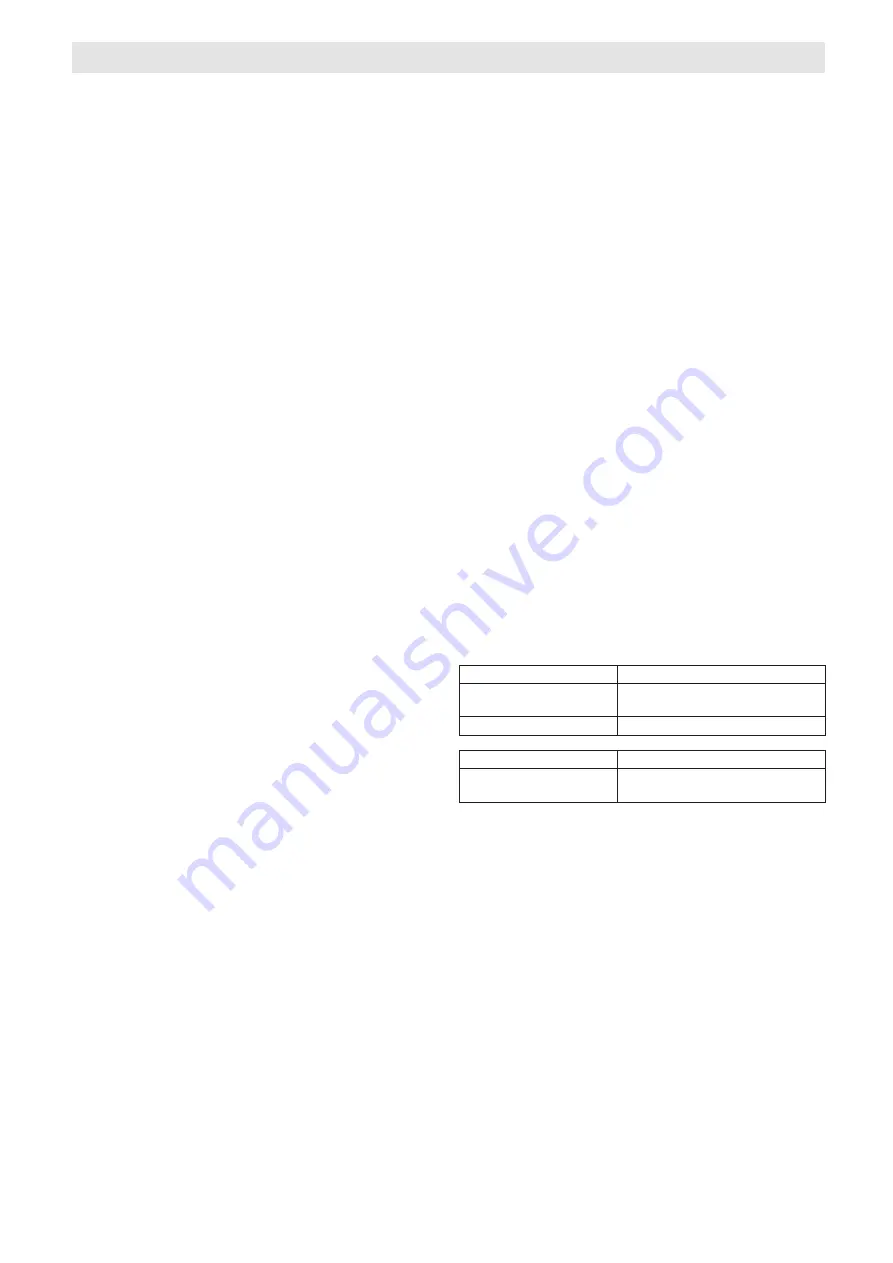
43
NOTE:
please refer to section 4, section 4.1 and use the ap-
propriate PPE when carrying out any of the actions or proce-
dures contained within this section.
8.1 CHECKING APPLIANCE OPERATION
When carrying out any repairs or servicing to the appliance,
the relevant commissioning procedure must be undertaken to
ensure the continued safe operation of the appliance. Particular
attention should be made to ensure gas tightness, water
tightness and the electrical integrity of the appliance.
8.2 APPLIANCE MODES OF OPERATION
NOTE
There must be sufficient system water pressure (min. 0.5 bar)
to ensure the water pressure switch is activated. If there is
insufficient system pressure the pump and fan will be prevented
from operating and the low-pressure fault code will be indicated.
8.2.1 OFF
When the appliance has been set to OFF via the REC10 UI,
the following functions will remain active:
• frost-protection system
• pump anti-block.
8.2.2 ON-BOARD FUNCTIONS
•
FROST-PROTECTION:
this function is only active when
there are no requests for heating or HW. If the temperature
drops below 5°C, the boiler will operate on minimum power
until the temperature of the thermistors reaches 35°C for CH
and 55°C for DHW. Thereafter the pump & fan will over-run
for 30-seconds.
•
ANTI-CYCLE FUNCTION:
the anti-cycle function ensures the
burner remains switched off for at least 3-minutes after the
set-point hysterisis (set-point + 5-deg) for CH heat request.
•
PUMP ANTI-BLOCK FUNCTION:
when there has been no
heating or HW request for 24-hours, the anti-block cycle
is activated. The pump will be activated for a period of
30-seconds.
8.2.3 HEATING MODE
When a ‘heating’ request is generated via the connected
external control/s and/or the REC10 UI, the appliance will
operate in the heating mode. The pump and fan will be activated
via the flow temperature sensor. When the fan is sensed to
be operating correctly (tacho signal), the ignition sequence
commences. Ignition is sensed by the electronic circuit to
ensure flame stability at the burner. Once successful ignition
has been achieved, the electronic circuitry increases the gas
rate to 75% for a period of 15 minutes.
The speed of the fan and therefore the output of the boiler is
determined by the temperature of the water sensed by the
flow temperature sensor, consequently a high temperature
at the flow sensor results in a lower fan speed. As the water
temperature increases, the temperature sensors – located
on the flow pipe of the boiler – reduce the fan speed via the
electronic circuitry. Depending on the load, either the water
temperature will continue to rise until the set point is achieved or
the water temperature will fall whereby fan speed will increase
relative to the output required. When the boiler has reached
the set point (+ hysterisis), the burner will switch off. The built-
in anti-cycle device prevents the burner from re-lighting for
approximately 3-minutes.
When the temperature of the flow sensor falls below the set
point (- hysterisis), the burner will re-light.
NOTE
If burner ignition is not detected at the first attempt, the appliance
will repeat the ignition sequence another two times (3-times
in total) before going to lockout. When the set-point has been
reached as measured at the primary thermistor, the appliance
will begin the modulation phase whereby the fan and gas valve
will continuously modulate to maintain the set-point.
If the temperature continues to rise and exceeds the set-point
by 5°C (hysterisis), the burner will shut down. A new ignition
sequence will be enabled when the 3- minute anti-cycle has
been performed and the temperature at the primary thermistor
has dropped 5°C (hysterisis) below the set-point.
NOTE
When the request for heating and/or hot water has been
satisfied, the appliance pump and fan may continue to circulate
to dissipate any residual heat within the appliance.
ATTENTION
Gas type and appliance outputs are factory set by default, at
the values declared in the specification data in section 2.
Vokera cannot accept any responsibility for any damage or
malfunction that has been caused as a result of tampering
or incorrect set up of this appliance during installation or
commissioning.
8.3 CHECKING THE EXPANSION VESSEL
Carry out the component removal procedure. You must ensure
that the boiler is completely drained of water. Using a suitable
pressure gauge, remove dust cap on expansion vessel and
check the charge pressure. The correct charge pressure should
be 1.0 bar ± 0.1 bar. If the charge pressure is less, use a suitable
pump to increase the charge.
NOTE
You must ensure the drain valve is in the open position whilst
re-charging takes place. Replace the dust cap and carry out
the relevant commissioning procedure (section 6).
8.4 EXTERNAL FAULTS
Before carrying out any faultfinding or component replacement,
ensure the fault is not attributable to any aspect of the installation.
8.4.1 INSTALLATION FAULTS
Symptom
Possible cause
No ignition
Check wiring/check electrical
supply/check gas supply
No Heating and/or HW
Check external controls
Fault
Possible cause
Fault code
Check gas supply, check flue
system
8.5 ELECTRICAL CHECKS
Any electrical checks must be carried out by a suitably qualified
person.
8.5.1 EARTH CONTINUITY TEST
Isolate the appliance from the electrical supply, and using a
suitable multi-meter carry out a resistance test. Connect test
leads between an appliance earth point and the earth wire of
the appliance supply cable. The resistance should be less than
1 OHM. If the resistance is greater than 1 OHM check all earth
wires and connectors for continuity and integrity.
8.5.2 SHORT CIRCUIT CHECK
Isolate the appliance from the electrical supply, and using a
suitable multi-meter, carry out a short circuit test between the
Live & Neutral connections at the appliance terminal strip.
Repeat above test on the Live & Earth connections at the
appliance terminal strip.
NOTE
Should it be found that the fuse has failed but no fault is
indicated, a detailed continuity check will be required to trace
the fault. A visual inspection of components may also assist in
locating the fault.
8. SECTION - CHECKS, ADJUSTMENTS AND FAULT FINDING