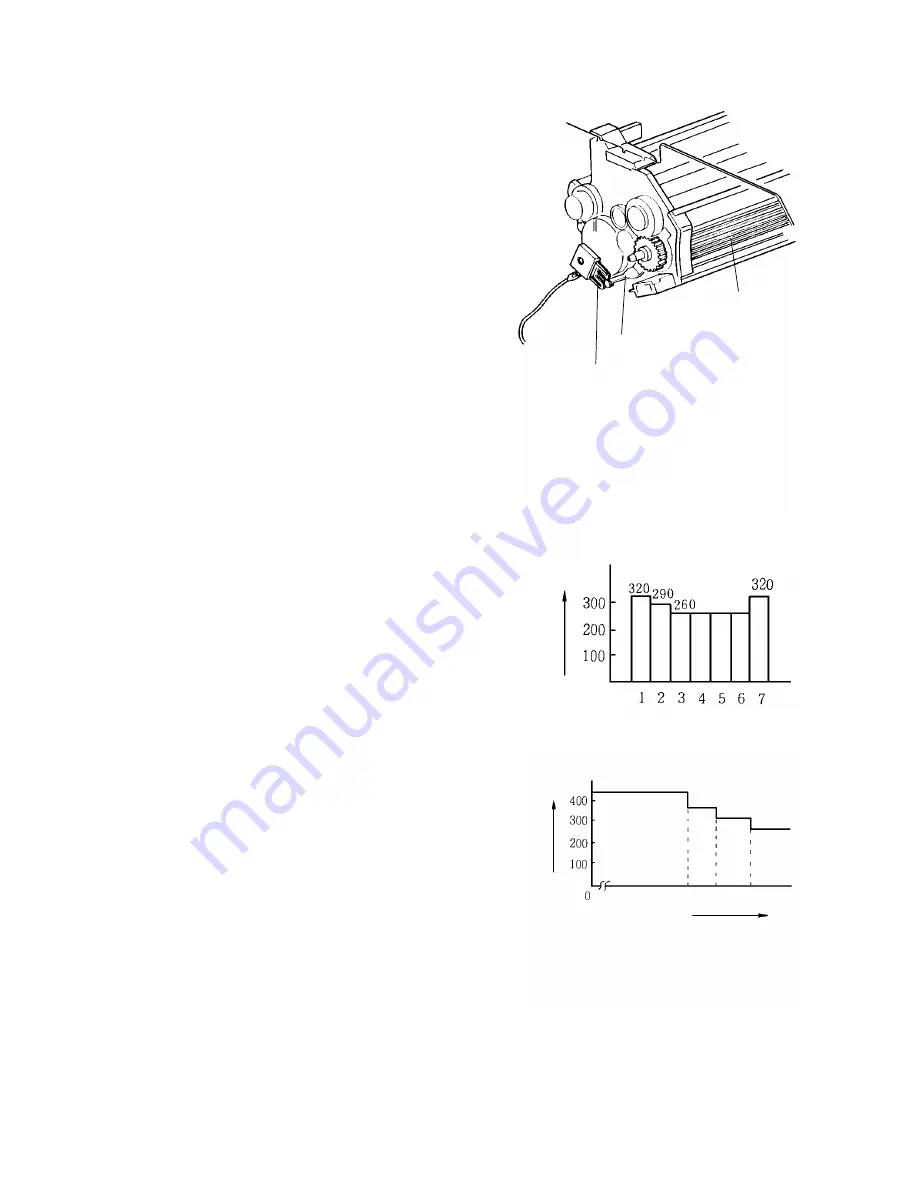
4. Bias
The charge on the drum surface is dissipated
in direct proportion to the intensity of the
reflected light from the original.
As the light intensity corresponding to the dark
areas of the image is weak, the drum potential
remains.
On the other hand, the majority of the drum
potential corresponding to the original
background disappears. However, the potential
does not disappear completely.
Therefore, a positive development bias is
applied to the development roller to prevent the
drum areas corresponding to the background
from being developed (this prevents dirty
background).
The development bias voltage is supplied from
the power pack C/B to the bias terminal via the
bias terminal plate.
1. Bias Control Methods
a. Manual Image Density Control
When image density is set manually,
the development bias is changed as
shown.
The voltage applied to the exposure
lamp also changes.
b. Automatic Image Density Selection
When automatic image density mode is
selected, the CPU measures the
background density of the original
through the ADS sensor and changes
the development bias.
Bias Terminal
Development
Roller
Bias Terminal Plate
From
power pack
- C/B
(at 30°C)
Bias
Voltage
Manual ID Level
(at 30°C)
Bias
Voltage
ADS Data
- 52 -
Summary of Contents for FT5034
Page 1: ...SERVICE MANUAL FT5034C...
Page 3: ...1 INSTALLATION 1 1 INSTALLATION REQUIREMENTS 3 1 2 INSTALLATION PROCEDURE 4 2...
Page 8: ...2 OVERVIEW 2 1 SPECIFICATIONS 8 2 2 GUIDE TO COMPONENTS 9 7...
Page 10: ...2 2 GUIDE TO COMPONENTS 1 Operation Panel 9...
Page 11: ...2 Indicator Panel 10...
Page 12: ...3 COPY PROCESS 3 1 COPY PROCESS DIAGRAM 12 11...
Page 115: ...8 TROUBLESHOOTING 114...