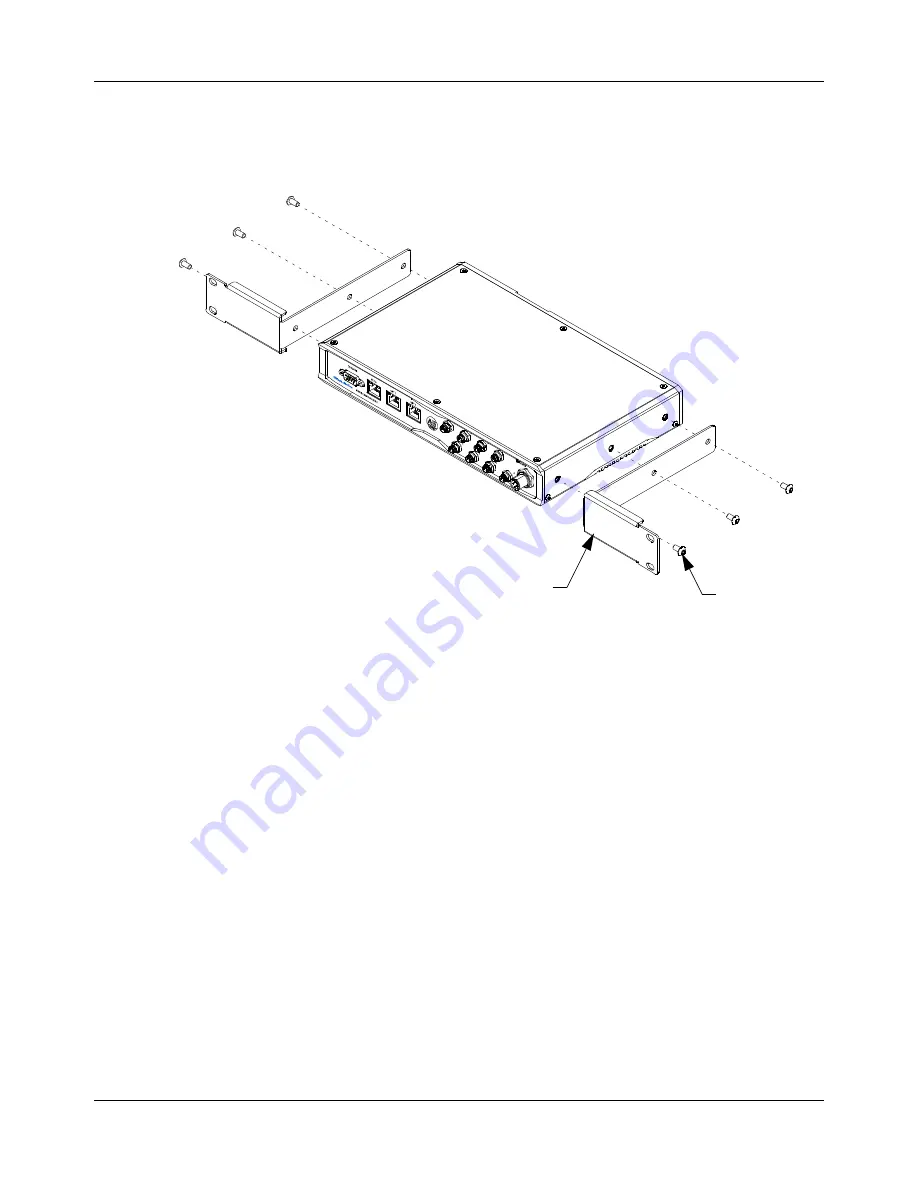
Installation
Node Controller Installation
Node Controller Hardware User Manual
89
Rockwell Automation Publication MMI-UM013B-EN-P - April 2020
Rack Mounting
The NC-S can be mounted in a standard 19 inch equipment rack by attaching the optional 1U
rack mounting brackets as shown in
Figure 5-3: NC-S Node Controller Rack Mounting
1.
Align each rack mounting bracket to the node controller and secure them with the sup-
plied M5 screws. Tighten to 1.1 N•m [10 in•lb].
2.
Locate the node controller in the rack and secure it with four screws (two per mount-
ing bracket) as specified by the rack manufacturer. Make sure that the service and
exclusion zones are maintained.
3.
Install cable management as required to secure the cables that are connected to the
node controller.
Mounting NC-S Power Supplies
Locate the power supply close to the node controller it is powering to minimize the length of
all wiring. The power supply can be oriented in any direction required.
M5 Screw
(6X)
Mounting Bracket
(2X)