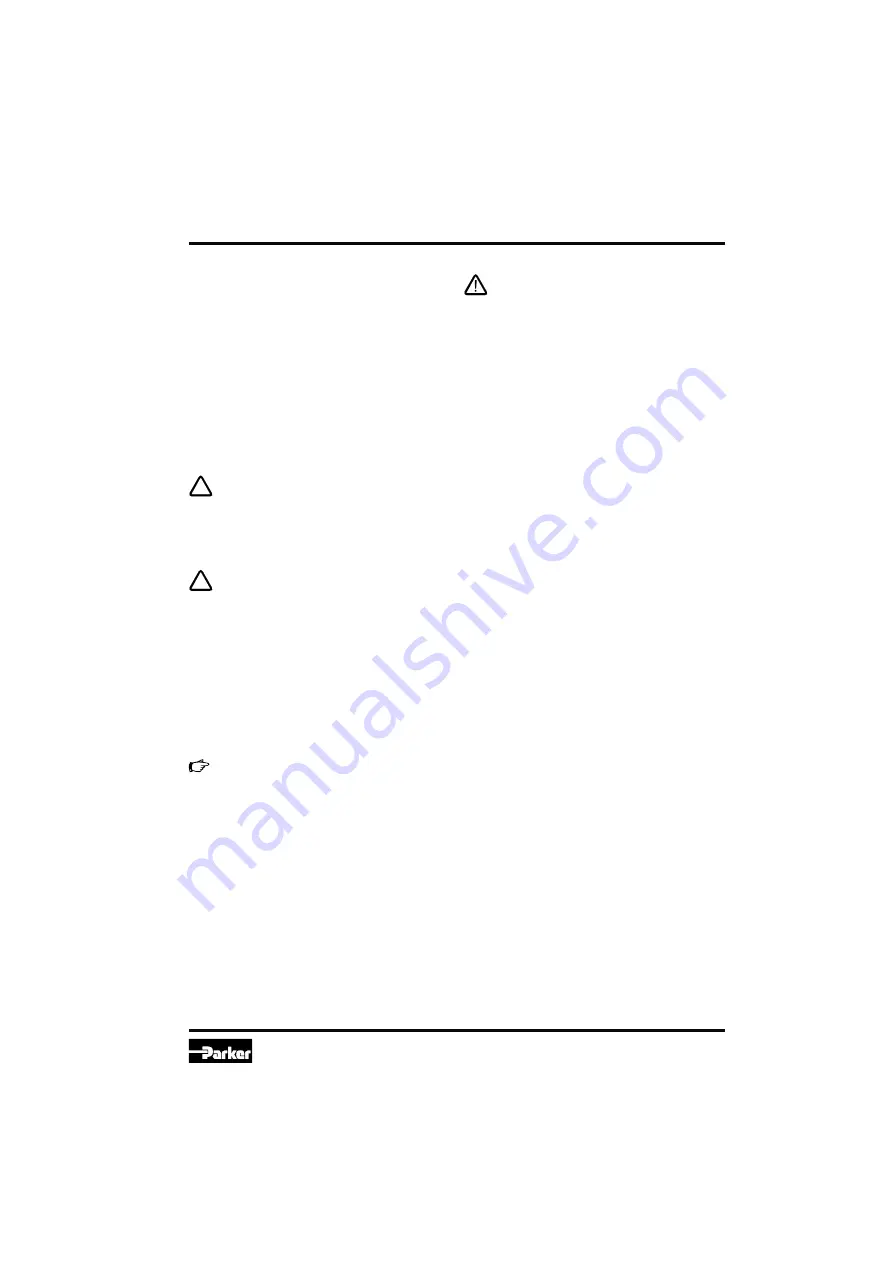
Prop. Directional Control Valve
Series D*FB / D*1FB
Operation Manual
25
D_FB-D_1FB 5715-669 UK.indd CM
Parker Hannifin GmbH
Hydraulic Controls Division
Air Bleeding of Hydraulic System
During initial startup, after an oil change as well as
after the opening of lines or valves the hydraulic
system must be air bleeded. Air in the hydraulic
system is very disadvantageous and therefore
undesirable for the control system. The pipeline
network is vented at its highest point. The fitting
may be loosened a little so that the air can escape
with only a small amount of oil loss. When the oil
is no longer foaming, the fitting is re-tightened.
Afterwards all functions are run through, one after
the other, in no-load operation with low pressure
and with full cylinder stroke. Afterwards the system
should be vented once more.
After air bleeding the oil level in the tank must
be checked, and refilled as necessary!
Filter
The function and lifetime of the valve are strongly
affected by the cleanliness of the fluid.
Dirt is the greatest enemy of the hydraulic
system!
There are three important sources of dirt to watch
for:
• contamination arising during installation
• contamination arising during operation, friction
wear
• impurities from the environment
Basically a purity level class of 7 acc. NAS 1638
is required.
Pay attention to maintenance details!
Flushing
It is recommended to flush the long pipelines by short
circuiting the pressure and return lines, especially
for large, central pressure oil stations. This prevents
the installation dirt from entering the valve.
6. Maintenance
Service work may only be carried out by
qualified personnel. Detailed knowledge of
the machine functions concerning switching
on and off as well as of the required safety
relevant technical tasks is required!
Periodical maintenance is essential for the longevity
of the system and guarantees reliability and avail-
ability. The following properties of the system has to
be checked in continuous short time intervals:
• oil level in the tank
• max. working temperature
• condition of the pressure fluid (visual inspection,
colour and smell of hydraulic fluid)
• working pressure levels
• gas pre-load pressure on the pressure accumu-
lator
• leakage on all system components
• condition of filter elements
• condition of hose lines
• cleanliness of components
After a certain operating duration a change of the
hydraulic fluid is required. The frequency of change
depends from the following circumstances:
• kind resp. grade of the pressure fluid
• filtering
• operating temperature and environmental
conditions
29
29