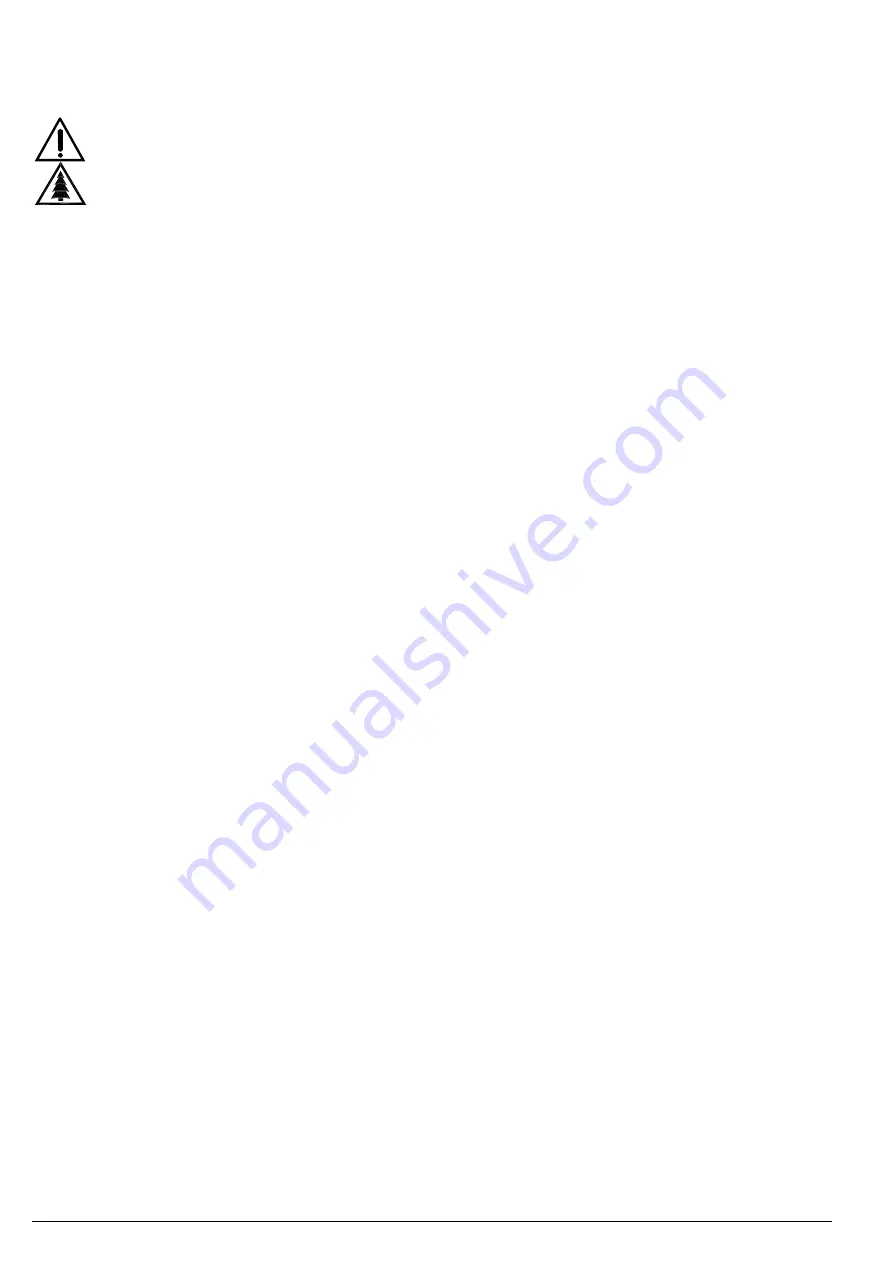
Operating manual liquid ring vacuum pumps and compressors series TRH - TRS - TRM - TRV - SA & Systems type HYDROSYS - OILSYS
34
evaluation by our technical department. Mechanical seals do not require maintenance until losses of liquid are visible
(for seal replacement see “Disassembly and Assembly Instructions”). Losses of few drops of liquid in several minutes is
normally considered acceptable and it is not an indication of seal failure.
Seal leakage or even seal failure should be properly corrected considering the impact on environment, toxicity and
safety issues.
CAUTION!
Pay attention to possible leakage of pumped liquid from mechanical seal which, by its characteristics, could be
harmful to the environment.
Mechanical seals should NEVER run dry, without flushing liquid (internal or external). This could cause severe damage
to the seal faces, O-Rings and elastomer.
Mechanical seals are wear parts: the actual mechanical seal life depends on the severity of the duty load.
It is recommended to check the wear of seal faces every 4000 working hours. This is an acceptable normal life span for
mechanical seals. Exceeding this life span can lead to losses due to wear and tear and will require seal replacement.
In case a mechanical seal is replaced, the condition of shaft sleeve (if present) must be checked: if the sleeve surface is
damaged, or in case of doubt, it is recommended to replace also the shaft sleeve together with the mechanical seals.
MECHANICAL SEALS WITH QUENCH
There are two types of Quench/Barrier, available upon request: API Plan 61 and 62.
System Plan 61 (see fig. 35) includes a bushing on the back of the seal at atmospheric pressure side (single or double)
to hold the bulk of the liquid in the event of accidental failures. The bushing requires a minimum clearance over the
shaft therefore the liquid is NOT sealed completely but most of it will be retained in case of a sudden seal breakage.
Drain and vent connections are threaded. This arrangement does not allow a continuous flushing because the above
mentioned clearances would cause considerable losses of liquid over the shaft toward the outside. This system is
chosen for avoid emergencies or to limit losses of liquid.
System Plan 62 (see fig. 36) requires (contrary to Plan 61) a constant flushing because the auxiliary seal is of the
contact type and CANNOT work without a liquid that removes the generated heat of friction. The auxiliary seal is usually
a lip seal (radial seal ring) not to be confused with the traditional mechanical seal. Losses of several liquid drops should
be tolerated and with time its reliability will decrease. This system is often used where there is the need to wash the
back of the mechanical seal on the atmospheric side preventing crystallization or coking of handled product. It is a less
effective alternative to the double mechanical seals in series. Pressure of buffer liquid must follow same rules as for the
double seals in series, therefore max pressure can be 0.3 bar over the atmospheric pressure and temperature can be
max 60°C.