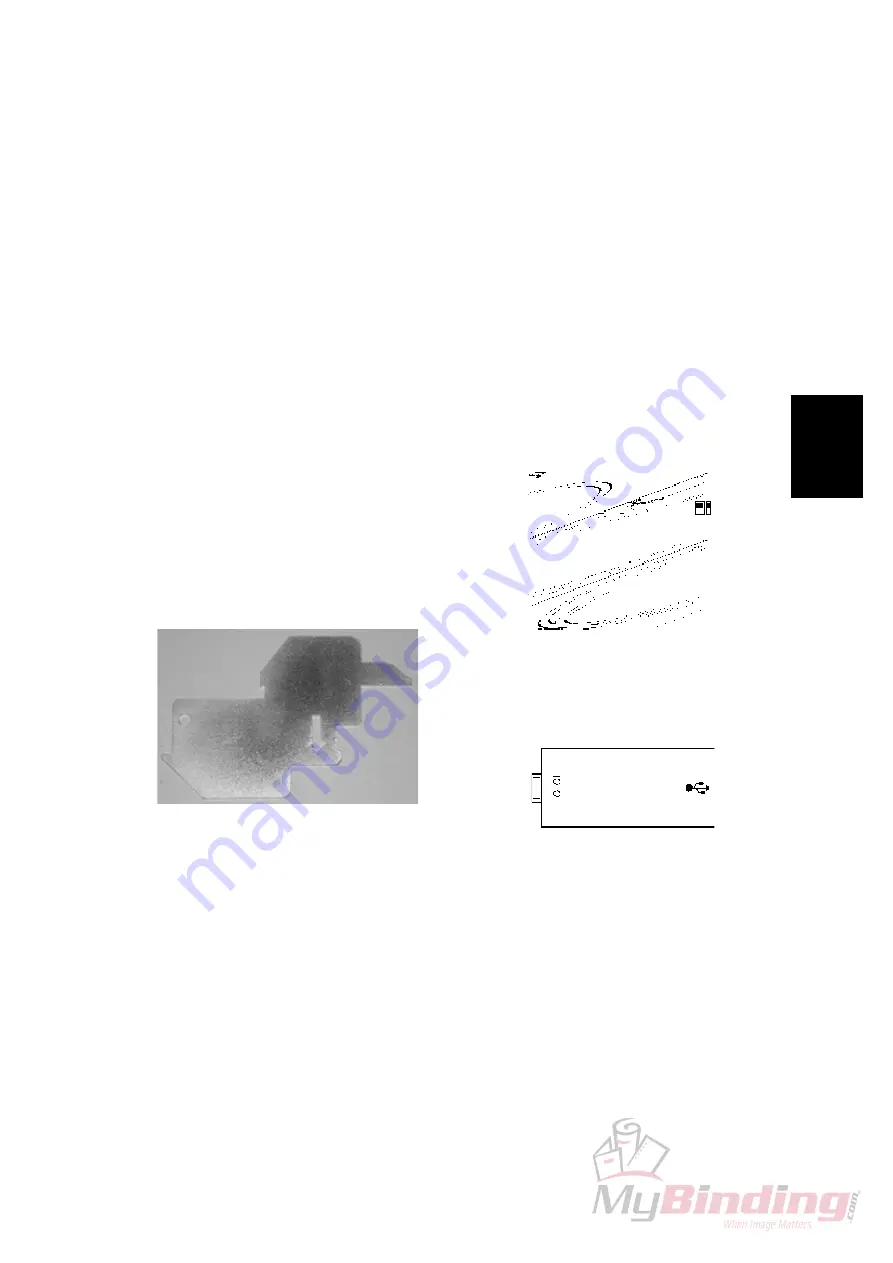
Replacement
Adjustment
20 September 2006, Rev 0.01
3-3
SPECIAL TOOLS AND LUBRICANTS
NOTE:
For the BM 2000 Booklet Making system not to be interlocked
(interlocked=36V interrupted), the Interlock switch must be activated and
the Interlock magnet must be blocked with a metal. Use the Cheater to
override the interlock for running the system with open top covers:
1. Hold the Cheater above the interlock so the arrows meet.
2. Put in the left end in the slot so it hooks under the bracket.
3. Push the Cheater down and to the right so it latches in place.
Interlock cheater
(One pcs included
in each module)
USB converter
(Not included!
Purchase locally)
Software loading cable
(Not included in BK5010.
Part No. SR770010)
In order to facilitate the service of the BM 2000 Booklet Making system there are a
few special tools needed.
Where part number is written it can be purchased from your supplier.
3.2
SPECIAL TOOLS AND LUBRICANTS
3.2.1 SPECIAL TOOLS