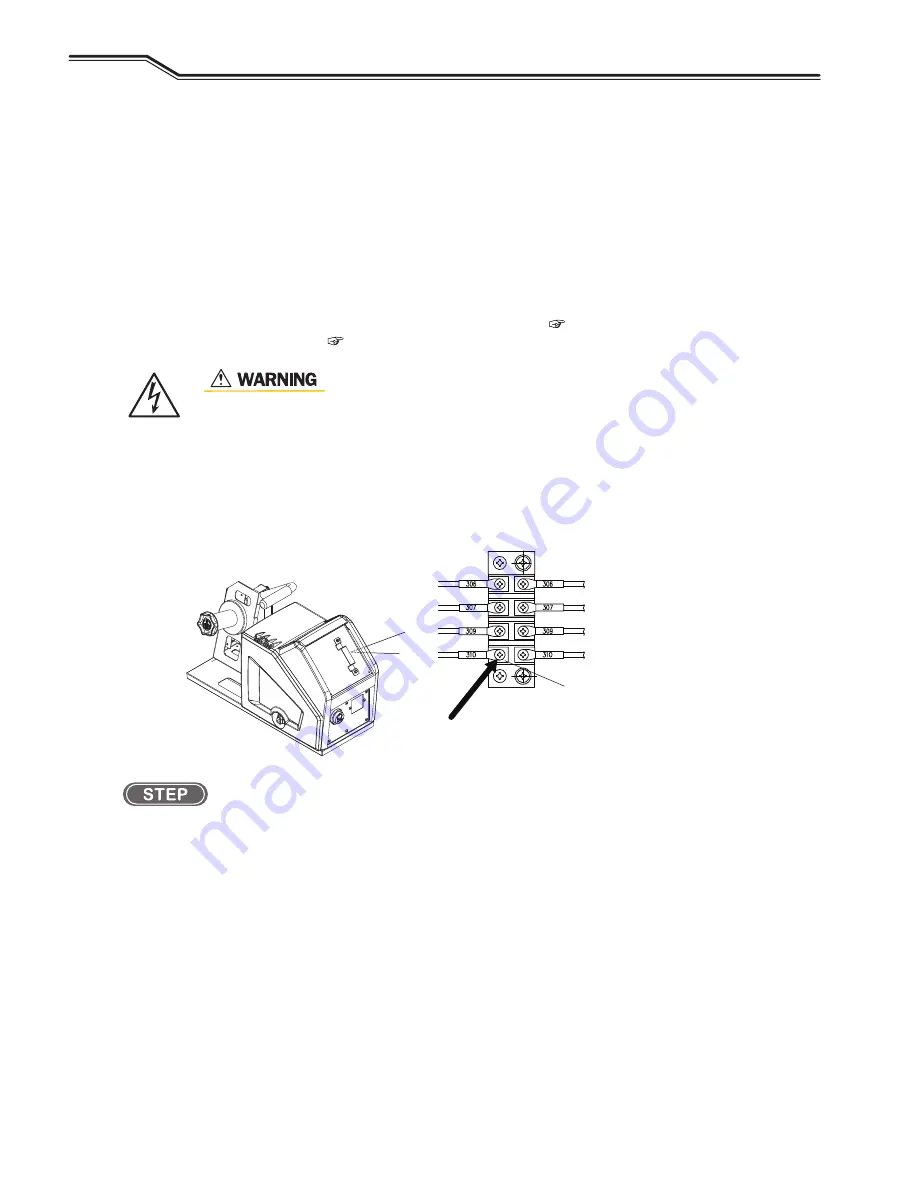
W
IRING
OF
V
OLTAGE
D
ETECTION
C
ABLE
AT
B
ASE
M
ETAL
S
IDE
C
ONNECTION
C
HAPTER
4
44
5.
Check the wiring and place the cover for external connection back to the welding power source.
4.6 Wiring of Voltage Detection Cable at Base Metal Side
When the extension cable is 99 ft (30 m) or more in length in total, use of the voltage detection cable at the base metal side
is recommended.
The voltage detection cable needs to be wired so that the correct feedback of the arc voltage can be obtained. Connect the
voltage detection cable as near as possible to the base metal to avoid detection of voltage decrease.
Use the voltage detection cable at base metal (optionally available: K5416N00 or K5416G00) by connecting with the wire
feeder or to the voltage direct detection terminal at the base metal side on the front of welding power source.
When using the voltage detection cable, set the internal function F38 to "1". (
6.7.1
-
Setting procedure)
Details on the internal function F38 (
6.7.2.27
-
F38: Arc voltage direct detection switching)
4.6.1
Wiring to wire feeder
This section explains how to connect the voltage detection cable at the base metal side to the wire feeder.
1.
Check that input power is turned off with the disconnect switch connected to the welding power source.
2.
Remove the right side panel of the wire feeder.
3.
Connect the voltage detection cable at the base metal side to the terminal board in the wire feeder (wire No.
310).
●
Use the voltage detection cable at the base metal side via the blind bush with film.
4.
Restore the right side panel of the wire feeder.
Wiring of voltage detection cable is complete.
•
Ensure to start the operation only after shutting off the input power by the contactor of
the power distribution box connecting the welding power source. Otherwise, electric
shock may occur.
Wire feeder
Connection part of
voltage detection cable
Terminal block
Jointly fasten with
wire 310