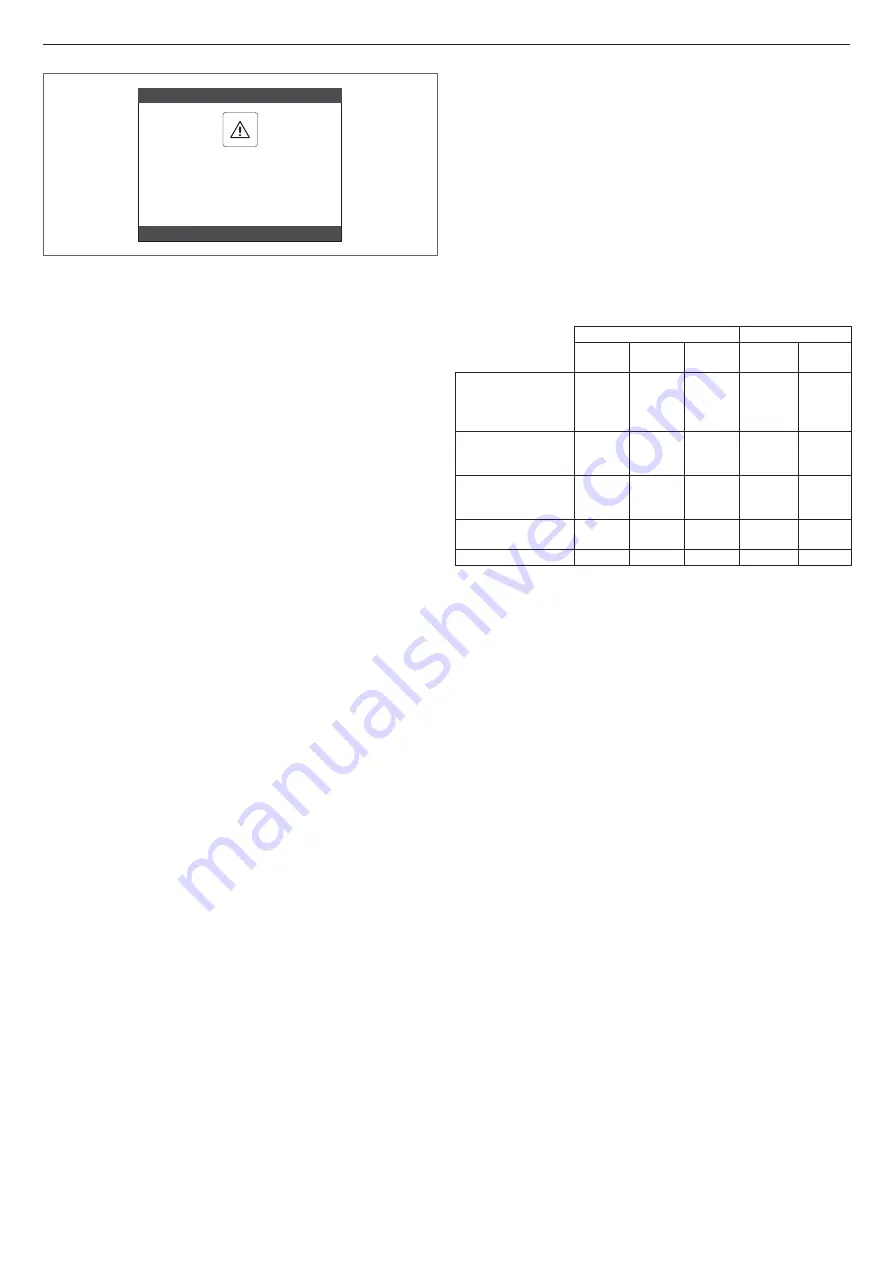
6
FAMILY CX
WRONG CONFIGURATION
OPENTHERM CONNECTED
High voltage connections
The connection to the mains supply must be made via a separation device
with an omnipolar opening of at least 3.5 mm (EN 60335/1 - category 3).
The appliance works with alternating current at 230 Volt/50 Hz, and is in
compliance with Standard EN 60335-1.
It is obligatory to make the connection with a safe ground/earth, in
compliance with current directives.
b
The installer is responsible for ensuring the appliance is suitably
earthed; the manufacturer will not be liable for any damage resulting
from an incorrect or absent earth connection
b
It is also advisable to respect the phase-neutral connection (L-N).
b
The earth conductor must be a couple of cm longer than the others.
b
To create the seal of the boiler use a clamp and tighten it on the cable
grommet used.
The boiler can operate with a phase-neutral or phase-phase (not fl oating)
power supply. For power supplies that are not earthed, it is necessary to
use an isolating transformer with earth-anchored secondary.
It is forbidden to use gas and/or water pipes to earth electrical appliances.
Use the power cable supplied to connect the boiler to the mains power
supply. If the power cable has to be replaced, use a HAR H05V2V2-F, 3 x
0.75mm² cable, Ø max external 7 mm.
3.11 Gas connection
The connection of the gas supply must be carried out in compliance with
current installation standards.
Before carrying out the connection, check that the type of gas is that for
which the appliance is set up.
3.12 Removing the casing (Fig. 12)
To access the components inside, remove the casing as indicated below:
- fi nd and unscrew the 2 screws (
A
) fi xing the casing to the boiler levering
the two fi xing clips (C), detach the bottom part of the casing
- lift the casing upwards to release it from the top tabs (
B
), then remove it.
WARNING
b
If removing the side panels, put them back in their initial position,
referring to the adhesive labels on their walls.
b
If the front panel is damaged it must be replaced.
b
The noise absorbing panels inside the front and side walls ensure the
airtight seal for the air supply duct in the installation environment.
b
It is therefore CRUCIAL after the dismantling operations to correctly
reposition the components to ensure the boiler's seal is eff ective.
3.13 Flue gas exhaust and combustion air suction (Fig. 13)
To evacuate the combustion products, refer to UNI 7129-7131. Always
comply with local standards of the Fire Department, the Gas Company and
with possible municipal dispositions.
The evacuation of the combustion products is carried out by a centrifugal
fan and the control board constantly monitors that it is operating correctly.
It is essential for the evacuation of the fl ue gases and the adduction of the
boiler's combustion air that only original pipes be used (except C6) and that
the connection is made correctly as shown in the instructions provided with
the fl ue gases accessories.
A single fl ue can be connected to several appliances provided that every
appliance is the condensing type.
The boiler is a C-type appliance (with airtight chamber), and must therefore
have a safe connection to the fl ue gas discharge pipe and to the combustion
air suction pipe; these both carry their contents outside, and are essential
for the operation of the appliance.
Both concentric and twin terminals are available.
Suction/discharge pipes length table
Maximum straight length
Pressure drop
25
KIS
30
KIS
35
KIS
Bend
45°
Bend
90°
Flue gases pipe
Ø 80 mm ("forced
open” installation)
(type B23P-B53P)
110 m
65m
65m
1 m
1.5 m
Concentric pipe
Ø 60-100 mm
(horizontal)
10 m
6 m
6 m
1.3m
1.6m
Concentric pipe
Ø 60-100 mm
(vertical)
11 m
7 m
7 m
1.3m
1.6m
Concentric pipe
Ø 80-125 mm
25 m
15 m
15 m
1 m
1.5 m
Twin pipe Ø 80 mm
60+60 m 33+33 m 35+35 m
1 m
1.5 m
b
The straight length includes the fi rst bend (connection into the boiler),
terminals and joints. An exception is made for the vertical Ø 60-100
mm coaxial pipe, whose straight length excludes bends.
b
The boiler is supplied without the fl ue gas exhaust/air suction kit,
since it is possible to use the accessories for condensing appliances
that best fi t the installation characteristics (see RIELLO catalogue).
b
The maximum lengths of the pipes refer to the fl ue accessories
available in the RIELLO catalogue.
b
It is compulsory to use specifi c pipes.
b
The non insulated fl ue gas outlet pipes are potential sources of
danger.
b
The use of a longer pipe causes a loss of output of the boiler.
b
Make sure the fl ue gas discharge pipe is tilted 3° towards the boiler.
b
The exhaust pipes can face in the direction most suited to the
installation requirements.
b
As envisaged by current legislation, the boiler is designed to take
in and dispose of fl ue gas condensate and/or meteoric water
condensate deriving from the fl ue gas discharge system using its
own siphon.
b
if a condensate relaunch pump is installed, check the technical
data (provided by the manufacturer) regarding output, to ensure it
operates correctly.
“Forced open” installation (B23P-B53P)
(Fig.14)
In this confi guration the boiler is connected to the ø 80 mm fl ue gases
discharge pipe by means of an adaptor.
Position the adaptor so that the Ø 60 pipe goes fully into the fl ue gases
turret of the boiler.
- Once positioned, make sure that the 4 notches
(A)
on the fl ange connect
to the groove
(B)
on the Ø 100 of the adaptor.
- Fully tighten the screws
(C)
that tighten the two locking terminals of the
fl ange so the adaptor itself is restrained.
Coaxial pipes (ø 60-100 mm)
(Fig. 15)
- Position the bend so that the Ø 60 pipe goes fully up against the fl ue
gases turret of the boiler.
- Once positioned, make sure that the 4 notches
(A)
on the fl ange connect
to the groove
(B)
on the Ø 100 of the bend.
- Fully tighten the screws
(C)
that tighten the two locking terminals of the
fl ange so the bend itself is restrained.