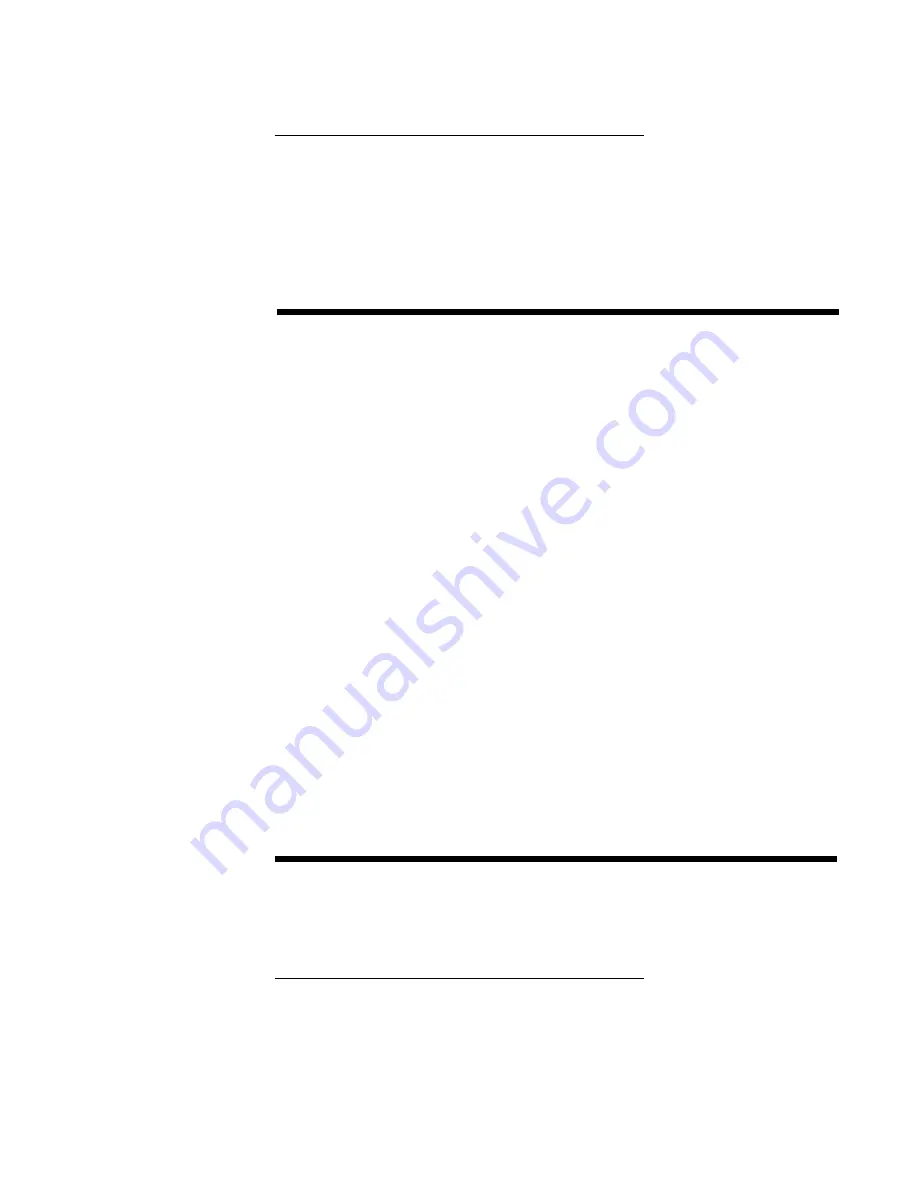
P
AGE
44
4.1.5 SETPOINT RE-TRANSMISSION OUTPUT - EO OPTION ONLY
If the instrument is provided with a current output not used for process control, this output
may be assigned to provide a linear re-transmission of the setpoint value. The setpoint
output is scaled for the application by using the Program mode parameters process/setpoint
output value upper Pou and process/setpoint output value lower PoL. The current output
resolution is @ 200 steps, so for the best re-transmission accuracy, the span between Pou
and PoL should be as small as possible. If a current output is used for re-transmission, the
corresponding control output, out1 or out2, cannot be assigned to it.
Alarm Operation 4.2
The type of alarm is selected in the Program mode as follows:
1. Process Alarm Direct - the alarm will be on if the process value is greater than the process
value selected.
2. Process Alarm Reverse - the alarm will be on if the process value is less then the process
value selected.
3. Deviation Alarm Direct - the alarm will be on if the process value is greater than the
setpoint plus the deviation value selected.
4. Devation Alarm Reverse - the alarm will be on if the process value is less than the
setpoint plus the devation value selected.
5. Deviation Band Alarm Open Within - the alarm will be on if the process value is greater
than one half the deviation band alarm values selected above or below the setpoint.
6. Deviation Band Alarm Closed Within - the alarm will be on if the process value is less than
one half the deviation band value selected above or below the setpoint.
The alarm will be active while the instrument is in the Control mode or while the profile is
running. Relay and solid state relay drivers can be assigned to provide output capability to
the alarm function.
The alarm value (Process, deviation or bandwidth) is selected in the Tune mode.
Alarm output chatter can be reduced by using the hysteresis parameter in the Program mode
to create a deadband around the alarm point.
Tune Mode Operation 4.3
Proportional output control may require the adjustment (tuning) of the PID and other related
parameters. This provides a means for the instrument's control algorithm to be adjusted to
meet specific application requirements.
4.3.1 SYSTEMATIC TUNING METHOD
1. Changes in tuning parameters should be made one at a time.
2. After making any changes in tuning parameters, a disturbance should be introduced into
the process so that the process reaction may be observed. This process reaction, or
recovery, will tell whether the tuning parameters provide the desired control. It is usually
easiest to make a step change in setpoint to introduce this disturbance.