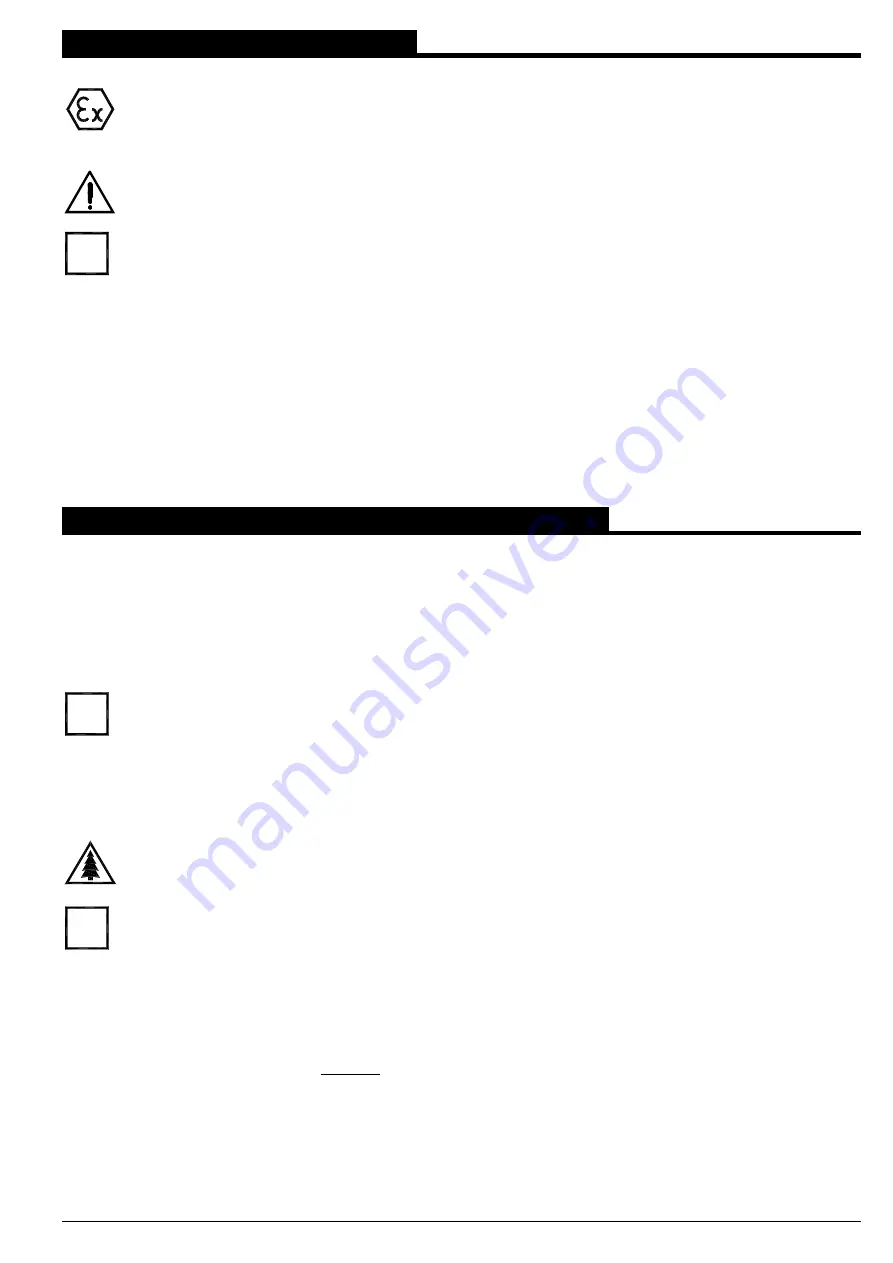
Operating manual liquid ring vacuum pumps and compressors series TRH - TRS - TRM - TRV - SA & Systems type HYDROSYS - OILSYS
27
10 - CHECK LIST PRIOR TO START-UP
If the installed pump is designated to be used in environments subjected to the application of the ATEX
99/92/CE directive but does not show the wording “ATEX” on the name plate, and the integrative ATEX
manual hasn't been received or undelivered, it strictly forbidden proceed to start up the pumps but necessary
to consult POMPETRAVAINI for clarifications.
CAUTION!
All questions listed below must have POSITIVE answers prior to proceeding to the pump start-up (the following
list may not be complete for special installations which may require further precautions as the cases dictate)..
- Is this manual entirely read and understood?
- Are all the safety protections in order?
- Are the electrical connections properly wired, grounded and protected?
- Is the position of the pump switch-off button evident, accessible and clear?
- The piping system has been flushed of any foreign particles, welding impurities, etc.?
- Have all piping and pump obstruction been removed?
- All connections and piping are leak proof and there are no external forces or moments applied to the piping or pump
flanges?
- Pump and motor are properly lubricated, if required?
- Pump/motor alignment has been checked?
- If mechanical seal requires flushing has this been connected?
- All valves in the installation are in the correct position?
-
Has this pump’s direction of rotation been checked by jogging the motor?
- Are pump and installation ready for start-up?
11 - STARTING, OPERATING AND STOPPING PROCEDURES
Upon receipt and/or completion of installation, before turning on the power to the electric motor, rotate the pump shaft
by hand to make sure that the pump rotor is free. In the event the shaft does not turn, try to free it up by applying a
torque to the pump coupling with a pipe wrench. To free the rotor of a monoblock style pump (without coupling)
introduce a bolt (or similar tool) at the motor shaft end that has a threaded connection and apply the torque by hand.
In the event the pump does not become free with the above procedures, fill up the pump with a suitable solvent or
lubricating liquid, let it rest for several hours to allow softening of the rust build-up inside the pump, drain the pump and
apply torque to the pump shaft as described above to finally free the rotor.
The selected solvent or lubricating fluid must be compatible with the pump, seals and gasketing materials.
New pumps from the factory and pumps coming from long term storage are likely impregnated with a rust preventative
liquid; before the start-up, these pumps should be subjected to fresh water rinsing for approximately 15 minutes.
The obtained liquid-water mixture must be collected and, according to the environmental disposal regulations, treated
as special liquid.
Dispose the waste liquids according to the current regulations protecting the environment.
CHECK PUMP-MOTOR COUPLING ALIGNMENT!
This must be done prior to the first start-up and before every start-up if pump or motor has been removed from
the installation for maintenance or other reasons. See chapter 8.2.
Prior to starting the pump verify that all auxiliary components are available, ready for use and, where required, they are
in the open position (i.e.: double mechanical seals are pressurised with buffer liquid, cooling liquid to heat exchanger is
open, etc.) and the pump bearings are lubricated.
If the gas and/or service liquid temperatures are in the dangerous levels, it is recommended to insulate the pump, piping
and separator to avoid direct contact with their surface, avoid freezing, thermal shock or loosing heat energy.
NOTE:
See chapters 11.4 to 11.6 for OILSYS systems start-up, operation and shut-down.
11.1 - START-UP
(In the following, reference is made to certain ITEM numbers which appear on fig. 6 to 11 of chapters 7 and 20).
Open valve at gas discharge if installed and partially open the valve at the suction side.
When operating the pump as compressor there must be a check valve ITEM 2 fitted at the discharge side.
When pump ITEM 4 is fitted in a partial recovery or total recovery or HYDROSYS systems, as built by
POMPETRAVAINI, it is required to have drain valve ITEM 11 at separator ITEM 1 in the closed position, flow regulating
valve ITEM 13 and overflow valve ITEM 24 in the open positions. Separator overflow valve ITEM 24 should be piped to
i
i
i