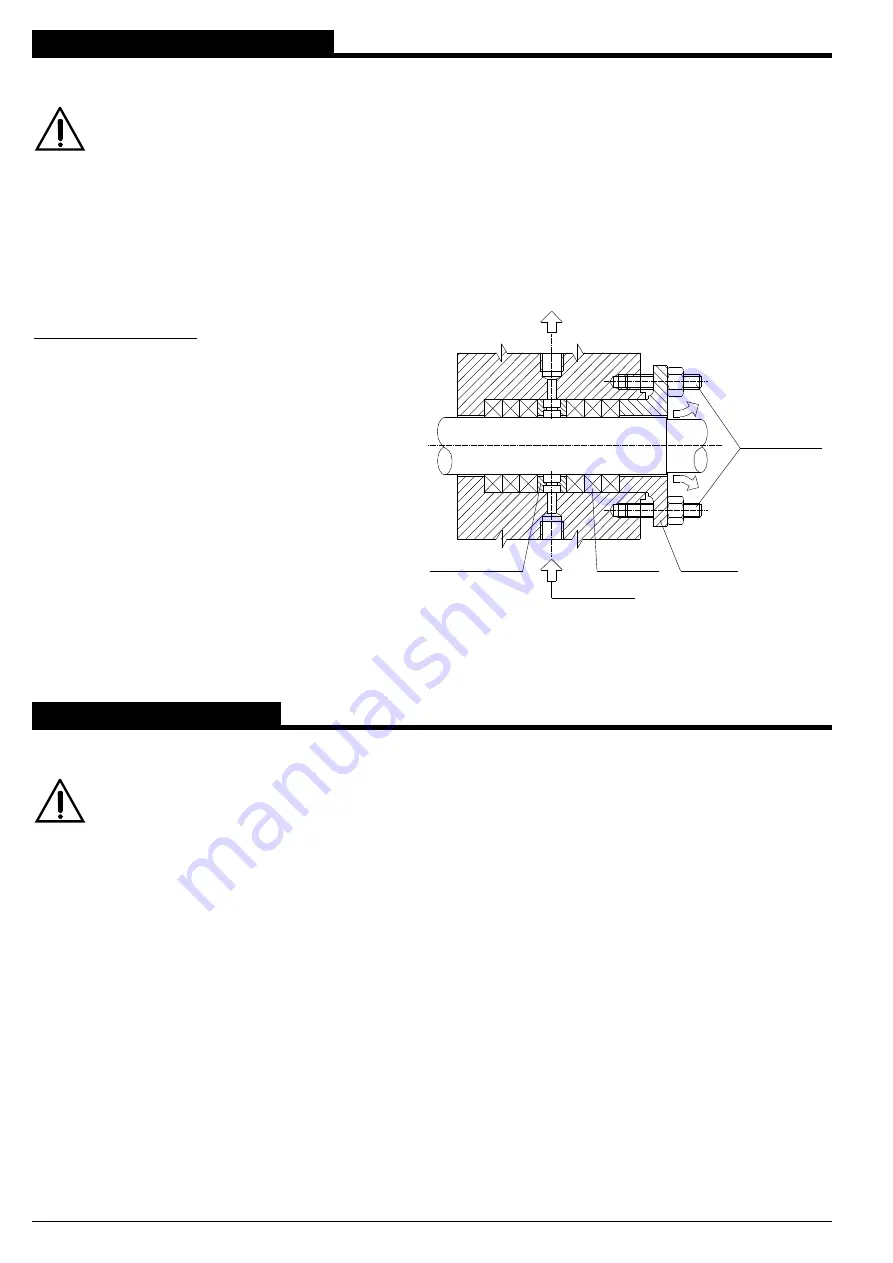
Operating manual liquid ring vacuum pumps and compressors series TRH - TRS - TRM - TRV - SA & Systems type HYDROSYS - OILSYS
32
14 - PACKED STUFFING BOXES
DANGER!
Danger due to collision, crushing or abrasions. Possible contact with hazardous fluids, cold or warm. Wait for
the complete pump stopping before handling the unit. If the pump still contains some fluid it may suddenly
start to rotate once again. Take precautionary measures by draining the pump or closing the pipes by mean of
a valve. Remove protections only in case of maintenance. Operate only provided with apposite protective
devices.
Pumps fitted with packed stuffing boxes require packing flushing either from an external source or directly from the
pumped media through pump internal passages.
This liquid is necessary to remove the friction heat generated between the shaft and the packing.
The dripping quantity is a function of the pump size and of the pressure in the stuffing box housing.
In any event the liquid drops coming out of the stuffing box should not exceed a temperature of 60 - 70°C in relation to
handling a liquid at ambient temperature.
All adjustment operations must be performed with the
PUMP NOT RUNNING following the safety measures
given in chapter 2. After completion of the work ALWAYS
re-install the safety guards previously removed.
At first start up loosen the nuts of the packing gland
allowing a steady flow of liquid to drain out (see fig. 30).
After obtaining a steady flow of leakage gradually tighten
the gland nuts until attaining a steady dripping within the
limit of the above recommended temperature.
A few hours time span may be required to establish a
steady dripping at low temperatures.
Packing adjustment is required when the liquid leakage
increases.
When adjustment is no longer possible, the packing
material should be replaced with new one.
Follow the “Disassembly and Assembly Instructions” to
replace the packing materials.
In the event the pump remains out of service for more
than 2 months it is recommended to replace the packing
rings, prior to start-up.
15 – MECHANICAL SEALS
DANGER!
Danger due to collision, crushing or abrasions. Possible contact with hazardous fluids, cold or warm. Wait for
the complete pump stopping before handling the unit. If the pump still contains some fluid it may suddenly
start to rotate once again. Take precautionary measures by draining the pump or closing the pipes by mean of
a valve. Remove protections only in case of maintenance. Operate only provided with apposite protective
devices.
Purpose of mechanical seals is to retain handled product inside the pump in the area where the shaft exits the pump
casing. Mechanical Seals can be of many different materials, types and configurations (see fig. 32-33-34 for some
examples).
To assure maximum reliability and safe operation Pompetravaini evaluates seal choices at time of pump selection in
connection with customer’s requirements, application and liquid details.
In the case of self lubricated single mechanical seals (API Plan 01, 02 or 11, see fig. 32) flushing and /or pressure
system are not required, pump has been engineered to provide proper seal lubrication with pump operating pressure.
In the event the application requires increased safety margin against possibilities of product leaking through a single
type mechanical seal, it is possible to install two mechanical seals working simultaneously thus creating a safety barrier
from the pumped liquid.
There are two possible types of double mechanical seals: Back-to-Back (also kno
wn as “Opposite” type) API Plan 54,
see fig. 33 and in Series (also known as “Tandem” type) API Plan 52, see fig. 34.
Double mechanical seals Back-to-Back are generally selected where pumped liquid is absolutely not allowed to leak
from the pump. Double mechanical seals in Series are chosen where the pumped liquid may escape the pump toward
the pump exterior but it is controlled and contained in the closed seal loop but never to escape to the atmosphere.
Double mechanical seal installations require a flushing (buffer) liquid from an external source that is compatible with the
pumped product as well as the working conditions. Flushing liquid system is such as to guarantee adequate buffer liquid
pressure and temperature to the mechanical seals: seal flushing system with proper instrumentation and controls is of
LANTERN
RING
PACKING
RINGS
PACKED BOX FLUSHING
GLAND PACKING
ADJUSTING
BOLTS & NUTS
Fig. 30