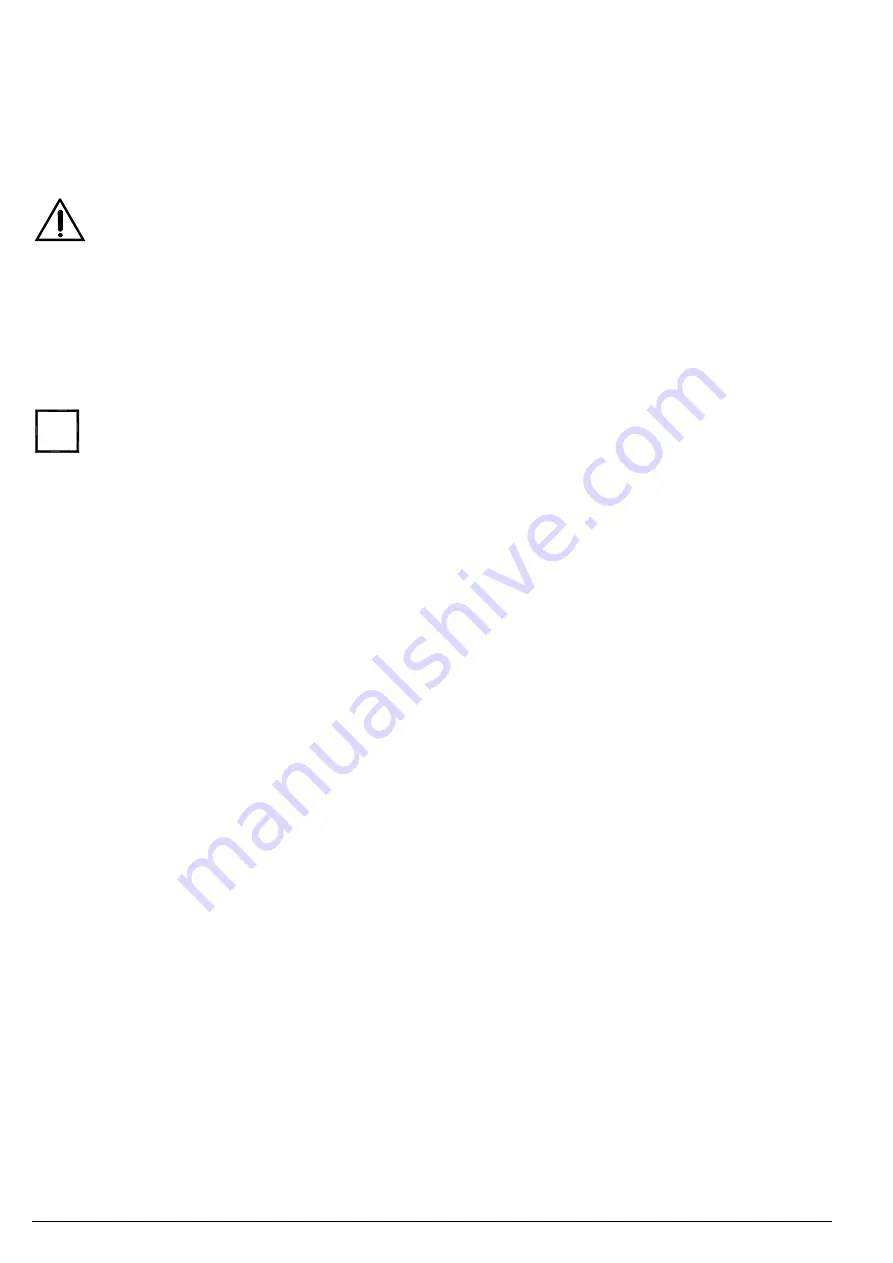
Operating manual liquid ring vacuum pumps and compressors series TRH - TRS - TRM - TRV - SA & Systems type HYDROSYS - OILSYS
10
Concrete pads and other concrete works must be aged, dry and clean before the pump assembly can be positioned in
place. Complete all the work relating to the foundations and grouting of the pump assembly, before proceeding with the
mechanical and electrical portion of the installation.
7.1 - PIPING CONNECTIONS
Identify first locations and dimensions of all connections required to interconnect the pump with the installation, then
proceed with the actual piping: connect the pump suction and discharge flanges, the service liquid line and all other
service connections (see fig. 6 to 15).
CAUTION!
Possible contact with hazardous media and hazardous substances, cold or warm.
Be sure to pipe the correct connection from the installation to the respective pump connection ! operate only
provided with apposite protective devices.
To prevent any limb or foreign matters from entering the pump during installation, do not remove protection cap from
flanges or cover from openings until the piping is ready for hook-up.
Verify that all foreign objects such as welding bits, bolts, nuts, rags and dirt are removed from piping, separators, etc.
before these are connected to the pump.
Flanges should be connected parallel with each other, without stress and with bolt holes lined up. The weight of the
pipe must not weigh on the pump.
The flange gaskets should not interfere with the inside diameter of piping and/or flange.
All piping must be independently supported, easily located and must not transmit forces or torque to the pump
due to the weight or to thermal expansions.
Piping size must never be less than the respective connection on the pump.
Suction and discharge flanges are vertical and identified with arrows.
To minimise friction losses and back-pressures, the discharge piping should be one size larger than the pump
connection size. To avoid back-pressure and possibility of flooding the pump when it stops, it is recommended to limit
the rise of the discharge
piping to approximately 50 cm above the pump discharge flange.
Upon completion piping and connections should be tested for leakage under vacuum.
7.2 - ACCESSORIES
Listed below are common accessories that may be supplied with the pump or added at a later date. See fig. 6 to 15 for
locations and connection sizes on the pumps.
Non return valve, (check valve)
Prevent back-flow of gas and liquid in the suction piping and/or discharge piping when the pump stops.
Is installed on the pump suction flange in the case of vacuum service or on the pump discharge flange in the case of
compressor service.
Vacuum relief valve
It is used to protect the pump from cavitation or to regulate the suction minimum pressure (or max vacuum).
When the pump capacity exceeds the system load at a given vacuum, the relief valve opens letting in atmospheric air or
gas (if connected to the discharge separator) keeping constant the pre-set
vacuum.
Automatic draining valve
It is used to drain the pump to the shaft centreline when the pump stops so to prevent that the pump has excessive
liquid for the next start-up. Starting the pump full or with too much liquid could severely damage the pump.
Vacuum gauge
Usually installed under the pump suction flange, will provide an indication of the pump operating vacuum (pressure).
Discharge reservoir separator
It separates the service liquid from the gases at the pump discharge.
It can be mounted on the pump discharge flange (type HSF) or on the pump baseplate (type HSP).
It is required when the system is with partial or total recovery of the service liquid.
Heat exchanger
It cools the service liquid for those systems with total liquid recovery: it can be plate and frame type, shell and tube type
or radiator type, depending upon the application.
Filter
Required to stop solids from entering the pump suction. Sizing of the filter is very important as it could create excessive
pressure drops which would affect the pump performance.
i