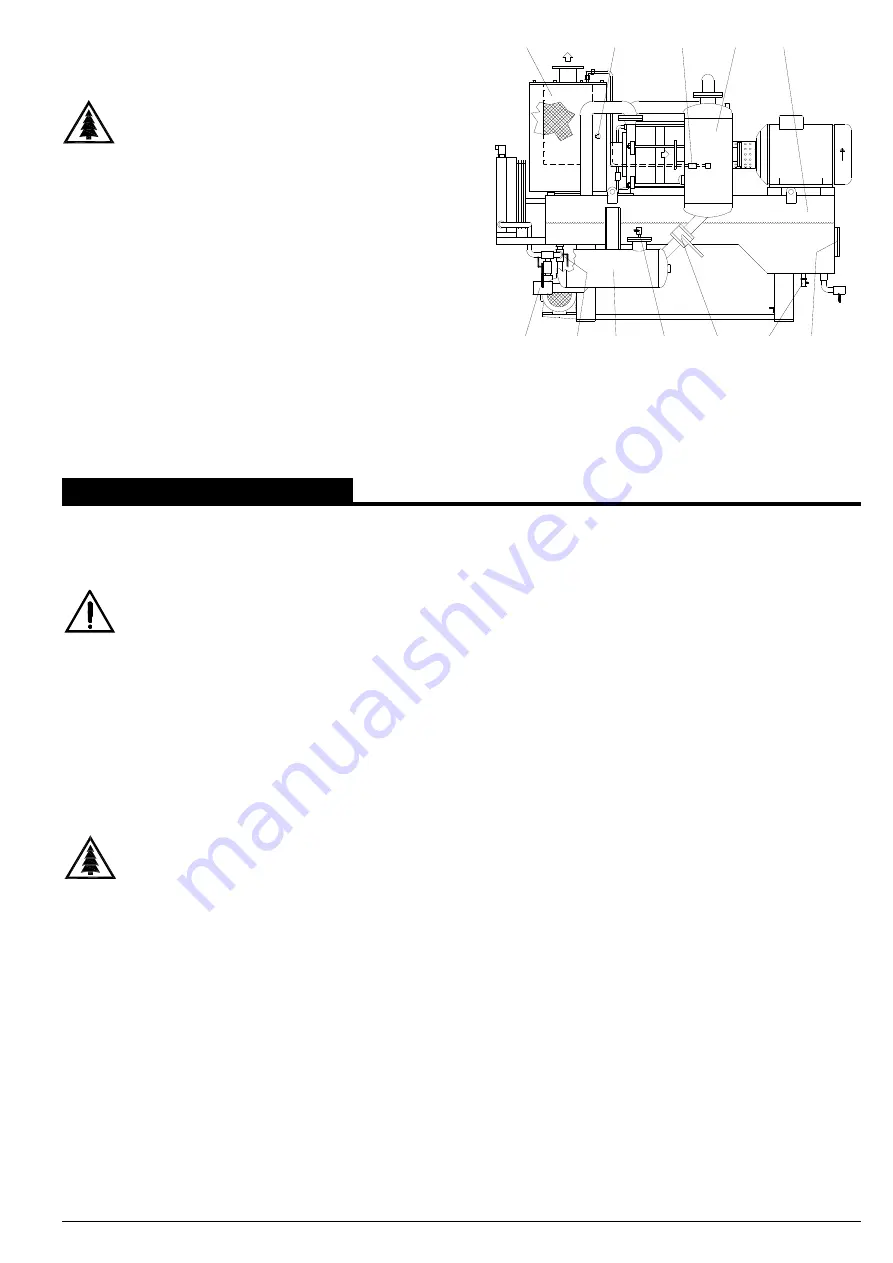
Operating manual liquid ring vacuum pumps and compressors series TRH - TRS - TRM - TRV - SA & Systems type HYDROSYS - OILSYS
31
To replace the oil demister filter, simply disconnect the oil
scavenger line, remove the cover ITEM 1C, remove the used
filter element.
Dispose the waste grease according to the current
regulations protecting the environment.
Apply a liquid gasketing material over the 2 gasket faces of
the new filter and place the latter in the housing, put in place
the cover and the scavenger line.
For systems with separator cyclone ITEM 1D and recovery
tank ITEM 1E it is required to periodically remove the
accumulated materials.
For this operation close the valve ITEM 13E between the
cyclone and the reservoir, open the vent valve ITEM 12
situated at the upper part of the separator, open the reservoir
drain valve ITEM 11A to discharge the collected materials.
After the cleaning operation, return to the original position by
reverting the above steps.
It is possible to by-pass the service liquid circulating pump by
closing the suction and discharge valves and opening the
valve ITEM 13C in the by-pass line.
This will connect the frame reservoir directly with the heat exchanger.
13 - BEARINGS MAINTENANCE
DANGER!
Danger due to collision, crushing or harm. Wait for the complete pump stopping before handling the unit. If the
pump still contains some fluid it may suddenly start to rotate once again. Take precautionary measures by
draining the pump or closing the pipes by mean of a valve. Possible contact with high temperature surfaces,
wait for the pump cooling. Maintenance must be absolutely carried out when the pump is at a standstill,
disconnecting the power supply and any other connection. Please make sure that the power supply is restored
only by the operator making the maintenance. It is necessary the presence of at least two operators and a
foreman must be aware there is a maintenance in progress.
Operate only provided with apposite protective devices.
FOLLOW THE SAFETY STANDARDS LISTED IN CHAPTER 2.
During assembly the bearings are already lubricated with high quality grease with working temperature limits -30°C
+140°C (for pumps type TRHA 150 and TRSA 200 the working temperature limits are -20°C +180°C).
The bearings must be lubricated every 2000/2500 hours, or at least once in a year, injecting a moderate quantity of
good quality lubricating grease (about 1/5th of the quantity shown in table 8). Any leakage of old grease must be
removed. We recommend replacing the bearings every 15000 hours or when replacing the mechanical seals (for
replacement see the "Disassembly and assembly instructions").
Dispose the waste grease according to the current regulations protecting the environment.
The sealed pre-greased never need lubrication, but must anyway controlled after 2000/2500 working hours.
Bearing temperature should not exceed the 85°C during normal working conditions and normal environments.
Bearings can overheat for reasons such as too much grease, misalignment of flexible coupling, wrong bearings,
excessive vibrations, bearing wear. See tab. 8 for bearing numbers and type used for each pump.
Fig. 29
(General schematic drawing)
1B
1E
11A
13C
12
13E
13F
14
1C
13G
1D
43