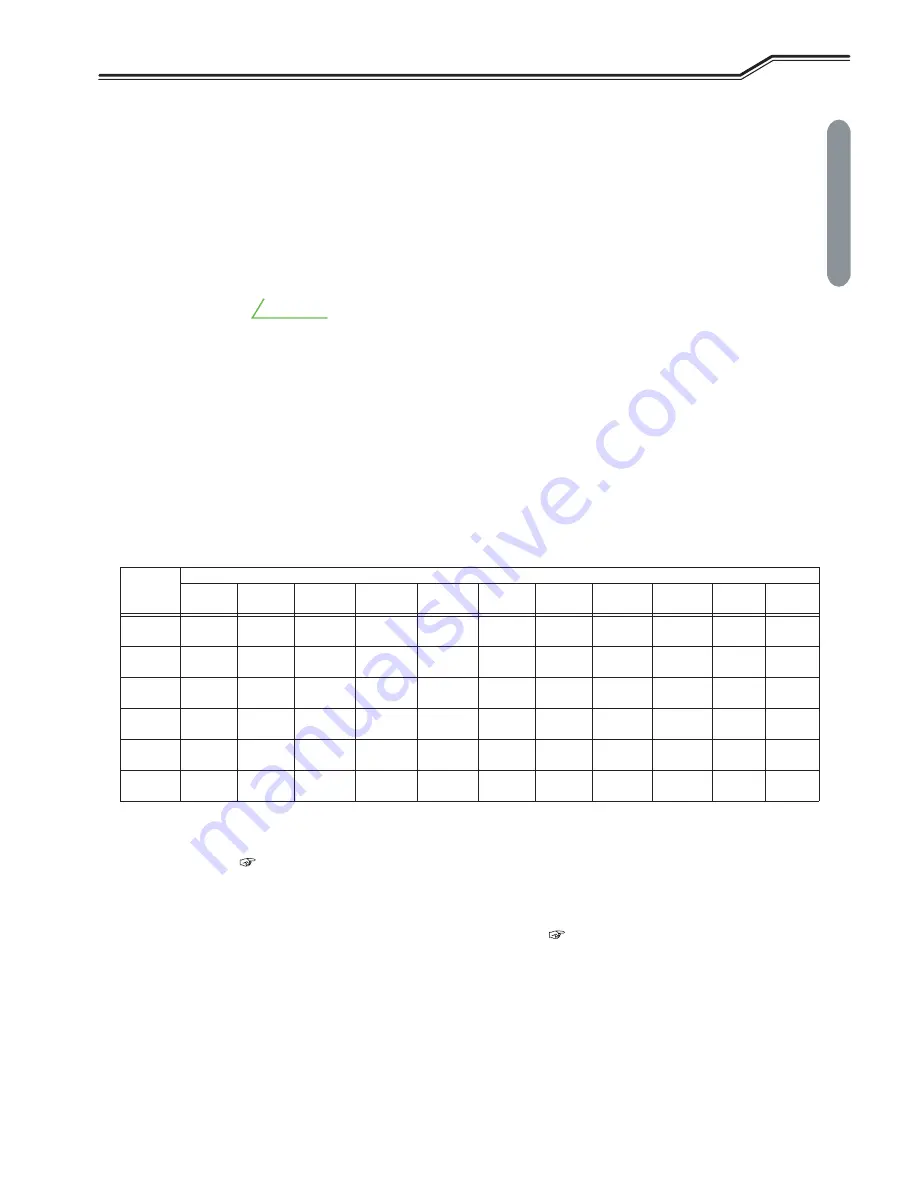
111
Chapter 7
Administrator F
unctions
W
ELDING
R
ESULT
C
ONTROL
F
UNCTION
A
DMINISTRATOR
F
UNCTIONS
C
HAPTER
7
7.2.2.2
Wire consumption
Wire consumption is controlled according to the setting range.
•
P20 (Cumulative wire consumption used in welding)
Wire consumption [lbs (kg)] used in welding is measured and counted.
The setting range of count value is between 0 and 9999 lbs (0 and 4535 kg). The count value will be cleared according
to the "P22" setting.
(If continuous operation is enabled, the value will be cleared when exceeding 9999 and returns to 0.)
T I P S
•
Approximate wire consumption will be obtained with the wire consumption control
function. The wire consumption may be different from the actual wire consumption due
to reasons such as slipping of wire.
The table below shows the wire unit amount [lbs (g/m)] calculated from the specific
gravity (g/cm
3
) of the wire material. Wire consumption is calculated based on the unit
amount and the wire feeding amount during welding. Therefore, there will be differences
between the actual consumption and the calculated value depending on the wire
constituents.
•
When wire consumption is 220.5 lbs (100 kg) or lower, the value after the decimal point
is also displayed.
•
The wire consumption used in inching or wire slowdown is not measured.
•
Special wires not listed in the table below are not measured.
•
P21 (Target wire consumption)
Select the target value of wire consumption in the range from 0 and 9999 lbs (0 and 4535 kg).
When the "P20" count value reaches the wire consumption specified here, an alarm appears indicating that the target
is achieved. (
7.2.2.6
-
Alarm indication when target is achieved)
•
P22 (Operation at the time when the target wire consumption is achieved)
Select the operation from 0 to 5 for the time when the target specified for "P21" is achieved.
The set values and operations when the target is achieved are the same as those of the "P12" function. "P12 (Operation
at the time when the target number of welding points is achieved)" (
7.2.2.1
-
Number of welding point)
7.2.2.3
Total welding time
The total welding time is controlled according to the setting range.
•
P30 (Cumulative total welding time)
Every interval from the start of current flowing triggered by the torch switch ON to the stop of output triggered by
the torch switch OFF is counted and accumulated as welding time.
The setting range of count value is between 0 and 9999 minutes. The count value will be cleared according to the "P32"
setting. (If continuous operation is enabled, the value will be cleared when exceeding 9999 and returns to 0.)
*2: If "Disabled" is selected and the target is achieved, next welding cannot start until any key on the operation panel is pressed.
Wire
diameter
[in. (mm)]
Unit amount [lbs (g/m)]
Mild steel
solid
Mild steel
cored
Stainless
steel
Stainless
ferrite
Stainless
cored
Brazing
CuSi
Brazing
CuAl
Soft
aluminum
Hard
aluminum
Inconel
Titanium
.030 (0.8)
0.0086
(3.9)
−
0.0088
(4.0)
0.0086
(3.9)
−
0.0099
(4.5)
0.0099
(4.5)
−
−
−
−
.035 (0.9)
0.0110
(5.0)
−
0.0112
(5.1)
0.0108
(4.9)
0.0093
(4.2)
−
−
−
−
0.0119
(5.4)
−
.040 (1.0)
0.0137
(6.2)
0.0137
(6.2)
0.0139
(6.3)
0.0132
(6.0)
−
0.0157
(7.1)
0.0157
(7.1)
−
0.0046
(2.1)
0.0214
(9.7)
0.0079
(3.6)
.045 (1.2)
0.0196
(8.9)
0.0163
(7.4)
0.0198
(9.0)
0.0192
(8.7)
0.0163
(7.4)
0.0225
(10.2)
0.0225
(10.2)
0.0066
(3.0)
0.0066
(3.0)
−
0.0115
(5.2)
.052 (1.4)
0.0267
(12.1)
0.0223
(10.1)
−
−
−
−
−
−
−
−
−
1/16 (1.6)
0.0348
(15.8)
0.0291
(13.2)
0.0351
(15.9)
−
0.0291
(13.2)
−
−
0.0119
(5.4)
0.0119
(5.4)
−
−