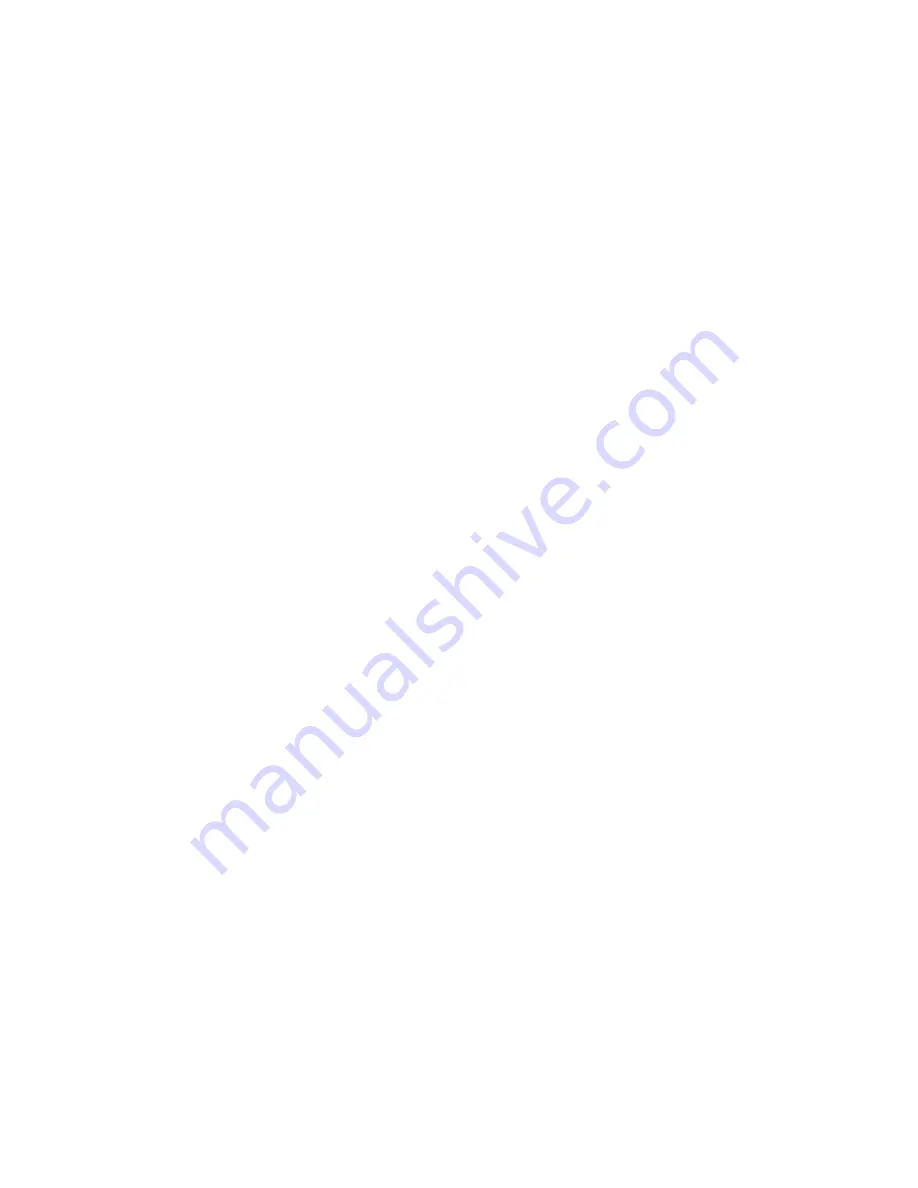
P
AGE
41
11
Profile Loop Count
PLCt
Press the SCROLL key to see the
Remaining
Profile Loop Count Remaining for the
last active profile.
12
Profile Loop Remaining
X
If necessary, use the UP and DOWN
key to adjust the Profile Loop Count
Remaining value.
To start a profile running, press the RUN/HOLD key while in the Profile Continue mode. If no
changes were made to any of the Profile Continue parameters, press the RUN/HOLD key
twice. The profile selected will start at the point selected.
4.1.2.4 ON-OFF CONTROL
On-Off control can only be implemented on controllers provided with SPST relay or SSR
driver output(s). On-Off operation can be assigned to either or both output 1 and 2. The
On-Off control can be selected as direct or reverse acting. Direct action is typically used in
cooling applications. The output device will turn on when the process value is greater than
the setpoint. Reverse action is typically a heating application. The output device will turn on
if the process value is below the setpoint. A hysteresis adjustment is provided for On-Off
outputs. This adjustment is in terms of degrees/engineering units and defines the width of
the
hysteresis bandwidth about the setpoint. This parameter may also be referred to as a dead
band. Relay chatter can be eliminated by proper adjustment of this parameter. When
operating in On-Off control, the control algorithm will turn the output on or off depending upon
the setpoint, the relative position of the process value, and the hysteresis adjustment. The
respective OUT1 or OUT2 indicator will illuminate to indicate that the output device is on.
The hysteresis will also affect the operation of the alarm output if used.
4.1.2.5 TIME PROPORTIONING CONTROL
Time Proportioning Control can be implemented on controllers provided with SPST relay or
SSR driver output(s). Time proportioning can be programmed for output 1 and/or 2. Time
Proportioning control is accomplished by cycling the output on and off when the process
value is within the proportional bandwidth selected at a prescribed time period. The time
period is selected in the Tune mode by adjusting Ct1 and/or Ct2. The on time is a percent-
age of the Cycle Time.
Example:
Calculated output % = 40%;
Cycle Time adjustment = 20 seconds
Output on time = .4 x 20 = 8 seconds
Output off time = .6 x 20 = 12 seconds
4.1.2.6 CURRENT PROPORTIONING CONTROL
Current Proportioning control provides a proportional current output in response to process
value and setpoint. The current output can be selected for direct or reverse operation. Direct
current output control is typically used for cooling applications. The current output will
increase as the process value increases within the proportional bandwidth selected. The
reverse current output control is typically used in heating applications. The current output will
decrease as the process value increases within the proportional bandwidth selected.
The instrument can be programmed to provide 0 to 20mADC or 4 to 20mADC (if EO option is
present) current output(s). The output selected is dependent upon the final control element
being used in the process. The output 1 and/or output 2 LED will be lighted whenever the
Current Proportional outputs are selected.