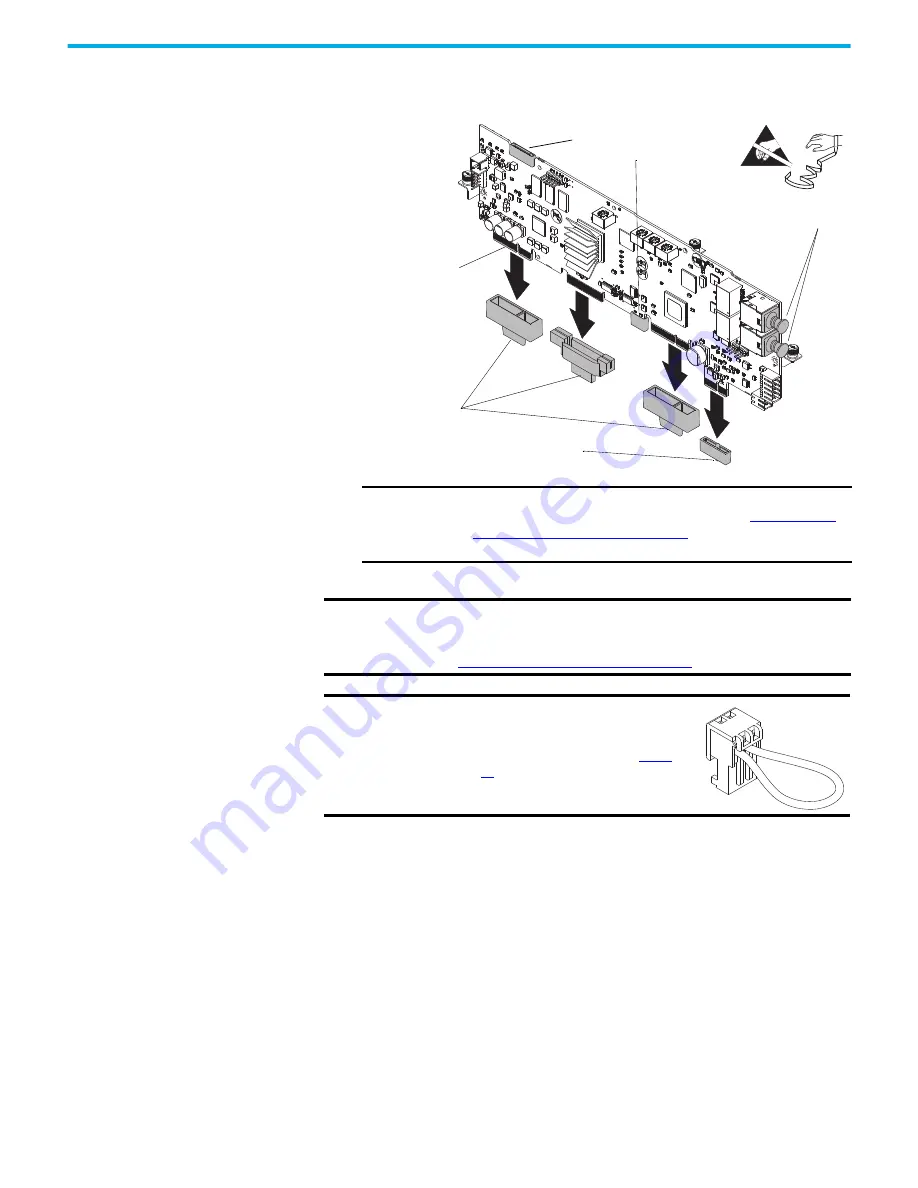
68
Rockwell Automation Publication 750-TG101A-EN-P - June 2022
Chapter 4 Frames 1…5 Renewal Kits Installation
1. For kit catalog number SK-RT-MCB1-PF755-XT only, hold the tab on the
protective cover and carefully remove the cover from the edge connector
on the circuit board. Do not touch the edge connector.
2. Install the main control circuit board in the reverse order of removal.
3. Make any necessary changes to the settings on these main control board
selectors or jumpers:
• Control switch
• Embedded EtherNet/IP address switches
• Hardware enable jumper
• Safety enable jumper
IMPORTANT
If before installation, grease is removed from an edge connector or
is contaminated, do not install the circuit board. See
Grease to an Edge Connector on page 18
for instructions on how to
clean and grease an edge connector.
IMPORTANT
Do not remove protective covers unless used at the time of installation. For
the product to meet the corrosive atmosphere rating, protective covers
must remain installed in unused connectors during storage and operation.
See
Protective Covers on Kits with XT on page 16
for details.
IMPORTANT
Be sure to install jumper J16 into connector P16
on the main control circuit board. See
for details.
Hold Protective Cover by Tab.
Remove Only when Used
Dielectric Grease on Connectors
(Grease is Translucent - Shown
Shaded for Example Only)
Main Control Circuit Board Shown
=
Remove Only when a Torque
Accuracy Module is Installed.
Do Not Remove these Protective Covers
(for Factory User Only).
Remove Only when EtherNet/IP™
Cables are Installed.