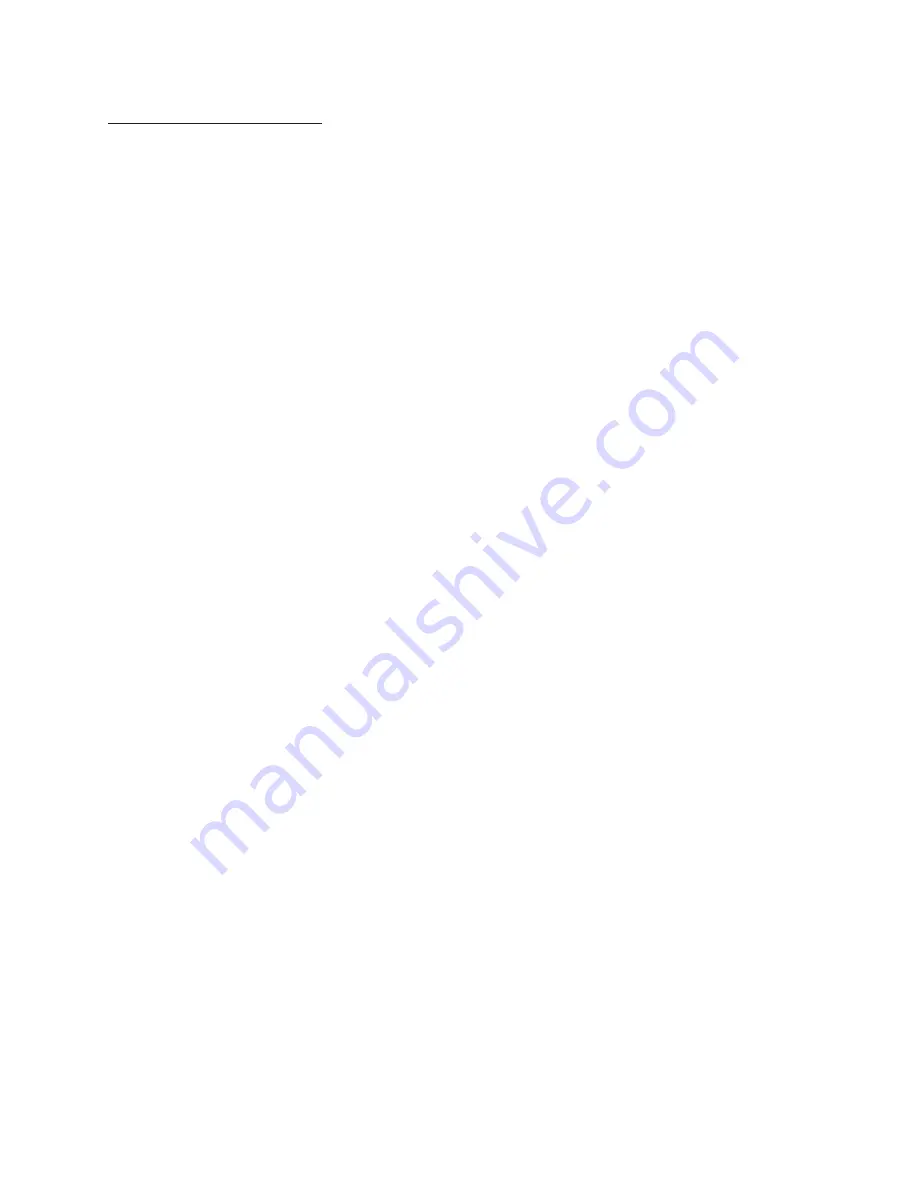
7–13
Chapter 7 – Fuser Subsystem
7.2.3 Fuser Control Modes
Fusing Mode. In Fusing Mode, the Engine Controller keeps the Fuser at the fusing temperature. Fusing
temperature is set in 5
°
C increments from 165
°
C to 185
°
C. Proper fusing temperature depends on the
media in use.
When the Data Controller sends a print command to the Engine Controller, the Engine Controller
activates Fusing Mode. This mode is also used during engine self-test.
Standby Mode. In Standby Mode, the Engine Controller keeps the Fuser at standby temperature,
approximately 165
°
C. Standby Mode keeps the inside of the engine from getting too hot; it also reduces
power consumption.
When the Data Controller sends a print command to the Engine Controller, the Engine Controller switches
the Fuser from Standby Mode to Fusing Mode. If the engine is idle for approximately 180 seconds in the
Fusing Mode, the Engine Controller automatically switches the Fuser to Standby Mode. The Data
Controller can switch the mode from Idle to Standby by using the Standby Mode Request Command.
Idle Mode. In Idle Mode, the Engine Controller lets the Fuser cool to near ambient temperature by turning
off the power to the Fuser.
When the Fuser receives a print command, the Engine Controller switches the Fuser from Idle Mode to
Fusing Mode. The Data Controller can request Idle Mode by issuing an Idle Mode Request Command.
Note that the Engine Controller does not automatically change the Fuser to this mode.
Summary of Contents for L1024
Page 1: ...R...
Page 2: ......
Page 3: ...R P N 704792 001 Rev C...
Page 18: ...1 8 Chapter 1 Introduction...
Page 19: ...2 1 Chapter 2 Clamshell Chapter 2 Clamshell Clamshell and Subassemblies...
Page 46: ...4 4 Chapter 4 Developer Subsystem...
Page 47: ...5 1 Chapter 5 Transfer Subsystem Chapter 5 Transfer Subsystem Transfer Charger...
Page 63: ...5 17 Chapter 5 Transfer Subsystem Detail 5 4 Removing the Lamp Connector...
Page 65: ...6 1 Chapter 6 Paper Feed Subsystem Chapter 6 Paper Feed Subsystem Paper Feed Subsystem...
Page 82: ...6 18 Chapter 6 Paper Feed Subsystem Step 3 Step 2 Detail 6 5 Removing Connectors...
Page 97: ...7 1 Chapter 7 Fuser Subsystem Chapter 7 Fuser Subsystem Fuser Subsystem...
Page 137: ...8 5 Chapter 8 Power Supplies 1 1 2 2 High Voltage Power Supply...
Page 144: ...8 12 Chapter 8 Power Supplies Figure 8 4 Removing the LVPS Cables...
Page 146: ...8 14 Chapter 8 Power Supplies 5 4 2 3 1 Figure 8 5 Removing the LVPS...
Page 147: ...8 15 Chapter 8 Power Supplies Cable Routing Figure 8 6 LVPS Cable Routing...
Page 150: ...8 18 Chapter 8 Power Supplies Figure 8 9 Removing the LVPS Cables...
Page 152: ...8 20 Chapter 8 Power Supplies 5 4 2 3 1 Figure 8 10 Removing the LVPS...
Page 153: ...8 21 Chapter 8 Power Supplies Cable Routing Figure 8 11 LVPS Cable Routing...
Page 199: ...10 1 Chapter 10 Control Panel Chapter 10 Control Panel Keypad LCD Control Panel...
Page 215: ...11 9 Chapter 11 Laser Scanning Unit LSU Subsystem Detail 11 1 Removing the Top Cover...
Page 225: ...12 5 Chapter 12 Covers Frame and Backplane Board 14 1 15 1 21 1 Hinge Covers...
Page 250: ...12 30 Chapter 12 Covers Frame and Backplane Board Figure 12 12 Removing Cables...
Page 252: ...12 32 Chapter 12 Covers Frame and Backplane Board 5 4 2 3 1 Figure 12 13 Removing the LVPS...
Page 269: ...12 49 Chapter 12 Covers Frame and Backplane Board Figure 12 27 Removing Cables...
Page 319: ...Appendix B Wire Data B 1 Appendix B Wire Data...
Page 322: ...Appendix B Wire Data B 4...
Page 327: ...C 5 Appendix C Continuous Form Stacker 15 2 10 1 Figure C 2...
Page 331: ...C 9 Appendix C Continuous Form Stacker 35 2 40 1 55 1 50 1 45 1 Figure C 4...
Page 333: ...C 11 Appendix C Continuous Form Stacker 60 2 Figure C 5...
Page 337: ...C 15 Appendix C Continuous Form Stacker 100 1 105 2 115 1 110 1 ROTATED 180 Figure C 7...
Page 349: ...C 27 Appendix C Continuous Form Stacker 1 2 Figure C 16 Removing the Vertical Frame Braces...
Page 371: ......
Page 372: ...704792 001C...