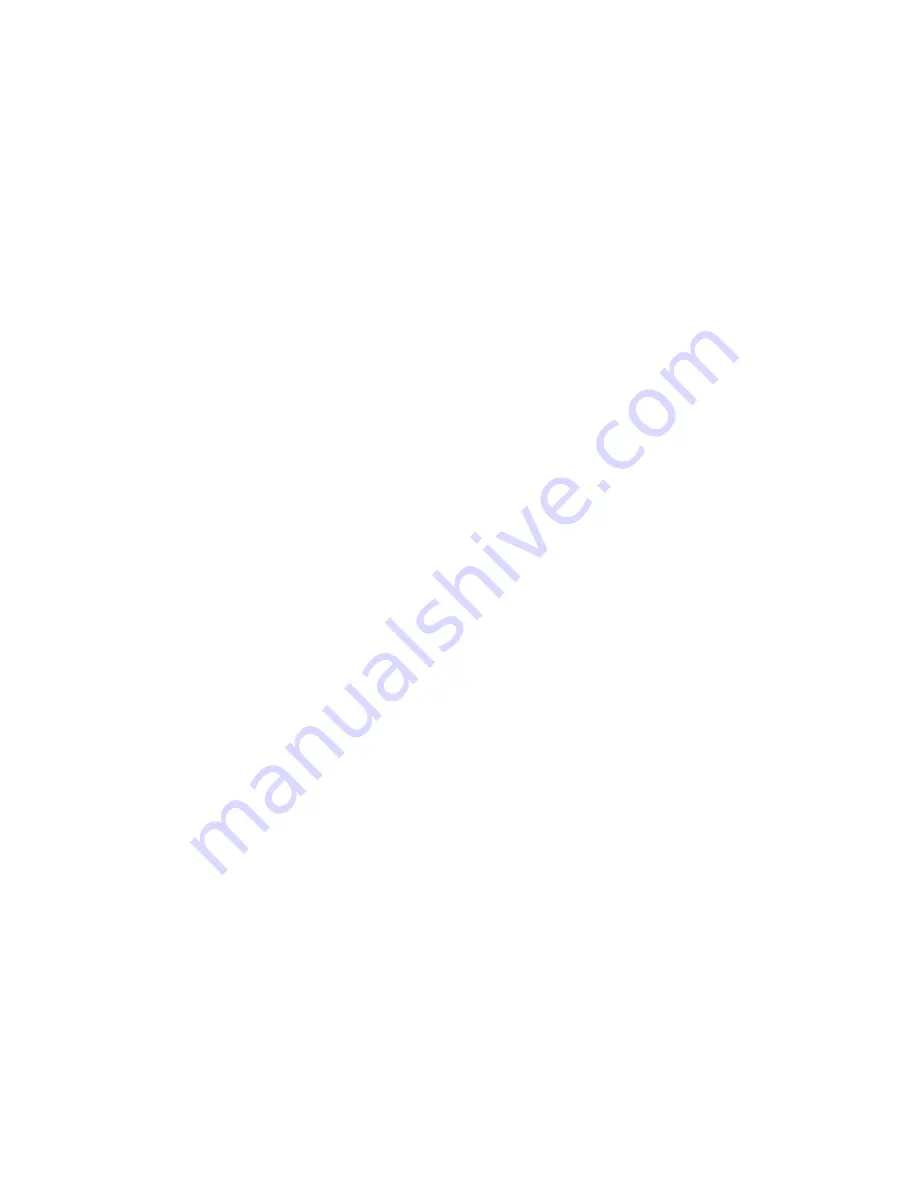
©2016 PACE Inc., Vass, North Carolina,
All Rights Reserved
Page
17
Procedure
It is recommended to conduct a trial operation each day before commencing with production to ensure
the heater temperatures will be uniform and that everything is operating correctly. It is important to verify if the
machine is providing adequate airflow. Insufficient airflow can be detrimental to the job at hand and possibly
cause damage to the machine itself if there is not enough airflow when the heater element is in operation.
Before operation, check for any components on both the top and bottom of the PCB that may not fit in
the TF-1800. Ensure the components are not going to crash into the heater head or camera arm as they move
up/down and in/out. Also check that the bottom heater will not be obstructed and does not make physical
contact with components on the board as this could cause uneven heating.
Production Mode
Example component installation – Note: If at any time you need to abort the process, click
on the red abort button.
1)
Turn on the TF machine and PC, and then run the TF software.
2)
Navigate to the Production Mode screen if not already there.
3)
Load a profile using the Load Profile button.
4)
Install the proper vacuum pick.
5)
Install the proper nozzle.
6)
Click “Start Process” and follow the onscreen instructions which will guide you through the
following steps.
7)
Place the PCB between the arms of the board holder and position the board so the red
laser point is in the center of the placement site and tighten the board holder retention
screw.
8)
Apply flux to the board if needed, and attach any thermocouples desired for additional
process monitoring. Adjust the Board Support Wand as needed.
9)
Place the component in the mounting plate on top of the camera housing. The component
needs to have the same orientation as the nozzle. Click “okay”.
10)
The BGA workstation will pick up component. If the vacuum pick fails to pick up the
component, reset the component in the nest and click retry.
11)
If Auto Flux Dip is selected, replace the component nest with the flux dip tray and follow
onscreen directions. After fluxing is complete, restore flux dip tray and component nest to
their original locations.
12)
Slide component nest out of the way, towards the back of the machine so the optics are
unobstructed.
13)
The component alignment screen will appear and the heater head will move down to the
focal position.
14)
Adjust the zoom and lighting as needed in order to see the pads on the PCB as well as
the solder balls or leads on the component. Then using the theta adjustment and X/Y
micrometers, align the component to the PCB.
15)
After alignment is complete, click the Alignment Complete button to prepare for heating.
16)
If auto placement is active, the heater head will place the component and nozzle into
position over the board. Otherwise, use the onscreen adjustments to manually lower the
heater head into final position.
17)
Make sure any extra thermocouples being used are in the correct location and click the
Start Heating Button.
18)
The selected temperature profile will run.
19)
Allow the PCB to cool and remove.