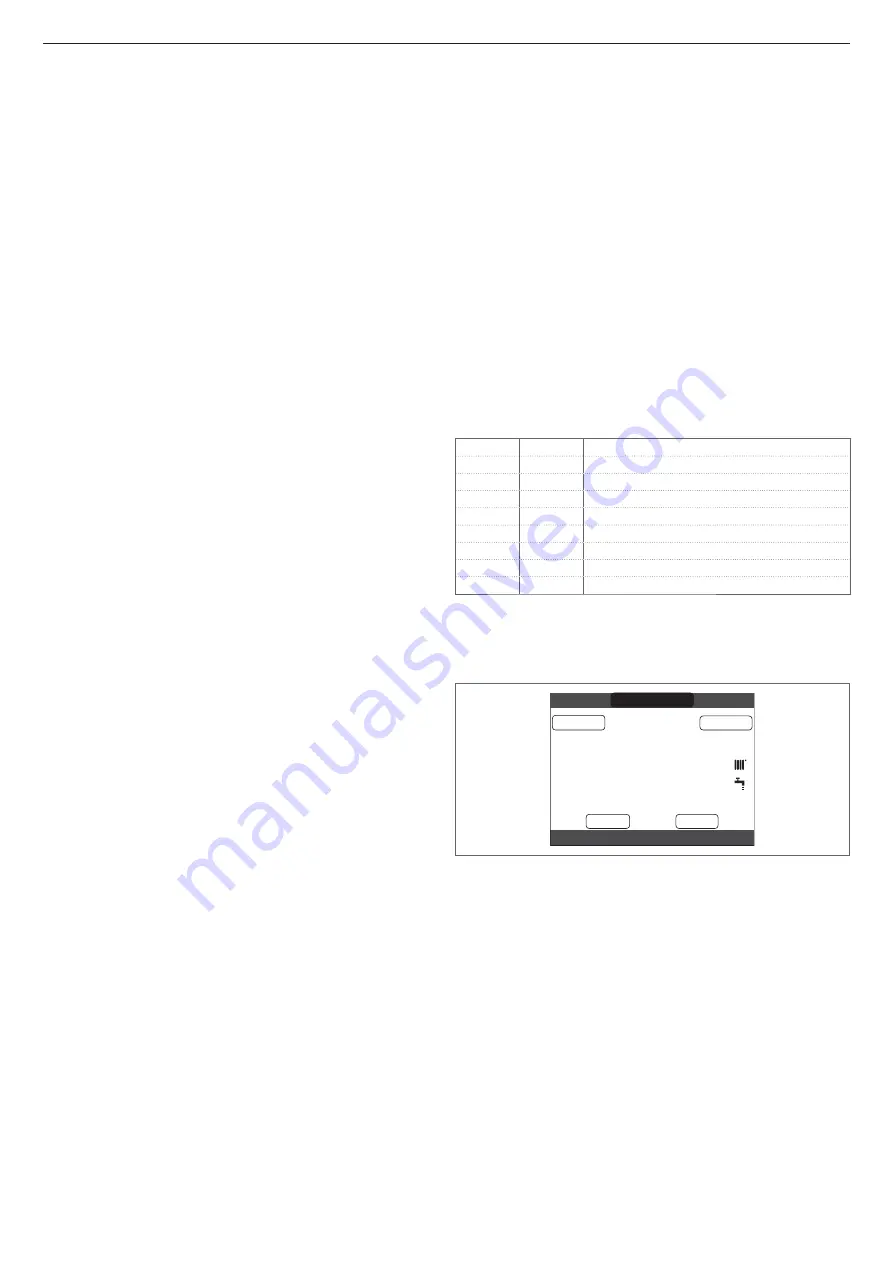
5
ENGLISH
ANTI-FREEZE SYSTEM (Fig. 7)
The boiler is fi tted as standard with an automatic anti-freeze system that
activates when the temperature of the water in the primary circuit falls below
5°C. This system is always active and provides protection for the boiler up
to an air temperature in the installation area of -5°C.
b
To take advantage of this protection (based on burner operation),
the boiler must be able to switch itself on; any lockout condition
(for ex. due to a lack of gas or electrical supply, or the intervention
of a safety device) therefore deactivates the protection.
In normal operating conditions, the boiler can protect itself against frost.
If the machine is left without power for long periods in areas where
temperatures may fall below 0°C, and you do not want to drain the heating
system, you are advised to add a specifi c, good quality anti-freeze liquid to the
primary circuit. Carefully follow the manufacturer's instructions with regards
not only the percentage of anti-freeze liquid to be used for the minimum
temperature at which you want to keep the machine circuit, but also the
duration and disposal of the liquid itself.
For the hot domestic water part, we recommend you drain the circuit.
The boiler component materials are resistant to ethylene glycol based
antifreeze liquids.
MINIMUM DISTANCES (Fig. 8a-8b)
To ensure access to the boiler for normal maintenance operations, respect
the minimum installation clearances envisaged.
For correct appliance positioning, bear in mind that:
- it must not be placed above a cooker or other cooking device
- it is forbidden to leave infl ammable products in the room where the boiler
is installed
- heat-sensitive walls (e.g. wooden walls) must be protected with proper
insulation.
b
When installing it is ABSOLUTELY NECESSARY to provide the
spaces necessary for the introduction of the instrument for analysing
the combustion. We have provided a sample diagram where the
distances between the boiler and wall unit /recess have been
obtained using an instrument with a length of 300 mm. Longer
instruments require more space.
3.8
Installation of condensate drain pipe (Fig. 9)
b
Before starting the boiler, even just temporarily, the SRD device
supplied must be installed .The manufacturer does NOT accept
liability for damage to persons or objects caused by the boiler
operating without the SRD device being installed correctly.
For the installation proceed as follows:
- remove the plug (
T
) from the siphon
- fi x the SRD device to the siphon (Fig. 9a), placing the gasket in-between,
screwing it on all the way and checking its seal
- connect the condensate discharge pipe (Fig. 9b) supplied as standard
with the product, then drain the condensate into a suitable drainage
system in compliance with current norms.
b
If it is not possible to fi t the SRD device due to the interference
with other objects under the boiler, it is possible to fi t it in a diff erent
position by inserting a connecting pipe between the SRD device and
the siphon in order to provide a fully airtight seal. The SRD device
should always be positioned VERTICALLY in order to ensure it
functions correctly
3.9
Positioning the wall-mounted boiler and hydraulic
connections (Fig. 10)
The boiler comes as standard with a boiler support plate. The position and
dimension of hydraulic fi ttings are shown in the detail drawing.
For the assembly, proceed as follows:
- fasten the boiler support plate (F) to the wall and use a spirit level to
make sure it is perfectly horizontal
- mark the 4 holes (ø 6 mm) envisaged for securing the boiler support
plate (F)
- make sure that all measurements are exact, then drill the wall using drill
tips with the diameters indicated above
- fi x the plate with the built-in template (G) to the wall.
- fi x the safety valve pipe supplied in the documentation envelope onto the
coupling of the safety valve (S), then connect it to an adequate discharge
system.
Make the hydraulic connections.
M
heating delivery
3/4”
AC
hot water outlet
1/2”
G
gas
R
heating return line 3/4”
AF
cold water inlet
1/2”
3.10 Electrical wiring (Fig. 11a-11b-11c)
Low voltage connections
Carry out the low voltage connections as follows:
- use the external cable box supplied as standard
- unscrew the fi xing screws of the cover
(V)
- carry out the connections as shown in the detailed drawing (Fig. 11a-11b)
b
We recommend using conductors with a section no larger than
0.5mm
2
.
b
In the event of TA or TBT connection, remove the relative
jumpers on the terminal board (Fig. 11c).
- Close the box with the screws
(V)
that were removed beforehand.
- Press the two tabs on the sides of the box to position it correctly in the
seat on the boiler (bottom left on the inside) sliding it towards the top
inside the relative slide bars.
- Tighten the safety screw (
V1
).
b
If the low voltage electrical connection box is not connected the
boiler does not ignite.
1-2-3-4
(- A B +)
Bus 485
5 - 6
TA
Room thermostat (contact without voltage)
7 - 8
TBOL
Not used
9-10
TBT
Low temperature limit thermostat
11 - 12
SE
Outdoor temperature sensor
13 - 14
OT+
Open therm
15 - 16
SBOL
Not used
17 - 18
X1
Not used
19 - 20
X2
Not used
OTBus remote control connection
When an OTBus remote control is connected to the system, the boiler
display shows the message “Open Therm Connected”, while some of its
functions are disabled and transferred to the OTBus remote control that
takes control of the domestic hot water and heating functions regarding the
main zone.
42
°C
MENU
STATE
SET
INFO
OPENTHERM CONNECTED
PLANT
HOT WATER TEMPERATURE
FRI
1.5
bar
18/05/2013
12:17
In particular on the boiler display:
- it is no longer possible to set the boiler OFF/WINTER/SUMMER status (it
is set by the OTBus remote control)
- it is no longer possible to set the domestic hot water setpoint (it is set by
the OTBus remote control)
- it is not possible to activate the CHIMNEY SWEEPER function if a OTBus
remote control is connected to the boiler
INFO menu
The domestic hot water setpoint is displayed in the INFO menu
in the place of the fl ow meter fl ow rate value
The heating setpoint set on the boiler display is used only if there are
heat requests from the TA and the OTBus remote control does not have a
request. We should point out that it is not possible, with the OTBus remote
control connected, to change the values of the parameters ACTUATION
TYPE and REQUEST TYPE of the main zone.
Note: an OT+ remote control cannot be connected if the system
already has a REC10H or BE16 interface boards. in this case the
system gives the following error message: