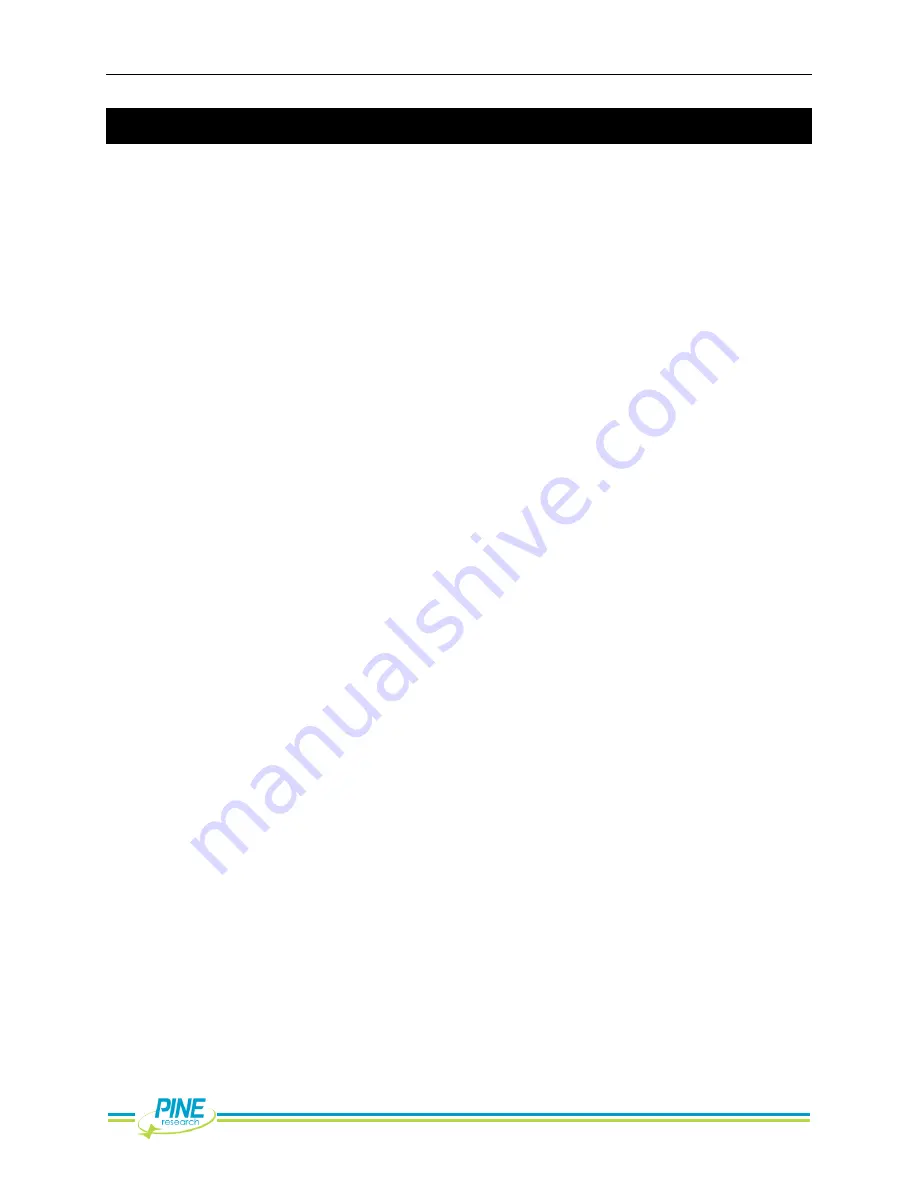
16
2
Description
The MSR rotator provides excellent steady-state control of constant rotation rates,
but it also offers outstanding acceleration/deceleration control for those
applications where the rotation rate must be modulated. The base rotation rate
(for steady-state constant rate control) may be manually adjusted from 50 to
10,000 RPM by turning a ten-turn potentiometer knob located on the front panel
of the control unit. As the knob is turned, a built-in tachometer measures the
actual rotation rate, and this rate is continuously displayed on the front panel of
the control unit. Manually turning the knob and observing the rotation rate is by
far the most common manner in which the rotation rate is selected.
More complex control of the rotation rate is possible when the MSR rotator is
connected to a potentiostat system capable of supplying an analog rotation rate
signal. While specific details vary from one system to another, the basic idea is
that the potentiostat produces an analog signal that is proportional to the target
rotation rate. This analog signal is carried by a cable (supplied by the potentiostat
manufacturer) to a pair of input banana jacks on the front panel of the MSR
rotator’s
control unit. This connection permits the software which controls the
potentiostat to control the rotation rate using a constant voltage level (for steady-
state rotation) or a more complex waveform such as a sine wave (for
hydrodynamically modulated voltammetry).
The rotator is able to accurately follow complex waveforms and create the
desired rotation rate response by using a high rate, low inertia, permanent
magnet DC motor in combination with a high voltage, bi-polar power supply. In
general, the MSR rotator can track and follow low frequency (less than 100 Hz)
external input signals with amplitudes that do not exceed 10% of the baseline
rotation rate. The usual proportionality between the external input signal and the
rotation rate is 1.0 RPM/mV, but a hardware jumper setting inside the control unit
may be used to select the different ratios (see Section 6.7).
The rotation rate is typically monitored by observing the front panel display on the
control unit. In addition, the tachometer measurement can be monitored by
connecting an oscilloscope, voltmeter, or other recording device across the two
output banana jacks on the front panel. The voltage signal from the tachometer
presented at these output jacks is proportional to the rotation rate. The ratio used
for this signal is 1.0 mV/RPM.
The control unit is connected to the motor unit using a 15-conductor cable with
“straight thru” wiring terminated on each end with HD
-15 connectors. The usual
cable length is 183 cm (72 in), but longer distances can be spanned by chaining
together multiple cables.
Summary of Contents for MSR 636A
Page 2: ......