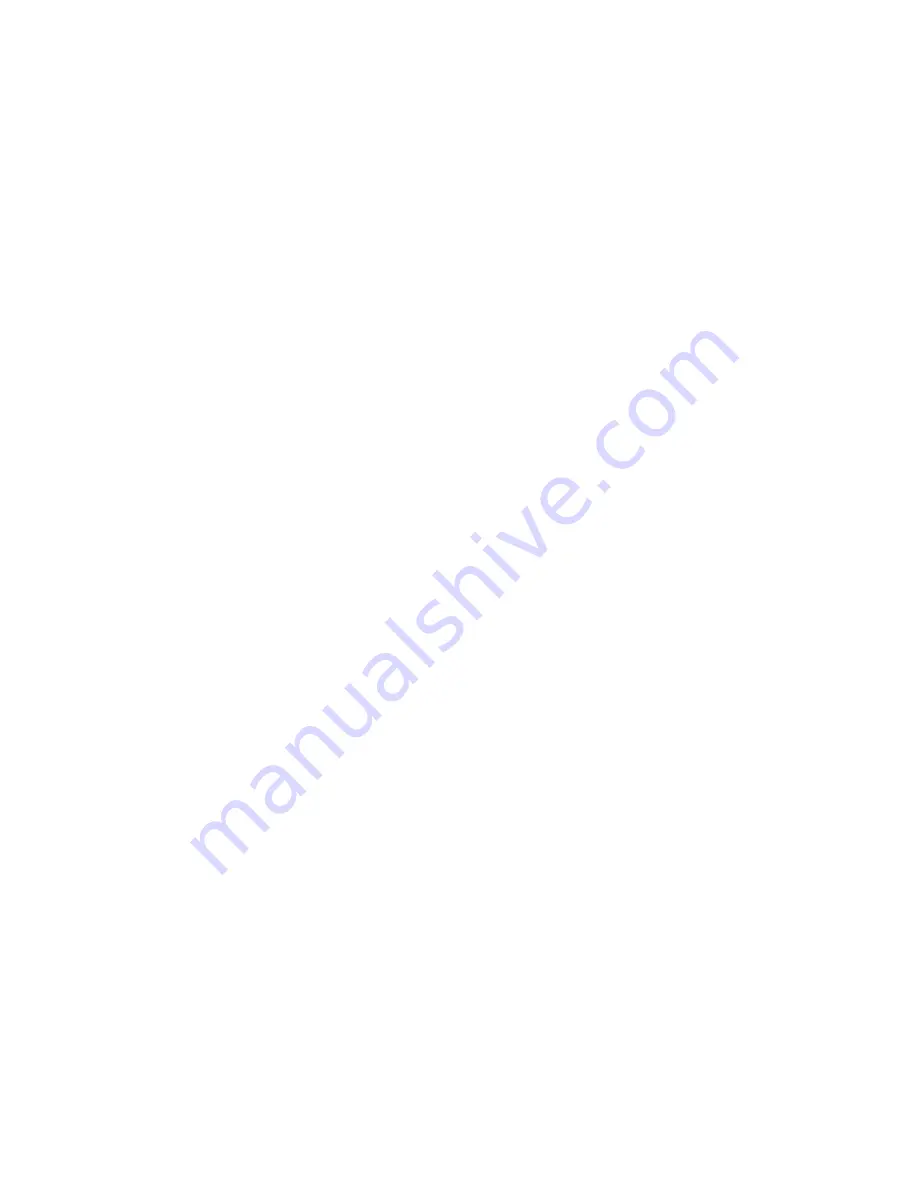
7
1.5 Suggested Maintenance Schedule
between Patients
1. Check entire unit for any visible evidence of damage, such as bent sliders, cracked or broken covers,
frayed or damaged wires, etc. If any signs of damage are found, the unit must be repaired before use.
2. Ensure that all knobs and/or levers are usable and in place.
3. Ensure that all moving components move freely as required.
4. Check all displays and electronic controls for proper operation.
5. Check all mechanical pivot and linkage points for smooth operation and secure mechanical connection.
Make sure all screws, nuts, bolts, rivets, pivot pins, and other fasteners are secure.
6. Gently wipe clean all exposed surfaces with a soft cloth dampened with a mild soap solution or alcohol.
Avoid abrasive cleansers. To disinfect, wipe all exposed surfaces with a 1% to 10% solution of bleach
and water, or other suitable disinfectants.
7. Ensure that all labels are present.
8. Replace patient softgoods.
9. Verify that the device operates to its set limits over several complete cycles.
10. For devices offering absolute Range of Motion (ROM) settings, verify device calibration by observing
the ROM of the device while taking a visual reading using a goniometer at the machine’s pivot points.
Compare the ROM settings of the device with the goniometer readings. ROM readings should be within
+/- 5 degrees of the set parameters. If the readings do not fall within the set parameters, the unit needs to
be checked and recalibrated by a properly trained Service Technician.
Every six Months
1. Repeat steps 1 through 10 of “BETWEEN PATIENTS” procedures.
2. Verify ground continuity where applicable from the device frame to ground pin of the power supply, if so
equipped, using a Safety Analyzer or appropriate device.
Every Eighteen Months
A full inspection of the device by a properly trained Service Technician is recommended every 18 months. The
following points should be covered:
1. Steps 1 and 2 of “EVERY SIX MONTHS” above.
2. Fully inspect all internal and external mechanical and drive components, and repair or replace as
necessary.
3. Fully inspect all internal and external electrical components (including wires, connectors and solder joints),
and repair or replace as necessary.
4. Perform a complete recalibration and subsequent check of electronic and mechanical safety systems
including Reverse-On-Load and Range of Motion.
5. Complete a final check of the device in accordance with Otto Bock Final Inspection criteria (these are
available in the appropriate Technical Service Manual or on request from Otto Bock).
2 COVERS (480/480E/480E PRO)
2.1 bottom Cover
Removal:
note:
Avoid cutting the heads off the plastic fasteners as these can be reused to reattach the covers.
1. Remove the Handle by removing the two Phillips screws located at each end of the Handle attachment.
2. Remove all 11 plastic fasteners from around the cover and separate the bottom cover from the unit.
Summary of Contents for 480
Page 1: ...480 480E 480E PRO CPM Service and Technical Manual 2011 QAL Medical 05070812 3 Rev C 08 11...
Page 2: ......
Page 25: ...25 14 Assembly Drawings 14 1 Main Assembly...
Page 26: ...26 14 2 Thigh Assembly...
Page 27: ...27 14 3 Cradle Sub Assembly 480 L480SA011 480E L480SA022...
Page 28: ...28 14 4 Foot Cradle Assembly...
Page 29: ...29 14 5 Ballscrew Assembly...
Page 30: ...30 14 6 480 U Bracket Slider Assembly...
Page 31: ...31 14 7 480E 480E PRO U Bracket Slider Assembly...
Page 32: ...32 14 8 480E or 480E PRO Motor Assembly Faulhaber...
Page 33: ...33 14 9 480E PRO ONLY Motor Assembly Maxon...
Page 34: ...34 14 10 Motion Controller Assembly 480 480E...
Page 36: ...36 14 12 480 Wiring Diagram...
Page 37: ...37 14 13 480E Wiring Diagram...
Page 39: ...39 14 15 480 480E Electrical Schematic...
Page 40: ...40...
Page 41: ...41...