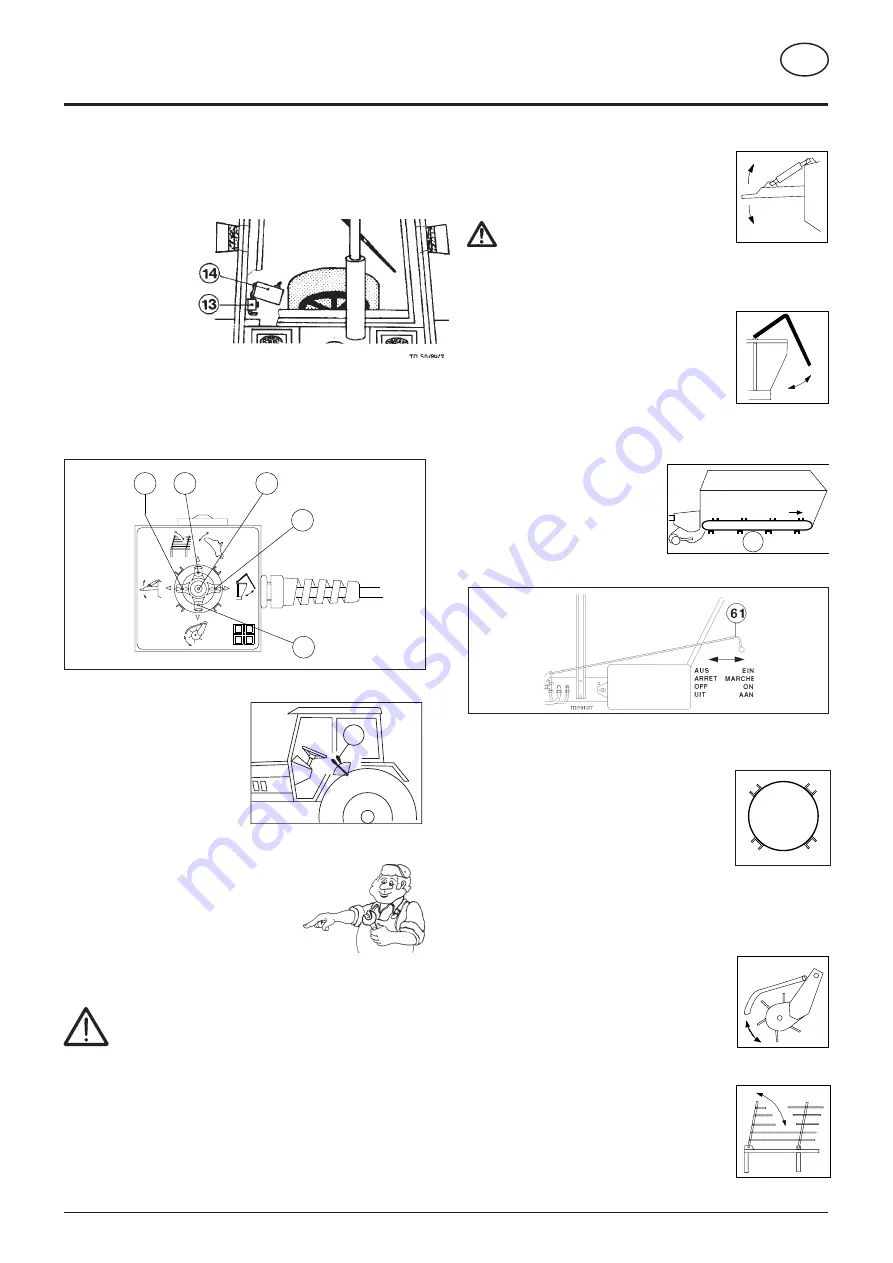
0200-GB ELEK-HYD_537
- 18 -
GB
ELECTROHYDRAULIC OPERATION
Installation and check of the
electrohydraulic operation
- Mount supplied
bracket (13) for the
e l e c t r o h y d r a u l i c
operating with two
hexagon screws
within driver’s vision
and reach in tractor
cabin.
- Insert front control
panel (14) in bracket (13).
Operation
- Preselect desired function on control panel. Switch engages.
- Preselected function is
engaged using servo-
control (ST) on tractor.
Note:
- If tractor is to be parked with implement
attached, electro-hydraulic operation
lever is to be shifted into neutral
position "C".
This prevents battery discharge.
Safety tips
Please take particular care when the operating
elements on the trailer and the tractor are to be used
simultaneously by more than one person. A
conscientious arrangement should be made by those
concerned before operation.
An example:
Danger of injury arises if a person stands at the rear of the
trailer and somebody in the tractor cabin activates a switching
function (opening the tailgate, switch on the driving gear, ...).
Pivoting drawbar
1. Lever on control panel in position "A".
2. Engage servo-control (ST) on tractor.
Attention!
Do not engage pivoting drawbar when
implement is standing on supporting wheel.
Tailgate
1. Lever on control panel in position "D".
2. Engage servo-control (ST) on tractor.
Automatic unlocking, raising/lowering and
shutting of tailgate.
Scraper floor reverse run (KR)
Front operation
1. Shift lever (61) to the "ON" position.
2. Lever on control panel in neutral position "C".
3. Engage servo-control (ST) on tractor.
Rear operation
1. First shift the lever (61) into the "OFF"
position.
2. Lever on control panel in neutral position
"C".
3. Engage servo-control (ST) on tractor.
4. Switch scraper floor drive "on" or "off" with lever (61).
Pick-up
1. Lever in position "E".
2. Engage servo-control (ST) on tractor.
Raising or lowering pick-up.
I n doing so loading unit operation and pick-
up are automatically switched on or off.
Dry forage extension
1. Lever on control panel in position "B".
2. Engage servo-control (ST) on tractor.
Folding extension up or back gradually.
TD 18/93/9
A
B
C
D
E
KB - KR
KR
ST