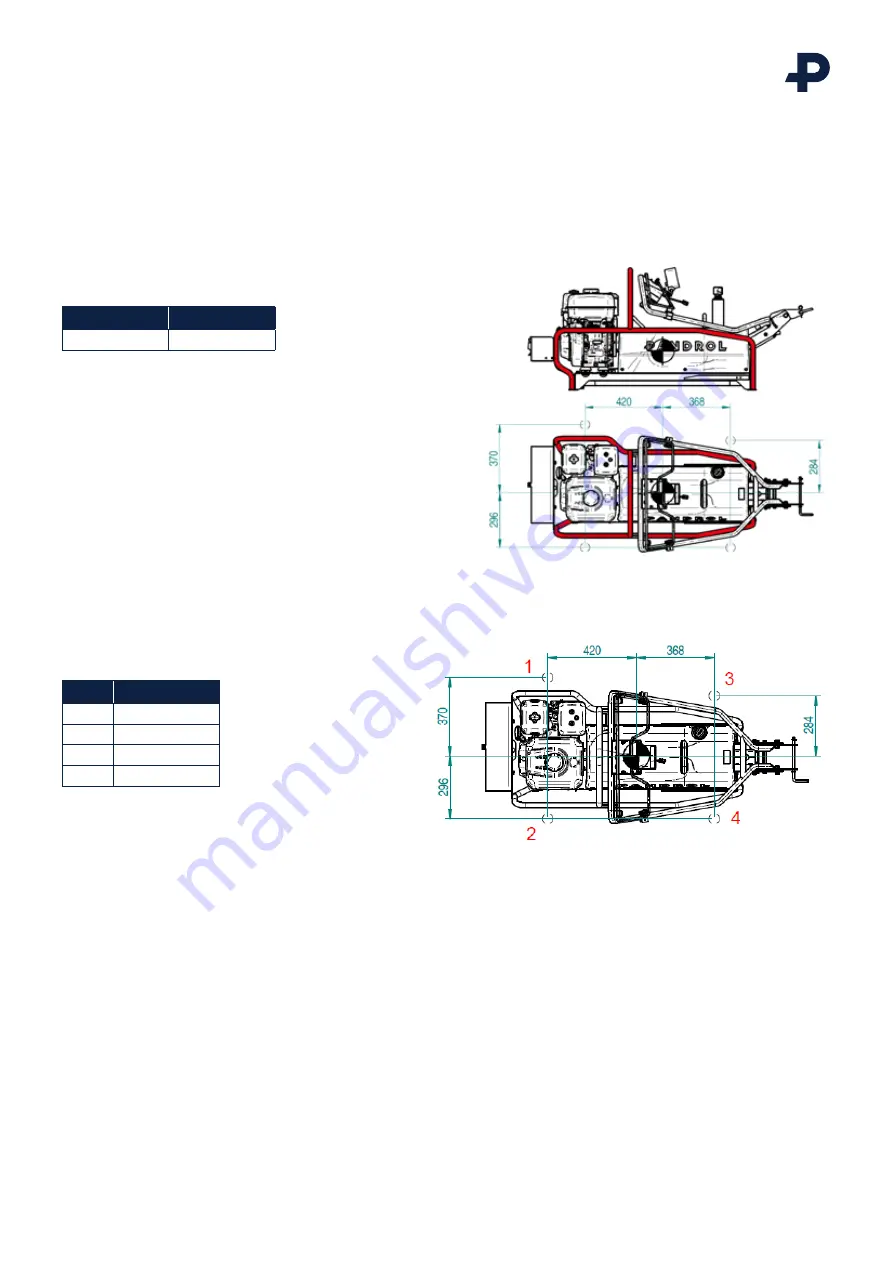
45 av 82
OPERATION AND MAINTENANCE MANUAL I ENG_OMM_CD200IQ_P03 I 2023-03-16
@Pandrol 2023
Fig 50. Overview lifting handles Powerpack
7.4.2. Manual Handling Power Pack
Fig 51. Weight balance Powerpack
Ì
VARNING! HEAVY WEIGHT
Description
Weight (kg)
Powerpack
103
Weight Table
Pos.
Weight (kg)
1
22
2
27
3
27,5
4
26,5
Weight Balance Powerpack
Summary of Contents for CD200 IQ
Page 2: ...2 av 82 OPERATION AND MAINTENANCE MANUAL I ENG_OMM_CD200IQ_P03 I 2023 03 16 Pandrol 2023...
Page 53: ...53 av 82 OPERATION AND MAINTENANCE MANUAL I ENG_OMM_CD200IQ_P03 I 2023 03 16 Pandrol 2023...
Page 80: ...80 av 82 OPERATION AND MAINTENANCE MANUAL I ENG_OMM_CD200IQ_P03 I 2023 03 16 Pandrol 2023...
Page 81: ...81 av 82 OPERATION AND MAINTENANCE MANUAL I ENG_OMM_CD200IQ_P03 I 2023 03 16 Pandrol 2023...