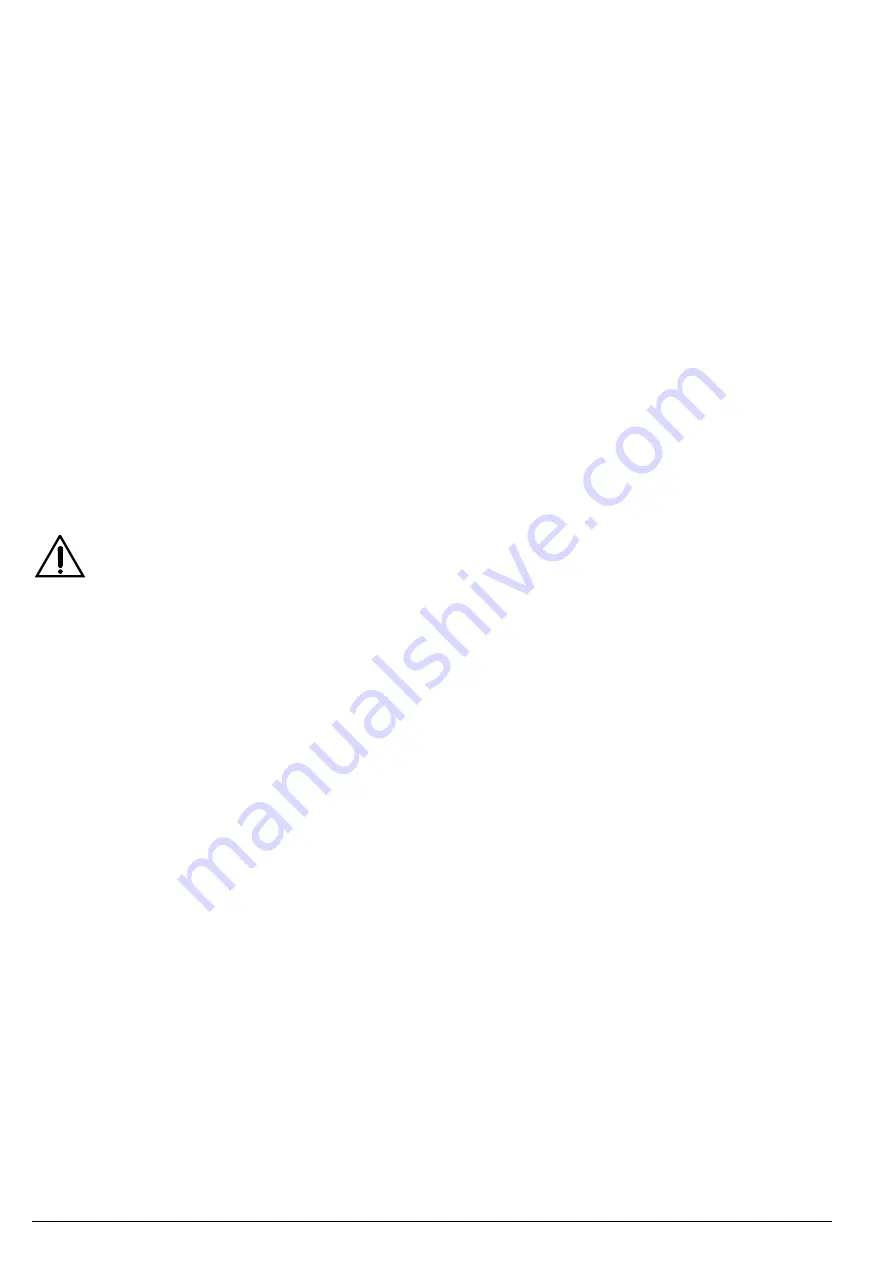
Operating manual liquid ring vacuum pumps and compressors series TRH - TRS - TRM - TRV - SA & Systems type HYDROSYS - OILSYS
12
7.4 - INSTALLATION SCHEMATICS FOR LIQUID RING COMPRESSORS
The liquid ring vacuum pump can also operate as a compressor up to a maximum differential pressure, depending upon
the models, of about 2 bar. The compressors series SA are specifically engineered to perform with differential
pressures of up to 10 bar, depending on models.
The principle of operation is same as given in previous paragraph (7.3 for vacuum pumps) and there are three possible
type of installations: once-through service liquid, partial recovery service liquid and total recovery service liquid.
The service liquid entering the compressor connection should have a pressure of minimum 0,4 bar
g
above the
compressor operating inlet
pressure. A booster pump will be required if the service liquid is available at lower
pressures.
Separator/reservoir is considered a pressure vessel and as such it must be engineered and built to the applicable codes
(ISPESL, ASME, PED, etc.). Accessories such as pressure relief valve, check valve(non-return valve), automatic float
type drain valve(water trap), etc. are required in a compressor system.
Fig. 9, 10 and 11 illustrate the three possible types of installations.
7.5 -
INSTALLATION OF “HYDROSYS” SYSTEMS
HYDROSYS systems are factory assembled and piped including discharge separator/reservoir, heat exchanger
(air/liquid or air/air), circulating pump, and all required accessories mounted on a common compact baseplate/frame.
See chapter 20 for additional details.
Installation of HYDROSYS system is similar to that of a vacuum pump or a compressor with partial recovery or total
recovery of service liquid depending upon the application (see chapter 7.3 or 7.4).
It is important to properly engineer the connecting piping to the system suction and discharge, cooling lines, flushing
lines, and draining lines.
The used heat exchanger is designed
with
service liquid being cooled approximately 4 to 6°C over the available cooling
media temperature. The cooling liquid flow is approximately same as the service liquid flow needed by the pump at the
operating conditions (see chapter 7.7 or 7.8).
Schematics for once-through, partial and total service liquid recovery are shown in fig. 7 - 8 - 10 - 11.
7.6 -
INSTALLATION OF “OILSYS” SYSTEMS
CAUTION!
Possible contact with hazardous media, cold or warm, and pump surfaces, cold or warm. During the
functioning the pump, the separator tank and pipes connections may reach temperatures higher than 60°C. In
case, adopt the necessary precautions and protection to satisfy the safety regulations in force. Operate only
provided with apposite protective devices.
OILSYS are factory packaged systems including liquid ring vacuum pump using oil for service liquid. For additional
details see chapter 21. The system is complete with oil circulating pump, heat exchanger, oil demister, cyclone for
removal of dust (optional) and other accessories upon request.
Installation is simple and does not require additional details other than those already discussed in the previous chapter.
Suction and discharge piping should be connected to the respective pump flanges. When locating the discharge piping
it should be noted that although the system is fitted with oil demister, there may still be traces of oil fumes carried by the
vented gas. Make sure therefore, that the selected area for vacuum pump discharge is suitable for such purpose.
All other connections, (heat exchanger, draining, etc.) must be properly done. See fig. 48 for location of connections.