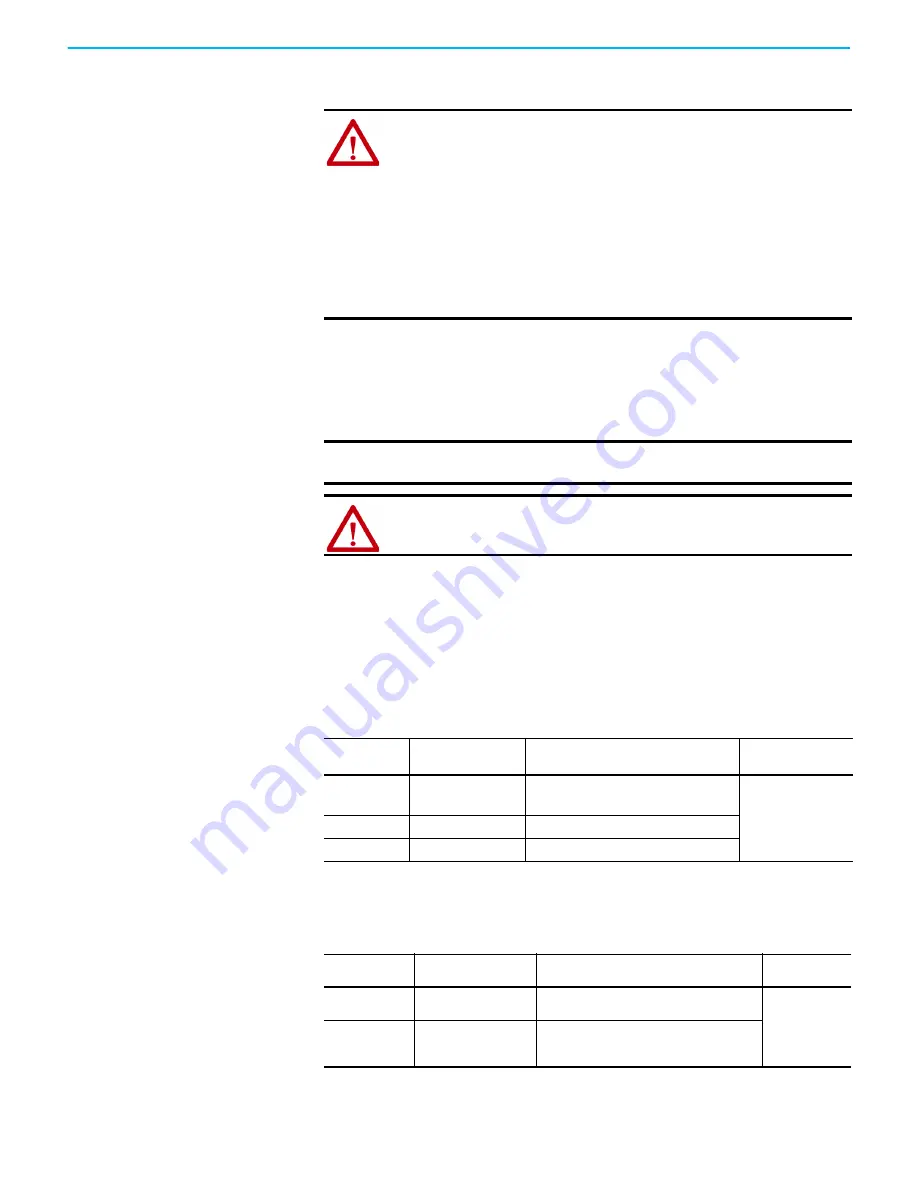
36
Rockwell Automation Publication 520-UM001K-EN-E - August 2021
Chapter 1 Installation/Wiring
I/O Wiring
Motor Start/Stop Precautions
Important points to remember about I/O wiring:
•
Always use copper wire.
•
Wire with an insulation rating of 600V or greater is recommended.
Control and signal wires should be separated from power wires by at least 0.3
m (1 ft).
Signal and Control Wire Types
Recommendations are for 50 °C ambient temperature.
75 °C wire must be used for 60 °C ambient temperature.
90 °C wire must be used for 70 °C ambient temperature.
ATTENTION:
A contactor or other device that routinely disconnects and
reapplies the AC line to the drive to start and stop the motor can cause drive
hardware damage. The drive is designed to use control input signals that will
start and stop the motor. If used, the input device must not exceed one
operation per minute or drive damage can occur.
ATTENTION:
The drive start/stop control circuitry includes solid-state
components. If hazards due to accidental contact with moving machinery or
unintentional flow of liquid, gas or solids exist, an additional hardwired stop
circuit may be required to remove the AC line to the drive. When the AC line is
removed, there will be a loss of any inherent regenerative braking effect that
might be present - the motor will coast to a stop. An auxiliary braking method
may be required. Alternatively, use the drive’s safety input function.
IMPORTANT
I/O terminals labeled “Common” are not referenced to the safety ground (PE)
terminal and are designed to greatly reduce common mode interference.
ATTENTION:
Driving the 4
…
20 mA analog input from a voltage source could
cause component damage. Verify proper configuration prior to applying input
signals.
Recommended Signal Wire
Signal Type/
Where Used
Belden Wire Type(s)
(1)
(or equivalent)
(1) Stranded or solid wire.
Description
Min. Insulation
Rating
Analog I/O & PTC 8760/9460
0.750 mm
2
(18 AWG), twisted pair,
100% shield with drain
(2)
(2) If the wires are short and contained within a cabinet which has no sensitive circuits, the use of shielded wire may not be
necessary, but is always recommended.
300V,
60 °C (140 °F)
Remote Pot
8770
0.750 mm
2
(18 AWG), 3 conductor, shielded
Encoder/Pulse I/O 9728/9730
0.196 mm
2
(24 AWG), individually shielded pairs
Recommended Control Wire for Digital I/O
Type
Wire Type(s)
Description
Min. Insulation
Rating
Unshielded
Per US NEC or applicable
national or local code
–
300V,
60 °C (140 °F)
Shielded
Multi-conductor shielded
cable such as Belden 8770
(or equivalent)
0.750 mm
2
(18 AWG), 3 conductor, shielded.
Summary of Contents for Allen-Bradley PowerFlex 520 Series
Page 8: ...8 Rockwell Automation Publication 520 UM001K EN E August 2021 Table of Contents Notes ...
Page 68: ...68 Rockwell Automation Publication 520 UM001K EN E August 2021 Chapter 2 Start Up Notes ...
Page 236: ...236 Rockwell Automation Publication 520 UM001K EN E August 2021 Appendix F PID Set Up Notes ...
Page 270: ...270 Rockwell Automation Publication 520 UM001K EN E August 2021 Index Notes ...