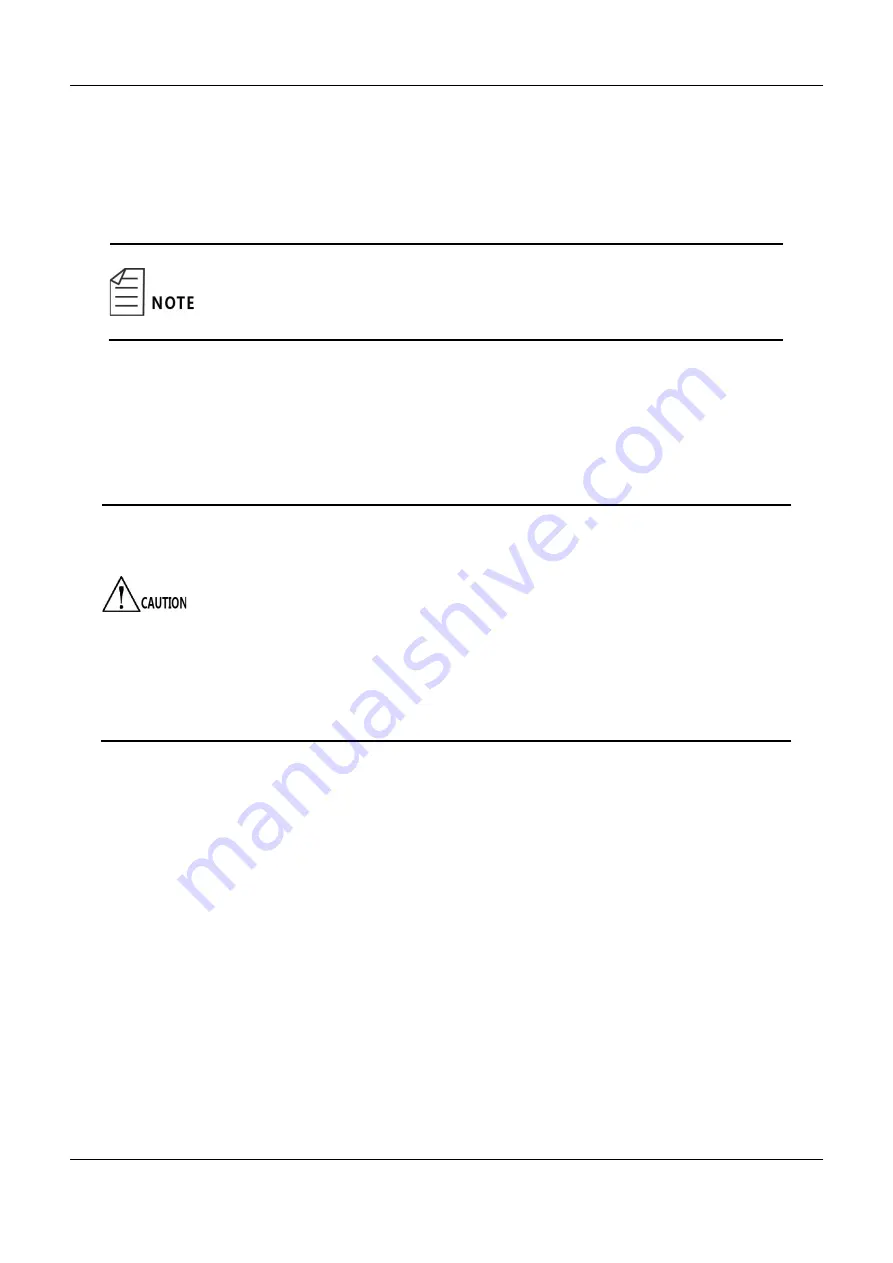
Chapter 3 Robot Debugging and Components Maintenance
Document Version V1.1.0 (03-07-2022)
10
Chapter 3 Robot Debugging and Components Maintenance
The axis joints of MS6MT Robot are assembled in a modular
manner. If the internal components of the module are damaged, the
whole module needs to be replaced.
3.1 Rough calibration
The loss of zero of MS6MT Robot is actually the loss of zero of the encoder. If the zero is
lost, perform calibration to recover the zero. The zero of the robot can be roughly recovered
through rough calibration.
If the zero of MS6MT Robot is lost, ensure that the robot remains
in its original position and each axis rotates at an angle of less
than 360°, then perform a rough calibration of the robot zero to
prevent internal cables from damage due to excessive winding.
Confirmation of rotation angle of each axis:
Open the waterproof cover at the rear end of each axis, observe
the winding degree of cables, and turn the mechanical arm to
restore the cables to normal.
Loss of zero:
When the motion trajectories of the robot deviate from the actual planned paths or the
six-axis robot is in a straight state and the calibrated grooves of each axis are aligned
separately, the joint coordinate value is not the value of the origin. The above situation means
that the zero is lost.
Possible causes:
○
1 Low battery voltage of the encoder.
○
2 Failure in the connection between the encoder and the module.
○
3 Failure in the module and encoder assembly.
Summary of Contents for MS6MT
Page 1: ......