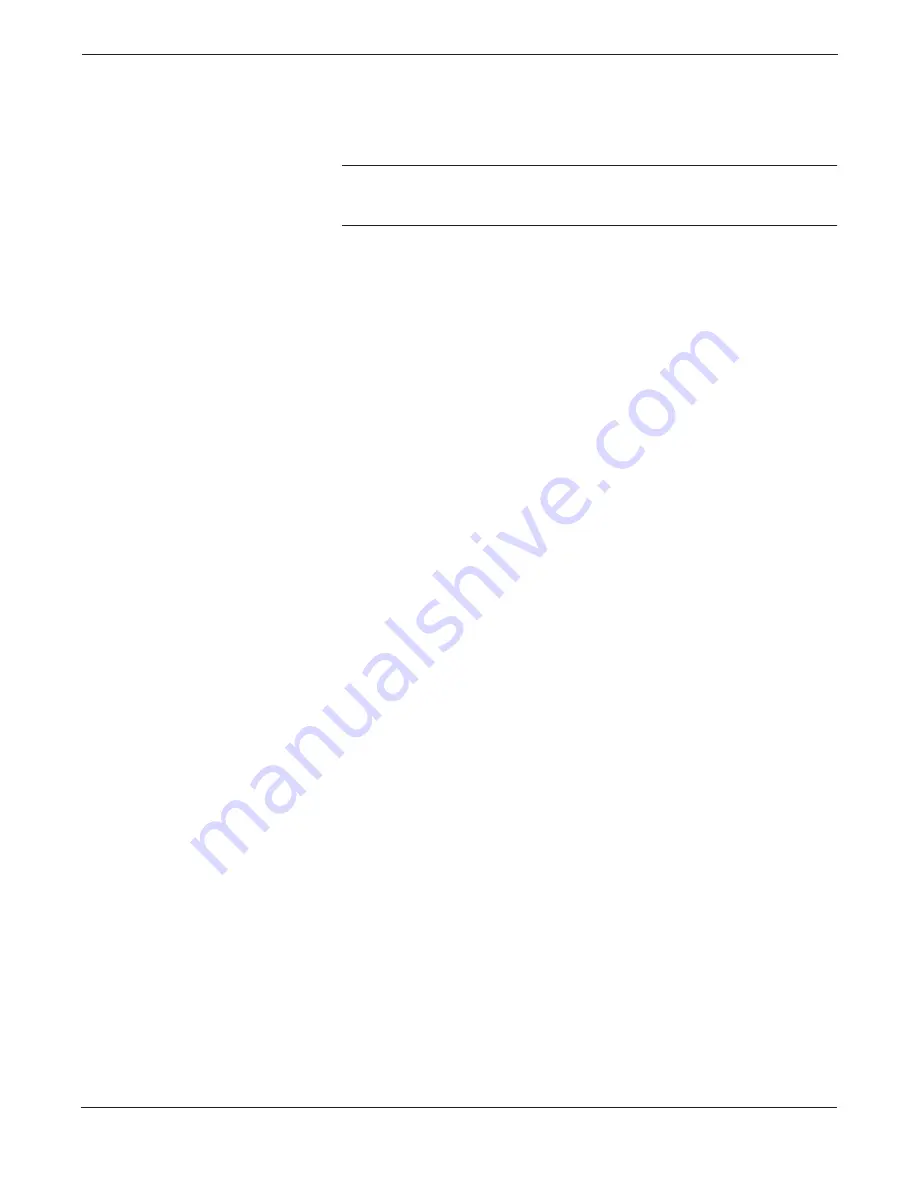
2-15
Level Controller Overview and Installation
TAP CONSIDERATIONS
When the Level Controller is oriented on its side, the Coplanar
™
flange
may be mounted to ensure proper venting or draining. Mount the flange
so that the drain/vent connections are on the top half of the flange for
liquid service.
CAUTION
In elevated temperature services, it is important that temperatures at
the Coplanar process flanges not exceed 250 °F (121 °C).
Impulse Piping
The piping between the process and the controller must accurately
transfer the pressure in order to obtain accurate control. In this
pressure transfer, there are five possible sources of error: leaks, friction
loss (particularly if purging is used), trapped gas in a liquid line, and
temperature-induced or other density variation between the legs.
The best location for the Level Controller in relation to the process pipe
depends on the process itself. Consider the following guidelines in
determining controller location and placement of impulse piping:
• Keep impulse piping as short as possible.
• Slope the impulse piping at least one inch per foot (8 centimeters
per meter) upward from the controller toward the process
connection for liquid.
• Avoid high points in liquid lines.
• Make sure both impulse legs are the same temperature.
• Use impulse piping large enough to avoid friction effects and
prevent blockage.
• Vent all gas from liquid piping legs.
• Avoid purging through the controller.
• Keep corrosive or hot (above 250 °F (121 °C)) process material out
of direct contact with the sensor module and flanges.
• Prevent sediment deposits in the impulse piping.
• Avoid conditions that might allow process fluid to freeze within
the process flange.
Diaphragm Seals
Because instrument response time is directly proportional to capillary
length, and the fill fluid volume in the capillary changes with
temperature to affect the output, care must be taken to optimize
performance:
• Keep the capillary length as short as possible.
• Mount a controller with one seal at the same level, or below the
seal and process connection. Use direct mount when possible.
• In vacuum applications, mount the controller below the lower tap
to ensure proper operation. This requirement applies to both one-
and two-seal systems.
• Avoid mounting seals and capillaries in direct sunlight.
• Keep the capillary lengths equal when two seals are involved.
• Rezero the controller on a seasonal basis.
• Never attempt to disconnect the seals or capillaries. Doing so will
void the warranty.
Summary of Contents for 3095
Page 2: ......
Page 4: ......
Page 8: ...viii ...
Page 10: ...Rosemount Model 3095 Multivariable Level Controller 1 2 ...
Page 42: ...Rosemount Model 3095 Multivariable Level Controller 3 10 ...
Page 74: ...Rosemount Model 3095 Multivariable Level Controller 5 18 ...
Page 98: ...Rosemount Model 3095 Multivariable Level Controller B 4 ...
Page 101: ...C 3 Approval Drawings FIGURE 3 1 continued 3095 1025A02A ...
Page 102: ...Rosemount Model 3095 Multivariable Level Controller C 4 FIGURE 3 1 continued 3095 1025A03A ...
Page 103: ...C 5 Approval Drawings FIGURE 3 2 Index of I S F M for 3095 3095 1020A01A ...
Page 104: ...Rosemount Model 3095 Multivariable Level Controller C 6 FIGURE 3 2 continued 3095 1020A02A ...
Page 105: ...C 7 Approval Drawings FIGURE 3 2 continued 3095 1020A03A ...
Page 106: ...Rosemount Model 3095 Multivariable Level Controller C 8 FIGURE 3 2 continued 3095 1020A04A ...
Page 107: ...C 9 Approval Drawings FIGURE 3 2 continued 3095 1020A05A ...
Page 108: ...Rosemount Model 3095 Multivariable Level Controller C 10 FIGURE 3 2 continued 3095 1020A06A ...
Page 110: ...Rosemount Model 3095 Multivariable Level Controller C 12 FIGURE 3 3 continued 3095 1024A02A ...
Page 111: ...C 13 Approval Drawings FIGURE 3 3 continued 3095 1024A03A ...
Page 113: ...C 15 Approval Drawings FIGURE 3 4 continued 3095 1021A02A ...
Page 114: ...Rosemount Model 3095 Multivariable Level Controller C 16 FIGURE 3 4 continued 3095 1021A03A ...