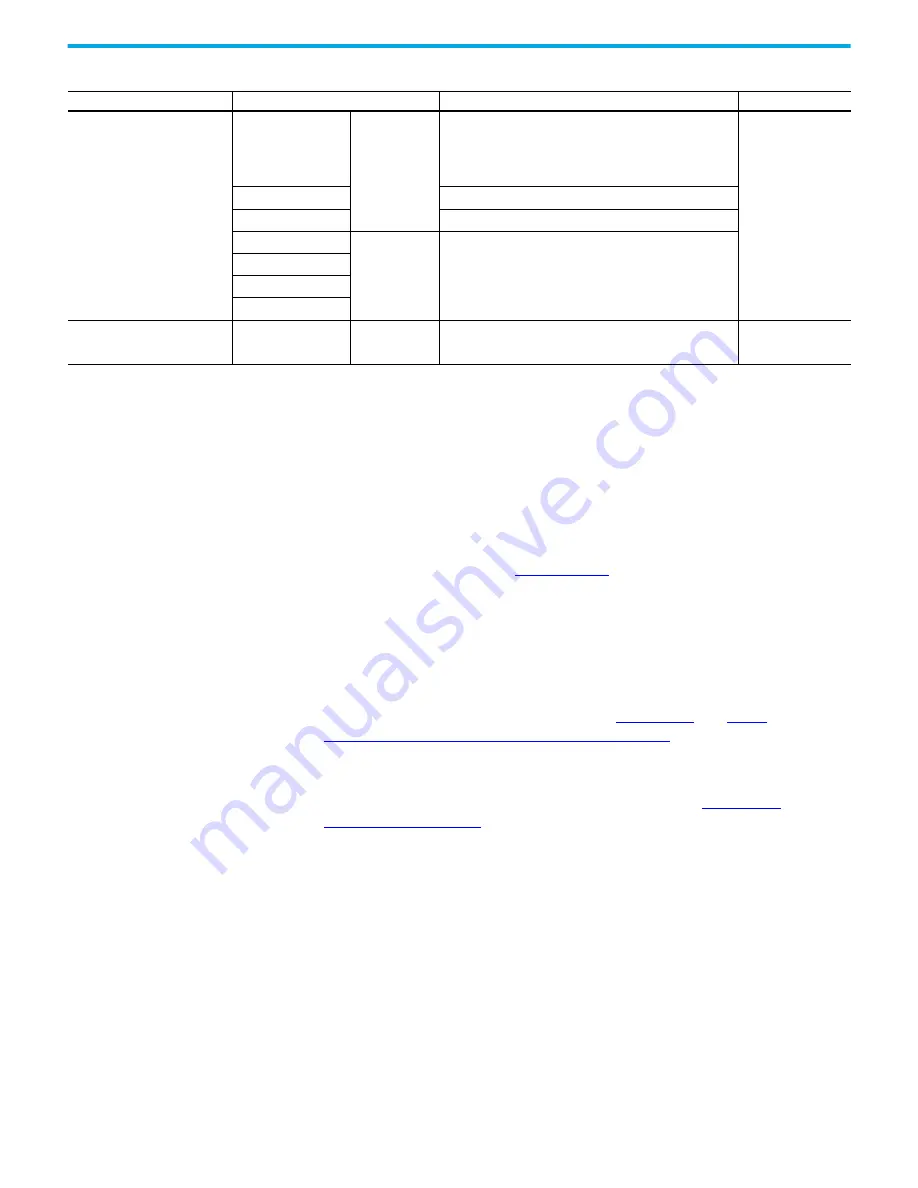
Rockwell Automation Publication 2198-RM006A-EN-P - December 2020
15
Chapter 1 Servo Drive and System Considerations
Table 3 - Motor Feedback Device Options
Cable Lengths
Verify that the feedback cable length in your current Ultra3000 servo drive
system does not exceed the maximum cable lengths for the Kinetix 5300 servo
drives. The maximum cable lengths for the Kinetix 5300 servo drives are:
•
Ethernet cable lengths connecting drive-to-drive, drive-to-controller, or
drive-to-switch must not exceed 100 m (328 ft). Complete a careful
evaluation of your Ethernet media when using a CIP motion solution.
For more information, see Guidance for Selecting Cables for EtherNet/IP
Networks, publication
.
•
Registration and digital input cables greater than 30 m (98.4 ft) must be
shielded.
•
The length of the power and feedback cables for the Kinetix 5300 drives
cannot exceed 50 m (164 ft), although in some cases maximum cable
length is less. The maximum drive-to-motor power and feedback cable
length depends on the AC input power, motor type, and feedback type.
For more information on cable lengths, see
and
Interconnects and Cable Considerations on page 32
Physical Dimensions
The physical sizes of the drive families are different (see
). In most cases, the Kinetix 5300 servo drives are
smaller and fit into the existing space of the compatible Ultra3000 drives;
however, you must verify the physical size of the Kinetix 5300 servo drive.
Control and Auxiliary Power
The control and auxiliary power feature lets the drive maintain logic power
when main power is removed. This allows communication between the
controller and the drive to continue and to maintain position feedback (aside
from absolute feedback).
The Ultra3000 servo drives (2098-DSD-005, -010, and -020) require an external
+5V power supply in applications where it is necessary to maintain logic power
when the AC line voltage is removed. The +24V I/O supply (IOPWR) allows use
of the drive-mounted breakout board with 24V to 5V DC converter (2090-
U3CBB-DM12).
Motor Feedback Device Option
Feedback Type
Description
Feedback Connector
Motor Feedback
Hiperface
High-resolution
single-turn and
multi-turn,
absolute
Applies to Kinetix MPL, MPM, MPF, MPS (-M/S or -V/E); Kinetix
MPAS (ballscrew), MPAR, MPAI, linear actuators; and LDAT-Series
(- xDx) linear thrusters.
15-pin Motor
Feedback (MFB)
Nikon
Applies to Kinetix TLP motors.
Tamagawa
Applies to Kinetix TL (-B) and TLY motors.
Digital AqB
Incremental
Applies to Kinetix MPL (-H) rotary motors, Kinetix MPAS (direct-
drive) linear actuators, LDAT-Series (-xBx) linear thrusters,
Kinetix TLY (-H) servo motors, and Kinetix LDL-series™/
LDC-Series™ linear motors.
Digital AqB with UVW
Sine/Cosine
Sine/Cosine with UVW
Auxiliary Feedback and
Digital Input
(1)
Digital AqB
Incremental
Applies to Digital AqB encoders.
20-pin Auxiliary
Feedback Connector
(1) The auxiliary feedback connector allows configuration of Digital AqB as a load feedback device or a half-axis (feedback only).