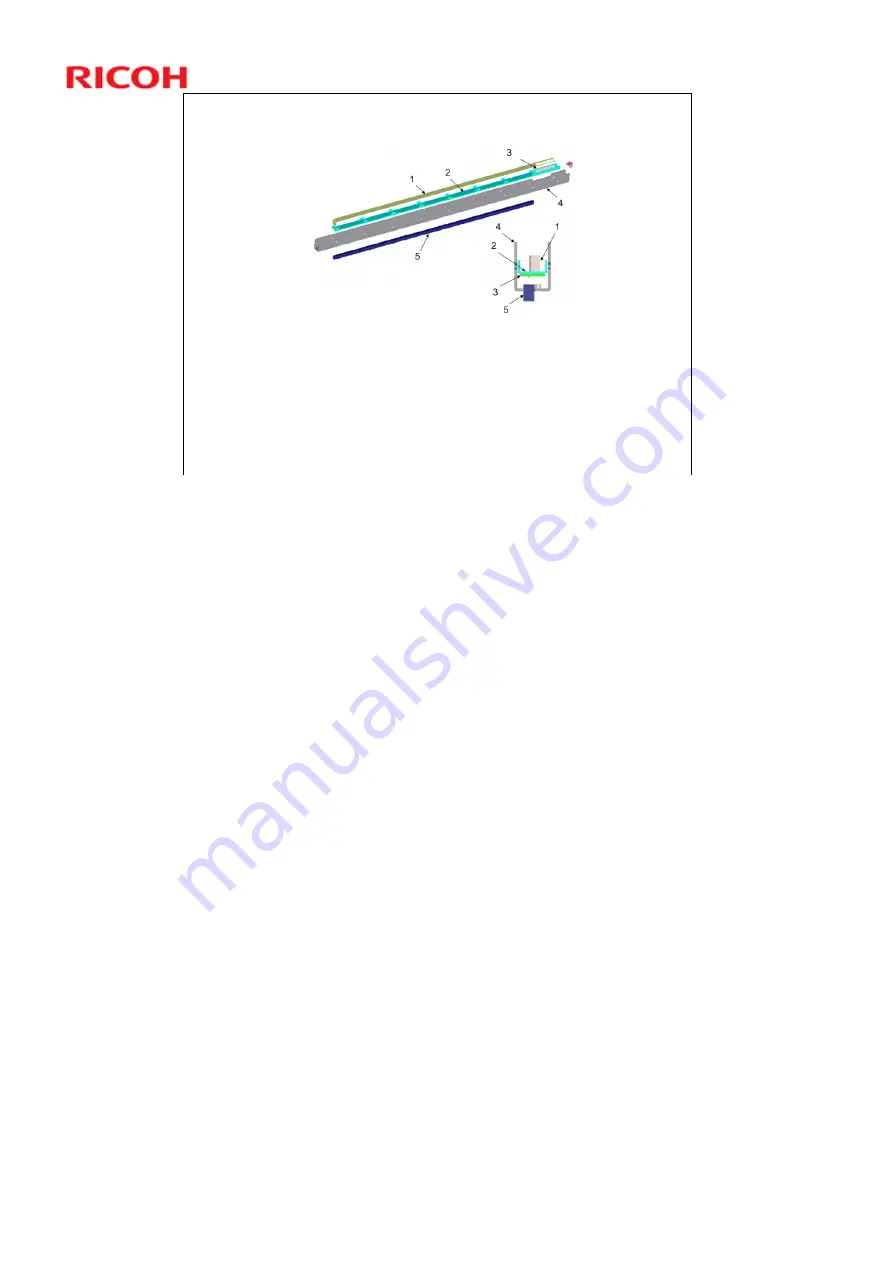
54
Ti-P1 Training
Slide 54
Components of the LED Array
The LED array consists of the following parts.
1. Sheet
2. Base
3. LED board
4. Frame
5. SLA (Self-focusing Lens Array)
The LED array is replaced as one complete unit. The individual
components shown above cannot be replaced in the field.
No additional notes