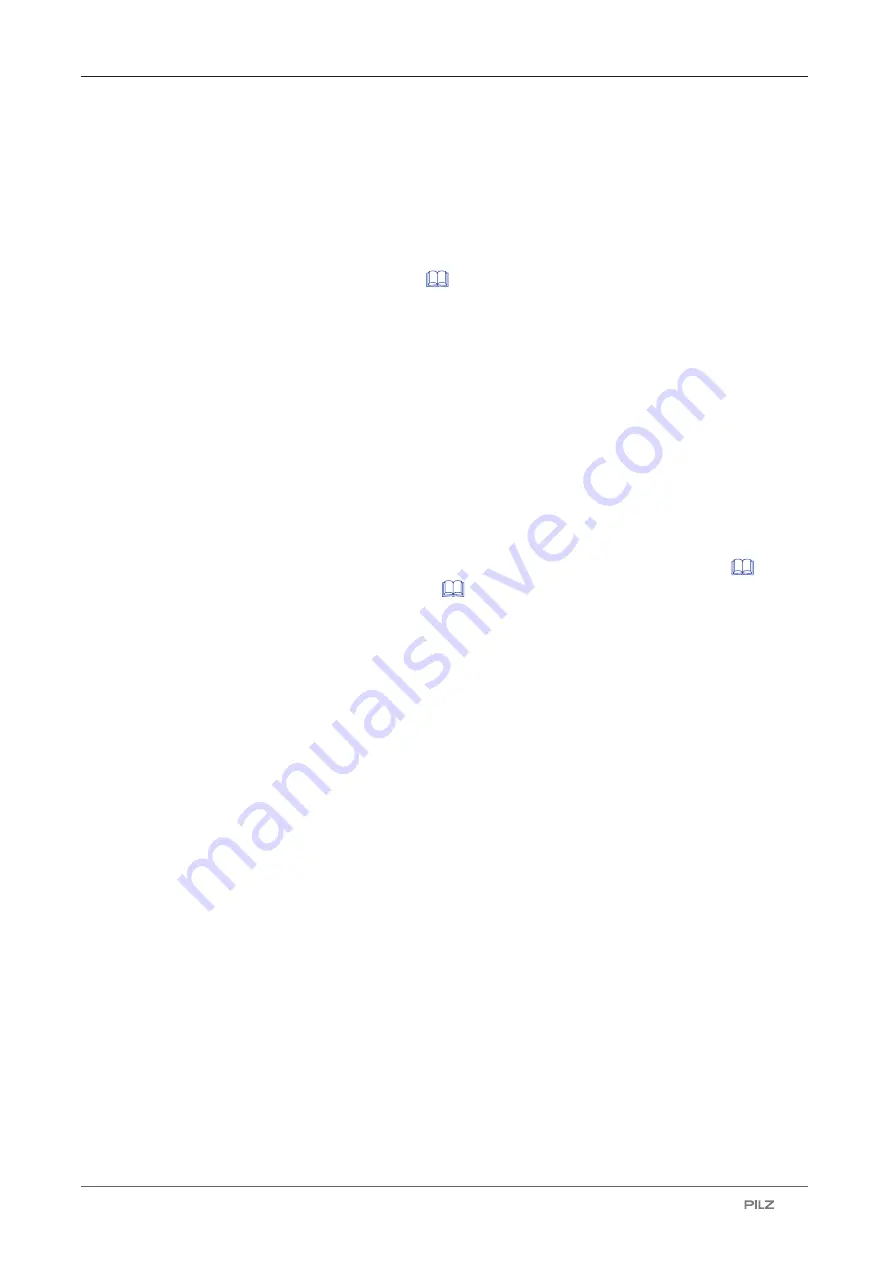
Installation
Operating Manual PSEN sg2c-5CCLLE
1004172-EN-02
| 35
6.3
Second installation of safety switch and handle unit /
upgrade for left-hinged gates
}
Remove the screw blocking the spring-loaded limit stop mechanism (see illustration in
previous section "Handle unit and actuator with screw").
}
Uninstall the safety switch from the installation site (compare steps in section entitled
Ini-
tial installation of safety switch [
28]
in reverse order).
}
Uninstall handle unit from the gate. To do this, position the screwdrivers in the slots
provided on the limit stop mechanism (see graphic "Unlock bolt").
}
Press screwdriver towards the base plate to release the spring-loaded limit stop mechan-
ism.
}
Disengage bolt tongue with handle unit in the actuator guide.
}
Remove exposed fixing screws.
}
Unscrew ball handle from the handle unit.
}
Remove the cover of the handle unit from the bolt tongue (2 countersunk screws).
}
Take limit stop from the bolt tongue and insert it from the other side into the location hole.
}
Turn bolt tongue around its longitudinal axis and screw together with the cover of the
handle unit.
}
Carry out the steps from the sections entitled
Initial installation of handle unit [
33]
and
Initial installation of safety switch [
28]
.