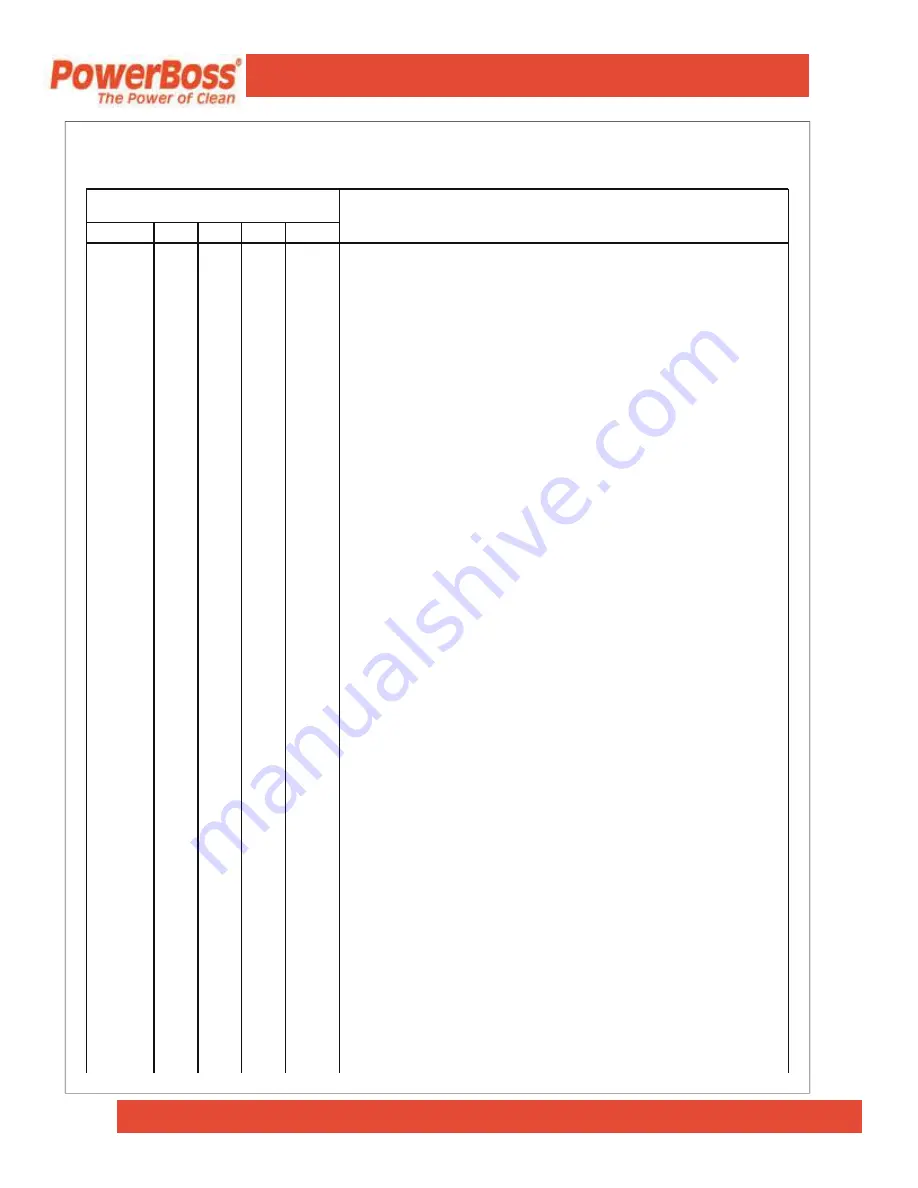
PowerBoss, Inc.
Copyright 2008
Armadillo
®
SW/10XV
PB # 4100034 / Rev. 01A08
Page 26
Operation, Maintenance and Troubleshooting
P L A N N E D M A I N T E N A N C E C H A R T ( C o n t i n u e d )
FREQUENCY (IN HOURS)
SERVICE
DAILY 50 100 200 500
(BY MAINTENANCE AREA)
HOPPER
X
Check hopper filters and clean or replace as
needed.
X
Check hopper clearance from floor and adjust as
needed.
X
Inspect the hopper flaps for wear or damage and
replace
as
needed.
X
Inspect hopper side and frame seals for wear or
damage. Adjust or replace as needed.
X
Lubricate the pillow blocks supporting the dump
mechanism.
STEERING
X
Lubricate steering cylinder rod ends.
X
Lubricate steering fork assembly.
X
Check for leaks.
PARKING BRAKE
X
Check for proper functioning and adjust as
needed.