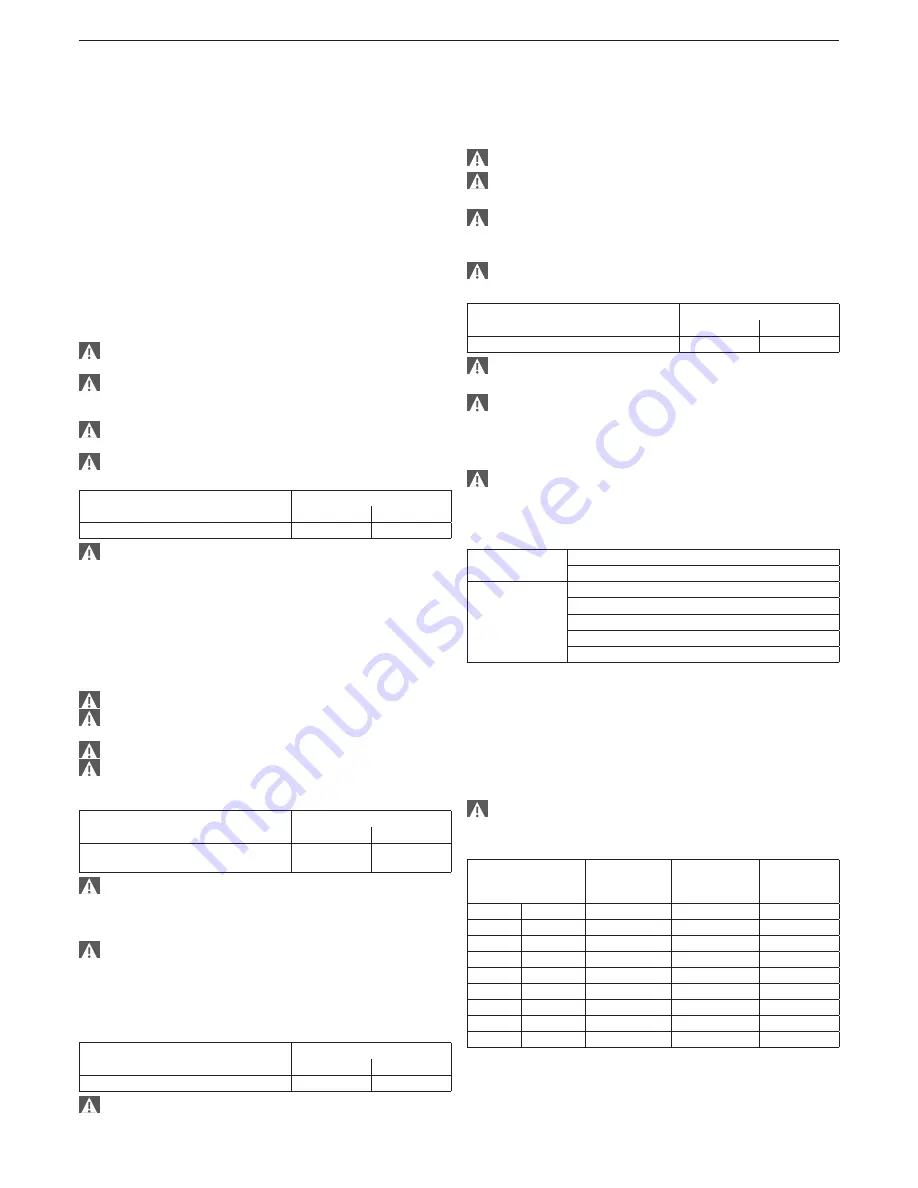
Residence Condens IS n
6
ENGLISH
7
5. Activate a request for DHW as follows: open a tap for 30" per
minute so that the three-way valve cycles from heating to DHW
and vice versa for about ten times (in this situation, the boiler will
go into alarm due to lack of gas, therefore reset it whenever this is
proposed).
6. Continue the sequence until no more air is felt coming from the air
vent valve.
7. Check the system pressure level is correct (the ideal level is 1 bar).
8. Turn off the system filling tap.
9. Turn on the gas tap and ignite the boiler.
3.10
Flue gas outlet and combustion air suction (fig. 18)
The boilers must be equipped with adequate flue gas outlet and air
suction pipes according to the type of installation, to be chosen from
those indicated in the Riello catalogue.
(TYPE B23P-B53P) INSTALLATION
Flue gas discharge pipe ø 80mm
The flue gas outlet pipe can be directed to the most suitable direction
according to installation requirements.
For installation, follow the instructions supplied with the kit.
In this configuration, the boiler is connected to the flue gas out-
let pipe of ø 80 mm through an adaptor of ø 60-80 mm (fig. 19).
In this case, the combustion air is picked up from the boiler
installation room (which must be a suitable technical room with
proper ventilation).
The non insulated flue gas outlet pipes are potential sources of
danger.
Make sure the flue gas discharge pipe is tilted 3° towards the
boiler.
maximum length of the flue
gas discharge pipe ø 80mm
pressure drop
bend 45°
bend 90°
80m
1m
1.5m
"Straight length" means without bends, drainage terminals or
joints.
“AIRTIGHT” INSTALLATION (TYPE C)
The boiler must be connected to concentric or twin flue gas discharge
pipes and air suction pipes, both leading outdoors. The boiler must
not be operated without them.
Concentric pipes (ø 60-100 mm) (fig. 20)
The concentric pipes can be fitted in most suitable direction in rela-
tion to installation requirements.
It is compulsory to use specific pipes.
Make sure the flue gas discharge pipe is tilted 3° towards the
boiler.
Non-insulated outlet pipes are potential sources of danger.
The boiler automatically adapts ventilation according to the
type of installation and the length of the duct. Do not obstruct
or choke the combustion air suction pipe in any way.
straight length of concentric
pipe ø 60-100mm
pressure drop
bend 45°
bend 90°
7,85 m (horizontal)
8,85 m (vertical)
1.3m
1.6m
"Straight length" means without bends, drainage terminals or
joints.
For installation, follow the instructions supplied with the specific ac-
cessory kit for condensing boilers.
The use of a longer pipe causes a loss of output of the boiler.
Concentric pipes (ø 80-125) (fig. 21)
The appropriate adaptor kit must be installed for this configuration.
The concentric pipes can be fitted in most suitable direction in rela-
tion to installation requirements. For installation, follow the instruc-
tions supplied with the specific kit for condensing boilers.
straight length of concentric
pipe ø 80-125mm
pressure drop
bend 45°
bend 90°
14,85m
1m
1.5m
"Straight length" means without bends, drainage terminals or
joints.
Twin pipes (ø 80 mm) (fig. 22-23)
The twin pipes can face in the direction most suited to the installation
requirements.
The suction pipe of the combustion air must be connected to the
input after removing the cap fixed with three screws. The flue gases
discharge pipe must be connected to the flue gases outlet.
It is compulsory to use specific pipes.
Make sure the flue gas discharge pipe is tilted 3° towards the
boiler.
The boiler automatically adapts the purging to the type of in-
stallation and the length of the pipes. Do not obstruct or choke
the pipes in any way.
For the indication of the maximum lengths of the single pipe,
refer to the charts (fig. 24).
straight pipe length
twin pipes ø 80mm
pressure drop
bend 45°
bend 90°
42+42 m
1m
1.5m
"Straight length" means without bends, drainage terminals or
joints.
The use of a longer pipe causes a loss of output of the boiler.
Twin pipes ø 80 with ducting Ø 60 and Ø 80 (fig. 25)
Thanks to the boiler characteristics, a flue gas discharge pipe ø 80
can be connected to the ducting ranges ø 60 and ø 80.
For the ducting, you are advised to make a project calculation
in order to respect the relevant standards in force.
The table shows the standard configurations allowed.
Table of standard pipe configurations (*)
Air suction
1 bend - 90° ø 80
4.5 m pipe ø 80
Flue gas
discharge
1 bend - 90° ø 80
4.5 m pipe ø 80
Reduction from ø 80 to ø 60
90° smoke pipe standard bend ø 60 or ø 80
For ducting pipe lengths see table
(*) Use flue gas system accessories in plastic (PP) for condensing
boilers.
The boilers are factory set to:
- 30 IS n: 5.600 rpm (DHW), 4.700 rpm (CH), and the maximum
length that can be reached is 14m for the ø 60 pipe and 75m for
the ø 80 pipe.
Should it be necessary to achieve greater lengths, compensate the
pressure drop with an increase in the r.p.m. of the fan, as shown in
the adjustments table, to ensure the rated heat input.
The minimum calibration is not modified.
Adjustments table
Table of adjustments for Residence Condens 30 IS n
Maximum number of
fan rotations
(rpm)
Pipes Ø 60
maximum
length
Pipes Ø 80
maximum length
ΔP at boiler
output with
max. length
DHW
CH
m
m
Pa
5.600
4.700
14
75
145
5.700
4.800
19
104
183
5.800
4.900
21 (*)
117 (*)
200
5.900
5.000
159
255
6.000
5.100
190
295
6.100
5.200
217
330
6.200
5.300
253
377
6.300
5.400
301
440
(*) Length that can be installed with pipes in class P1
.
The configurations Ø 60 show test data verified in the laboratory.
In the case of installat ions that differ from those indicated in the
“standard configuration” and "adjustments" tables, refer to the equiv-
alent linear lengths Ø 80 - Ø 60 below.
Summary of Contents for Residence Condens IS n
Page 208: ...Cod 20116331 03 16 Ed 0 ...