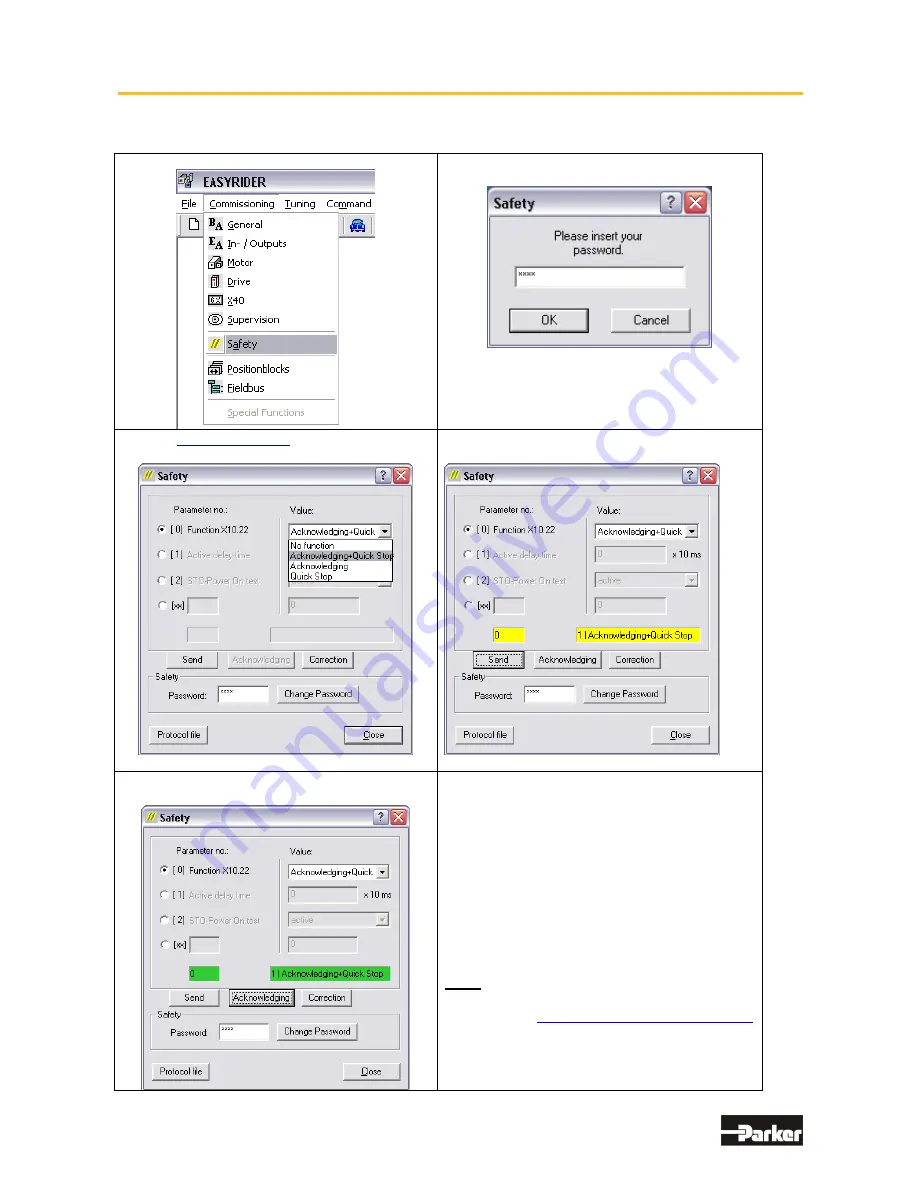
9
Safe
Safe
Safe
Safe Torque
Torque
Torque
Torque Off (STO)
Off (STO)
Off (STO)
Off (STO)
07-02-12-02-EN-V1215.doc / Type:
638
89
●
EASYRIDER Safety Parameter Data Entry Dialog Boxes
1. Commissioning menu - select “Safety“ :
2. Access password - enter “BGSM“
and verify with “OK“
3. Enter
Safety Password
, select Parameter
Nr. and enter the appropriate Value
4. Send the Parameter - press “Send”one time
4. When the yellow display is correct - press
the “Acknowledge” button twice to accept
5. When the parameter display is
green,
it
confirms that the value is correct, has been
stored and power loss protected in the drive
unit!
Once all of the relevant safety data
parameters have been entered, then it is
possible to call up the protocol form of the
actual safety parameter settings by pressing
the “Protocol file” button.
(ACROBAT Reader is required!)
Note:
A copy of the
Safety-Parameter-Protocol Form
is available in the appendix of the Servo Drive
Handbook and can be used for verification
purposes.
This manual was downloaded on www.sdsdrives.com
+44 (0)117 938 1800 - [email protected]