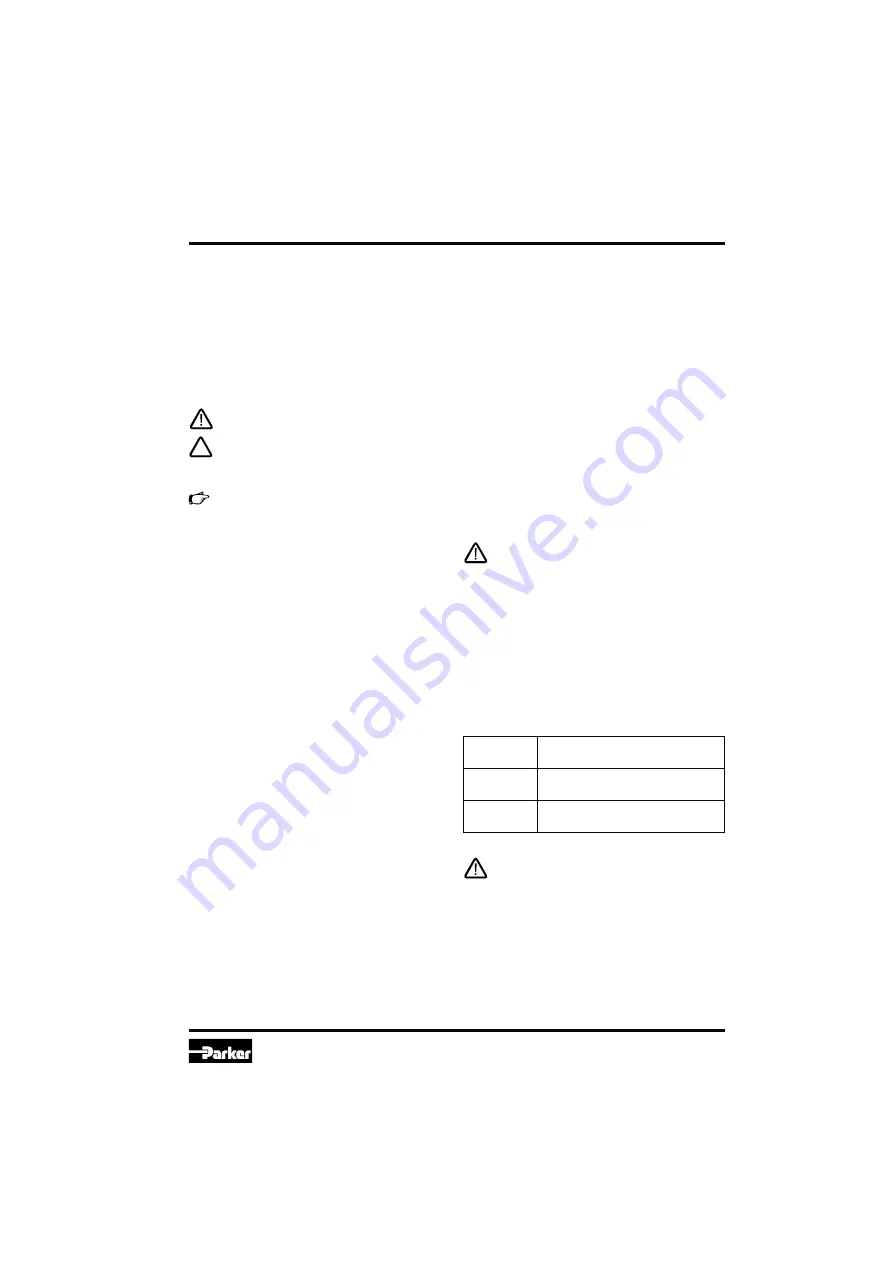
Prop. Directional Control Valve
Series D*FB / D*1FB
Operation Manual
9
D_FB-D_1FB 5715-669 UK.indd CM
Parker Hannifin GmbH
Hydraulic Controls Division
2. Safety Instructions
Please read the operation manual before instal-
lation, startup, service, repair or stocking! Paying
no attention may result in damaging the valve or
incorporated system parts.
Symbols
This manual uses symbols which have to be fol-
lowed accordingly:
Instructions with regard to the warranty
Instructions with regard to possible
damaging of the valve or linked system
components
Helpful additional instructions
Marking, Name Plates
Instructions applied on the valve, i.e. wiring dia-
grams and name plates, must be observed and
maintained legibly.
Work at the Valve
Workings in the area of installation, commissioning,
maintenance and repair of the valve may only be
allowed by qualified personnel. This means persons
which have, because of education, experience and
instruction, sufficient knowledge on relevant direc-
tives and approved technical rules.
3. Important Details
Intended Usage
This operation manual is valid for proportional
directional control valves D*FB/D*1FB series. Any
different or beyond it usage is deemed to be as not
intended. The manufacturer is not liable for warranty
claims resulting from this.
Common Instructions
We reserve the right for technical modifications of
the described product. Illustrations and drawings
within this manual are simplified representations.
Due to further development, improvement and
modification of the product the illustrations might
not match precisely with the described valve. The
technical specifications and dimensions are not
binding. No claim may resulting out of it. Copyrights
are reserved.
Liability
The manufacturer does not assume liability for
damage due to the following failures:
• incorrect mounting / installation
• improper
handling
• lack of maintenance
• operation outside the specifications
Do not disassemble the valve! In case of
suspicion for a defect please return the valve
to the factory.
Storage
In case of temporary storage the valve must be
protected against contamination, atmospheric ex-
posure and mechanical damages. Each valve has
been factory tested with hydraulic oil, resulting in
protection of the core parts against corrosion. Yet
this protection is only ensured under the following
conditions:
Outdoor storage or within sea and tropical
climate will lead to corrosion and might disable
the
valve!
Storage
period
Storage requirements
12 months
constant humidity < 60% as well
as constant temperature < 25°C
6 months
varying humidity as well as
varying temperature < 35°C
13
13