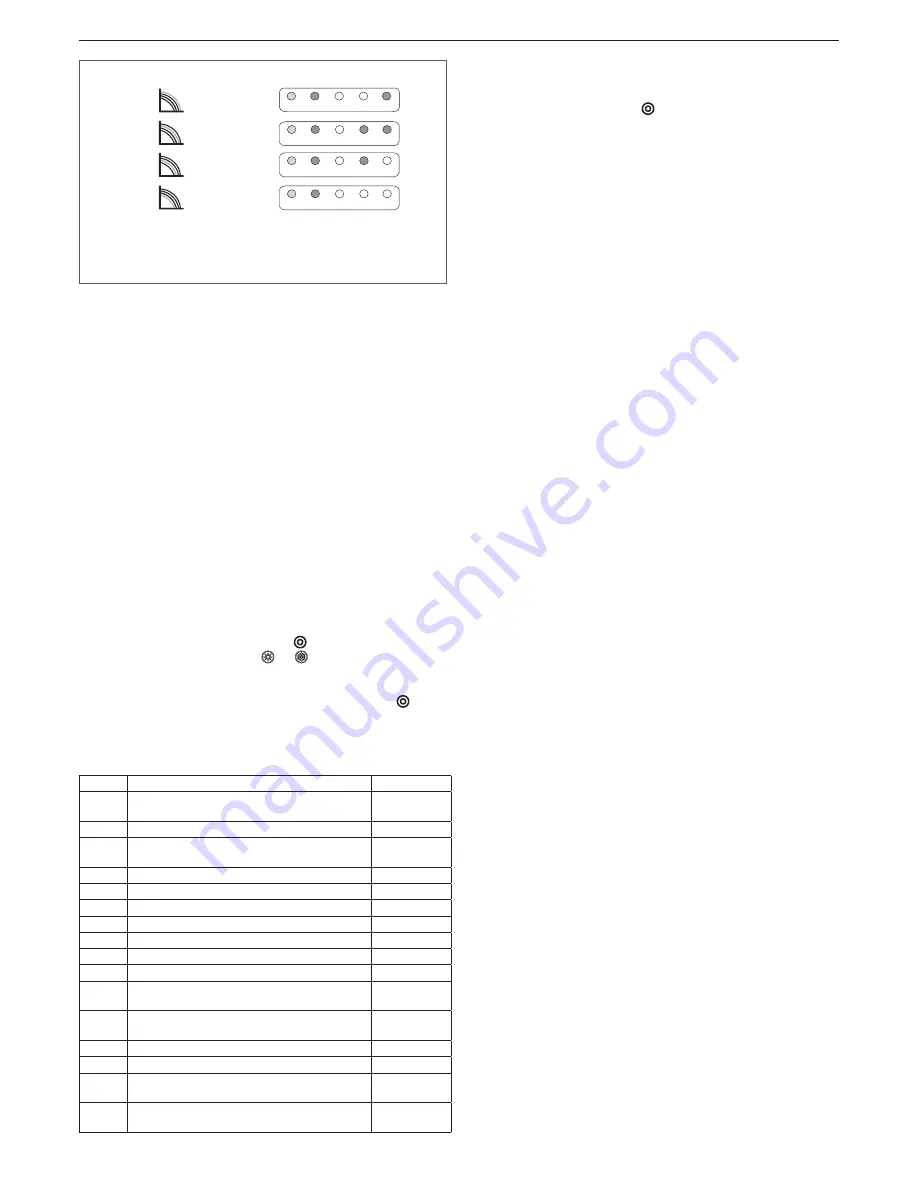
Residence Condens IS n
12
LED 1
rosso
LED 2
giallo
LED 3
giallo
LED 4
giallo
LED 5
giallo
4
3
2 (*)
1
(*) valore settato da fabbrica
7 m
6 m
5 m
4 m
(*) factory set value
R Red
G Yellow
R
G
G
G
G
IMPORTANT
If curves 3 (5 meters) or curve 4 (4 meters) are set, the bypass must
be replaced with that supplied, following the procedure below.
4.6
Bypass replacement (fig. 30)
- Switch off the electrical supply by turning the system's main switch
to "Off".
- Close the taps of the system and drain the heating circuit of the
boiler.
- Extract the bypass body cover fixing clip (1).
- Extract the bypass body cover (2).
- Replace the by-pass valve (3) with that supplied.
- Replace the by-pass body cover and the clip.
4.7
Light signals and faults
Green LED
Off = boiler in stand-by, no flame.
On = burner on, the boiler operates normally.
Red led
In the event of stoppage: display of the fault code only blinking on
the digit.
In the event of lockout: red LED on and fault code blinking on digit.
The error code is not present in status
(off/reset), to make it visi-
ble position the mode selector to
or
(fig. 31).
It is displayed however during the combustion analysis and the an-
ti-freeze phase operations.
To restore the operation, position the function selector to
(off/re-
set) and then return it back to the desired position: summer or winter
mode.
If the reset does not activate the boiler operation, contact the Techni-
cal Assistance Centre.
Code
Description
Lockout type
AL10
Number of ignition attempts exceeded
(flame absent/condensation present)
lockout
AL20
Limit thermostat fault
lockout
AL21
Low temperature thermostat/
condensation pump safety fault
lockout
AL26
Return overtemperature
lockout
AL28
Return line/outlet probe differential fault
lockout
AL29
Flue gases probe overtemperature
lockout
AL34
Tacko fan fault
lockout
AL40
System water pressure low (after 10 minutes)
lockout
AL41
System water pressure low
stop
AL52
General electronic fault
lockout
AL55
Fault due to absence of boiler mode
configuration (corresponding jumper absent)
lockout
AL60
DHW probe fault
see dedicated
section
AL71
Outlet probe fault (open/short circuit)
STOP
AL73
Return line probe fault (open/short circuit)
STOP
AL79
Outlet overtemperature/ return /
outlet probe differential fault
lockout
AL91
Primary heat exchanger cleaning
(call customer service)
Signal
For AL41 faults
Check the pressure on the boiler water gauge; if it is less than 0.5 bar
proceed as follows:
- position the mode selector to
- fill slowly by opening the filling tap outside the boiler (fig. 32) until
the hand of the hydrometer is between 1 and 1.5 bar (fig. 33)
- reposition the mode selector on the required position (summer or
winter).
If the drop in pressure is frequent, contact the Technical Assistance
Centre.
For fault AL60
The boiler is working normally, but does not provide any stability of
the domestic hot water temperature that, in any event, is supplied at
a temperature of around 50°C.
The intervention of the Technical Assistance Centre is required.
For fault AL91
The boiler is equipped with an auto-diagnostic system which, based
on the total number of hours in certain operating conditions, can sig-
nal the need to clean the primary exchanger (alarm code 91). Once
the cleaning operation has been completed, reset to zero the total
hour meter with special kit supplied as an accessory following proce-
dure indicated below (fig. 34):
- disconnect the electrical power supply, unscrew the 4 Allen screws
(A) and remove the control panel (B),
- restore the electrical power supply to the boiler by holding down
the combustion analysis button "CO" (C) for at least 4 seconds.
To verify a successful reset of the counter, switch the power supply to
the boiler off and on again; the value of the counter will be displayed
after the lighting of all segments of the digits.
Note: the meter resetting procedure should be carried out after each
in-depth cleaning of the primary exchanger or if this latter is replaced.
To check the status of the totalled hours, multiply the value read by
100 (e.g. value read 18 = total hours 1.800; value read 1= total hours
100).
4.8
Boiler configuration (fig. 35-36)
The electronic board has a number of jumpers (JP4) that allow to
configure the boiler; access is possible by disconnecting the cover A
of the control panel by means of the clips B after having positioned
the main switch to off.
JUMPER IN POSITION 1:
pre-selection of the most appropriate heating temperature adjust-
ment field based on the type of system.
Jumper not inserted - case A
Standard system 40-80 °C.
Jumper inserted - case B
Floor installation 20-45°C.
During manufacture, the boiler is configured for standard systems.
JUMPER IN POSITION 2: (storage tank with probe)
JUMPER IN POSITION 3: (storage tank with thermostat)
JUMPER IN POSITION 4: (not used)
JUMPER IN POSITION 5: (not used)
JUMPER IN POSITION 6: (not used)
As standard the boiler comes with the jumper in position 3 (stor-
age tank with thermostat); in the event an external storage tank
with probe is required, the jumper must be moved from position
3 to position 2 (case C).
4.9
Setting the thermoregulation
Thermoregulation only works with external sensor connected, so
once installed, connect the device to the appropriate connections
provided on the terminal board of the boiler (see chapter "Electrical
wiring"). This will enable the THERMOREGULATION function.
Choosing the compensation curve (fig. 37-38-39)
The compensation curve for heating maintains a theoretical temper-
ature of 20°C indoors, when the external temperature is between
+20°C and -20°C. The choice of the curve depends on the minimum
external temperature envisaged (and therefore on the geographical
location), and on the delivery temperature envisaged (and therefore
on the type of system). It is carefully calculated by the installer on the
basis of the following formula:
fig. T
Summary of Contents for Residence Condens IS n
Page 208: ...Cod 20116331 03 16 Ed 0 ...