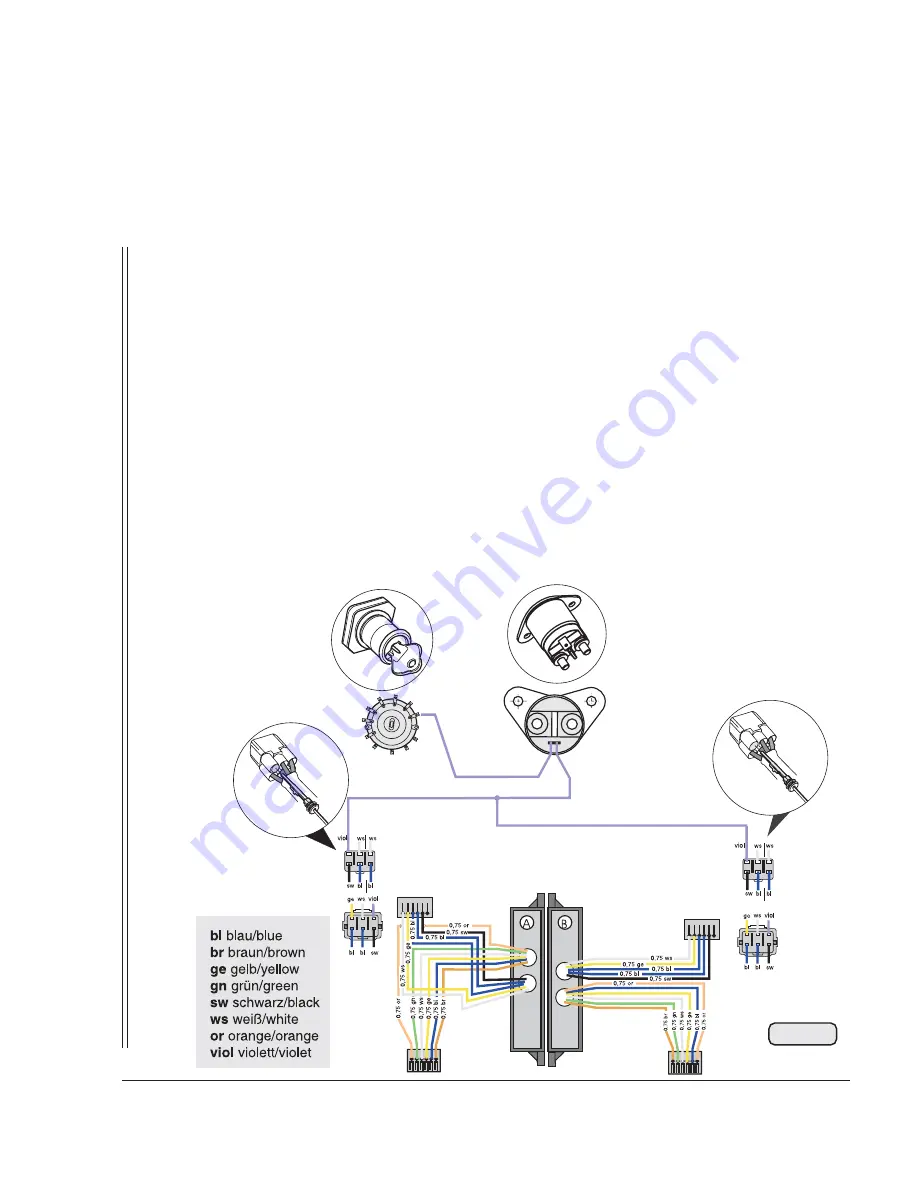
Effectivity: 912 Series
Edition 1 / Rev. 1
d04640
page 119
May 01/2009
BRP-Powertrain
INSTALLATION MANUAL
17.3.9) Battery
See Fig. 67.
■
CAUTION:
To warrant reliable engine start use a battery of at least
16 Ah capacity.
17.3.10) Capacitor (Option electrical fuel pump)
See Fig. 67.
■
CAUTION:
To warrant reliable operation of the electrical fuel
pump the use of capacitor of at least 22 000 μF / 25 V
is necessary.
17.3.11) Easy start function on the electronic module (optional)
See Fig. 67 and 79/1.
In order to use the easy start function the relevant connections to the
starter relays and ignition switch need to be made.
The start function can be used for aircraft, which have an engine start
problem in cold conditions.
◆
NOTE:
In addition also a modified fly wheel hub is offered,
which aids improved starting.
Fig. 79/1
00219