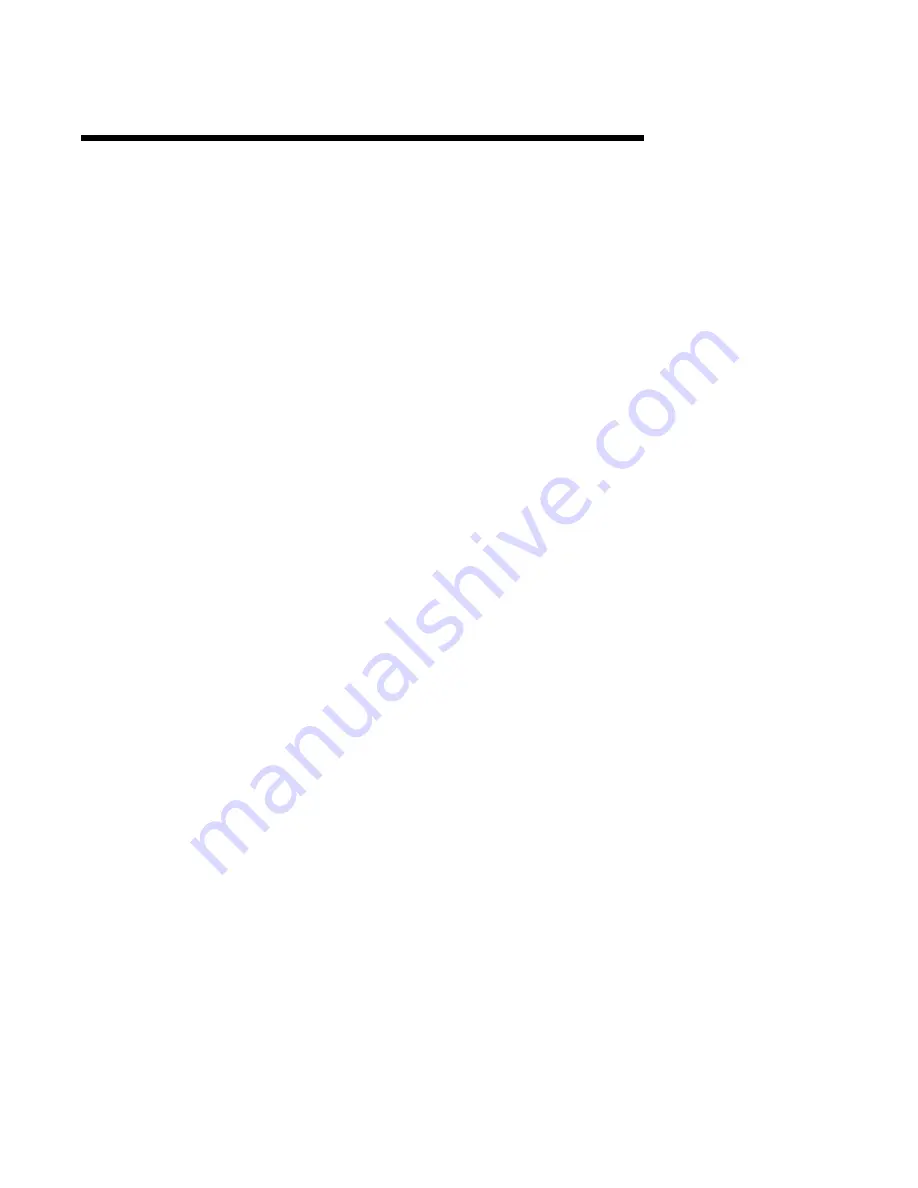
P
AGE
67
Appendix B
Glossary
Assured Soak
Assured Soak refers to the ability of the instrument to be programmed to interrupt the Soak
segment time down if the process value exceeds a deviation value selected in the Profile
Entry mode from the setpoint. The Soak timer will restart from where it was stopped when the
process value does not exceed the deviation value selected from setpoint.
Automatic Reset (Integral)
This parameter is used so that the instrument will compensate for process variable deviations
from setpoint that occur when the process load characteristics change. Instructions for
determining the automatic reset settings are given in Section 4.3 (page 44). Factory default is
0.0. Display code ArSt.
Automatic Transfer
This feature, if configured, allows manual control of the process until setpoint is reached, at
which point the controller automatically transfers from manual to automatic control. Factory
default value is 0 = no auto transfer. Display code AtFr.
Balanceless Transfer
This feature prevents changes in proportional output when changing from the Manual to
Control mode of operation. When transferring from the manual mode to the control mode, the
proportional outputs will be "Balanceless" regardless of whether the unit is inside or outside
the proportional band. This only holds true if the Auto Reset (ArSt) value is greater than 0.
Bumpless Transfer
This feature prevents step changes in proportional outputs when changing from
automatic to
manual control only.
Control Algorithm
A pre-programmed series of instructions that are used by the instrument when determining
the status of the output(s).
Cycle Time
This Tune mode parameter is used to select the on/off cycle time for time proportioning
outputs (Ct1 for Output 1 and/or Ct2 for Output 2).
When using the Position Proportioning option, Ct1 must be selected for the stroke time of the
motor.
Display Filter Factor
This parameter is adjustable from 1 to 20 which represents the number of scans of the
process variable that are averaged together before updating the displayed value. The factory
default value is 1 = no filtering. Display code dFF.
Engineering Units Upper and
Engineering Units Lower
These Program mode parameters are used with volt, millivolt, and milliamp inputs. The
Engineering Units Upper Euu should be selected as the value to be displayed when the input
is at maximum. The Engineering Units Lower EuL should be selected as the value to be
displayed when the input is at minimum.
First Output Position
This parameter is adjustable from -1000 to 1000 units and represents a shift or offset of the
on-off actuation points or proportional band for the first output relative to the normal position.
For example, a negative value could be used to offset an expected overshoot. First Output
Position also shifts the proportional band with respect to the process value range outside of
which integral action is inhibited. Factory default is 0. Display code FoP.