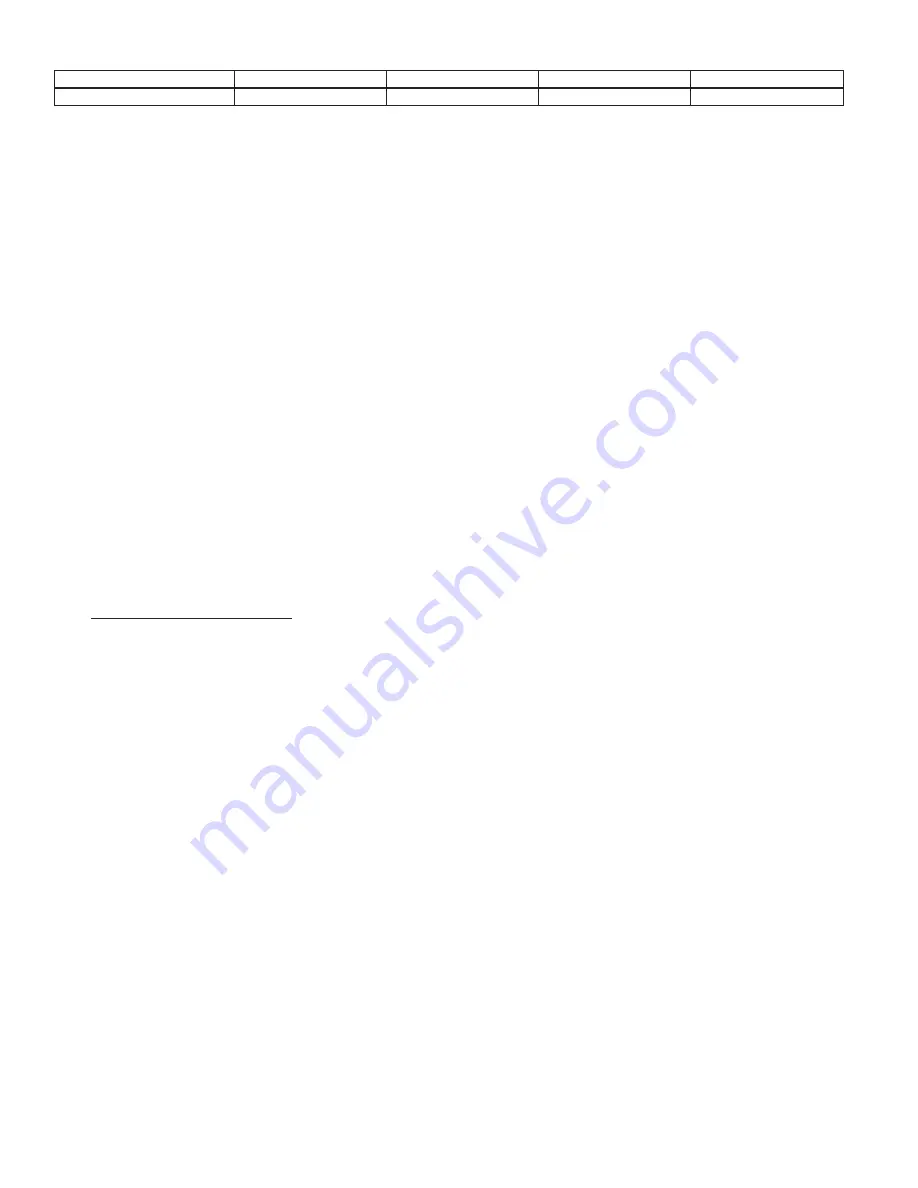
Table 19—Blower Off Delay Setup Position
PINS
1 AND 2
2 AND 3
3 AND 4
4 AND 5
Time (in sec)
90
120
150
180
A.
Check Primary Limit Control
This control shuts off gas control system and energizes air-circulating blower motor if furnace overheats. Recommended method of checking this
limit control is to gradually block off return air after furnace has been operating for a period of at least 5 minutes. As soon as limit control has
shut off burners, return-air opening should be unblocked to permit normal air circulation. By using this method to check limit control, it can be
established that limit is functioning properly and operates if there is a restricted return-air duct or motor failure. If limit control does not function
during this test, cause must be determined and corrected.
B.
Check Pressure Switch
This control proves operation of draft inducer. Check switch operation as follows:
1. Turn off 115-v power to furnace.
2. Remove main furnace door and disconnect inducer motor lead wires from wire harness.
3. Turn on 115-v power to furnace.
4. Set thermostat to call for heat and wait 1 minute. When pressure switch is functioning properly, hot surface igniter should NOT glow, and
control status code LED light flashes a Status Code 31. If hot surface igniter glows when inducer motor is disconnected, shut furnace down
immediately. Determine reason pressure switch did not function properly and correct condition.
5. Turn off 115-v power to furnace.
6. Reconnect inducer motor leads, reinstall main furnace door, and turn on 115-v power supply.
CHECKLIST
1. Put away tools and instruments. Clean up debris.
2. Verify flame rollout manual reset switch has continuity.
3. Verify that blower and main access doors are properly installed.
4. Cycle test furnace with room thermostat.
5. Check operation of accessories per manufacturer’s instructions.
6. Review User’s Guide with owner.
7. Leave literature packet near furnace.
—67—
Summary of Contents for PG9MAA
Page 70: ... 70 ...
Page 71: ... 71 ...