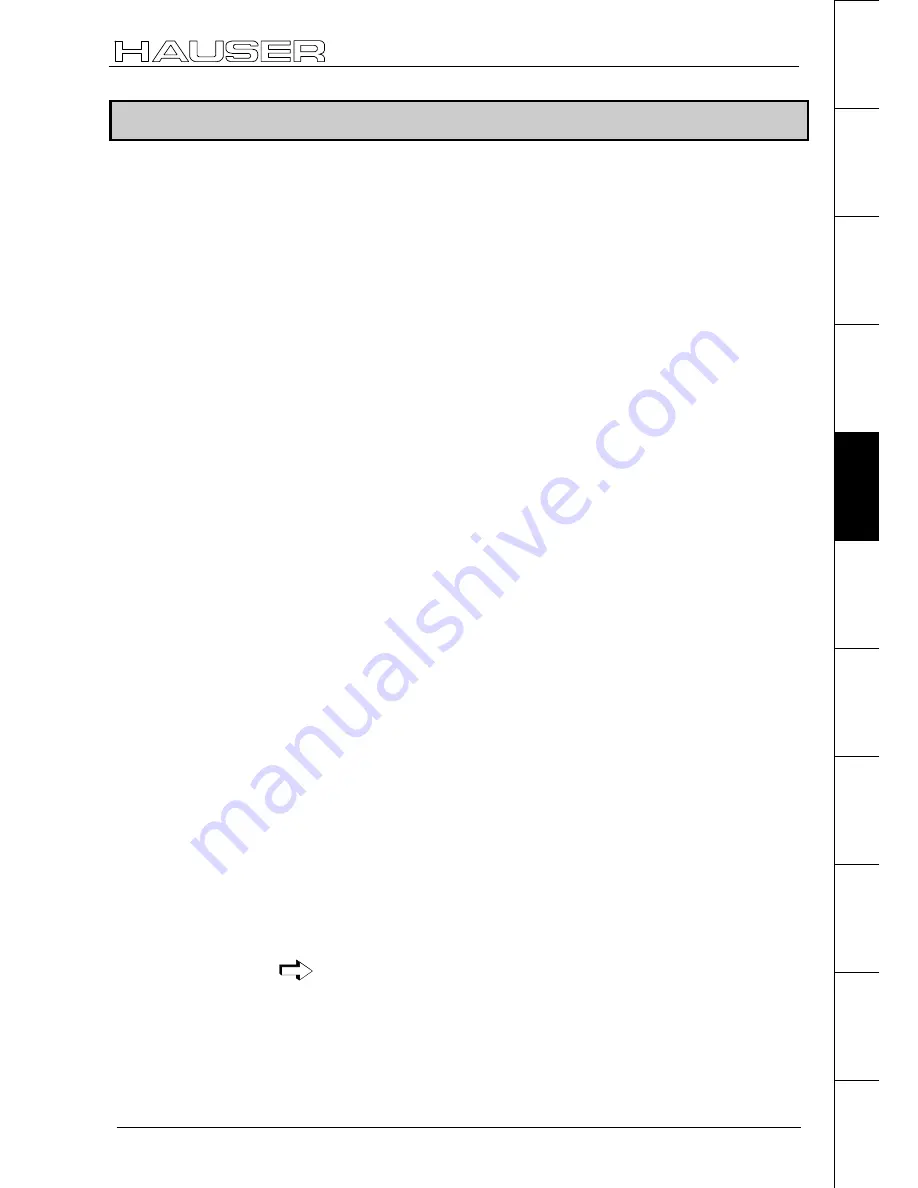
Positioning and control functions
Individual configuration of synchronous motors
95
Unit
hardware
Connector
assignment / cable
Technical data
Configuration
Positioning and
control functions
Optimization
functions
Interfaces
Accessories /
options
Status
Parameter
Error list
8.4
Positioning and control functions
The COMPAX basic unit is designed to meet the technical control requirements of
a servo axis. Special control commands are implemented in the different unit
variants for synchronisation or gearing functions. The support of a superordinate
control unit is required for more complex systems, especially for the co-ordination
of several axes. Parker supplies solutions based on PCs and PLCs, as well as the
compact industrial computer COMTAC as a multi-axis simultaneous control unit.
Up to 250 sequentially numbered sets of commands can be stored in the COMPAX
program memory. Program execution can be controlled via data interfaces or
binary inputs/outputs. It is possible to select addresses (data record selection)
using the interpretation of the adjoining binary input signals (external data record
selection).
The command set structure has been deliberately kept simple and resembles the
well-known programming language Basic. Program control instructions, comparator
functions, setting/resetting of outputs and the motion-related commands for
specifying velocity, position, acceleration time, etc. are also possible.
N001:
ACCEL 250
acceleration time 250 ms
N002:
SPEED 80
velocity 80%
N003:
REPEAT 10
specified wait loop 1s
N004:
IF I7=1 GOTO 9
query I7 to log. 1
N005:
WAIT 100
waiting time 100 ms
N006:
END
end REPEAT loop
N007:
OUTPUT O7=1
sets output; no positioning
N008:
GOTO 13
N009:
POSA 1250
positioning
N010:
OUTPUT O8=1
sets O8 for 500 ms
N011:
WAIT 500
N012:
OUTPUT O8=0
N013:
END
The range of commands used with the compact COMPAX servo control unit is
deliberately different in terms of type and range to the standardized NC
programming standards as described in DIN 66024 and DIN 66025. COMPAX is
not designed with the control and calculation capability of a complete CNC
controller, even though it can perform many CNC functions.
All commands are processed in sequence (sequential step programming). The
program can be interrupted or suspended using a break or stop signal. The axis is
then decelerated using the preset time delay. The program can then be continued
from another point.
Once "Power on" is in place, the data record indicator is at 1. If the program is to
started at another point, the data record indicator can be adjusted using the
command "GOTO xxx" (The direct command is only recognized by COMPAX if A4
"Ready for start" ="1").
Using the "START" command (via the digital Input I5 or using the direct "START"
command via an interface), you can start the program from the selected data
record number.
The data record indicator is set to 001 using the "Find machine zero" or
"Approach real zero".
This function can be set to binary inputs using parameter P211.
Program example:
Start program