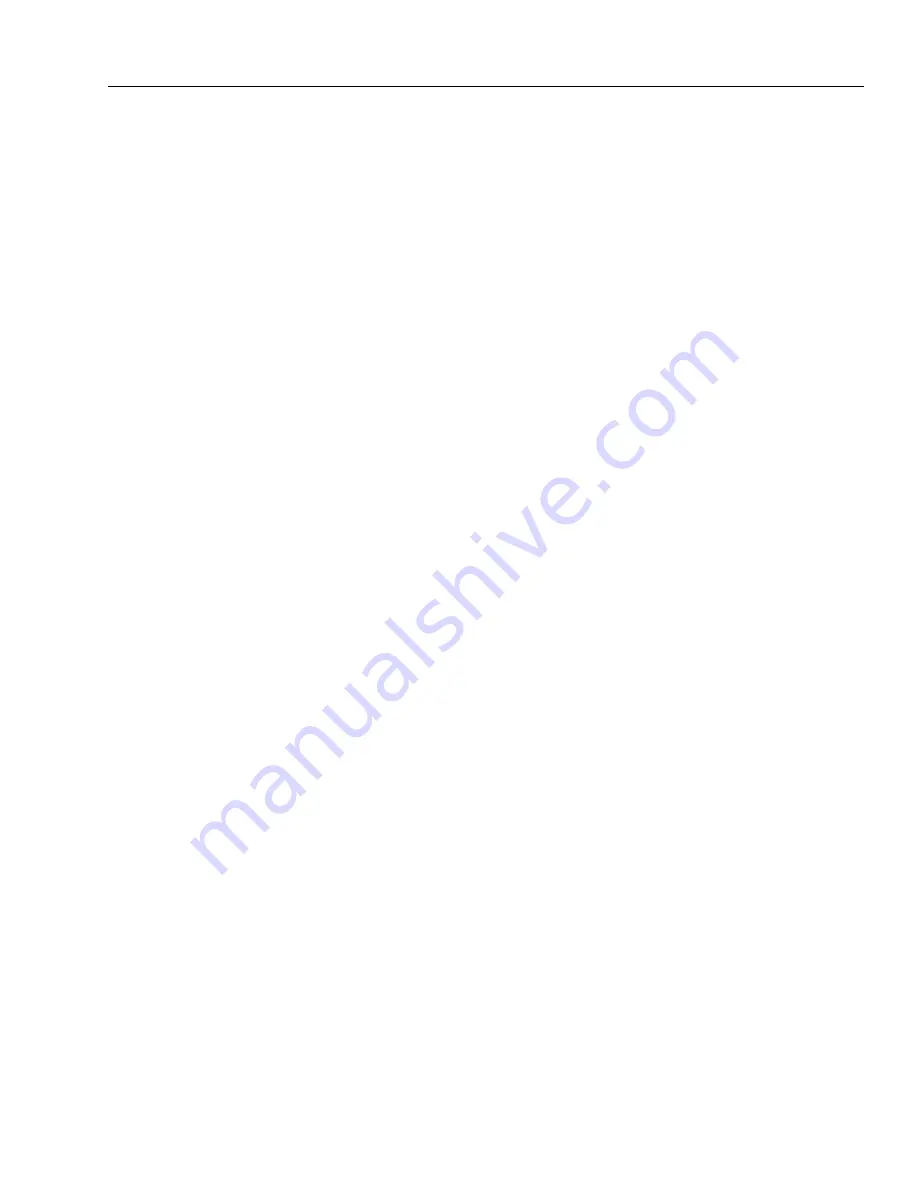
SECTION 3 - CHASSIS & TURNTABLE
3120895
– JLG Lift –
3-23
Installation
Position 1-off gasket (5) over male pilot on brake housing
(4).
Locate brake shaft (1) and secure brake in position using
2-off 1/2” UNC mounting bolts in the through mounting
(fixing) holes provided.
Connect hydraulic pressure supply to brake pressure inlet
port. Ensure that the hydraulic pressure is set to the
required level up to a maximum of 3000 psi (200 bar) and
check that the brake disengages and re-engages cor-
rectly.
Maintenance
The brake is required to be kept in good working order
and must be included in the planned maintenance pro-
gram for the equipment to which the brake is installed.
This must include torque testing together with inspection
and replacement of the working parts such as friction
plates (3 & 6) and, springs (22 & 23). The frequency of
inspection depends on the duty demanded of the brake.
Disassembly
To remove brake from its installed position, reverse proce-
dure previously described in the installation instructions.
Place the complete brake assembly on a clean, dry work
bench.
Remove external gasket (5) as necessary.
NOTE:
Refer to Diagrams for the following.
1.
Supporting brake face “A”, remove the six socket head
cap screws and washers (items 13 & 14) in equal
increments to ensure the spring pressure within the
brake is reduced gradually and evenly.
Alternatively, if press is available, the cylinder hous-
ing (8) can be restrained on face “B” while removing
the six socket head cap screws and washers (13 &
14).
The brake assembly can now be fully dismantled
and parts examined.
2.
Remove cylinder housing (8) and piston (9) subassem-
bly and dismantle if required, removing O-ring seals
(15 & 17) and backing rings (16 & 18) as necessary.
3.
Remove gasket (7) from housing (2).
4.
Remove friction plates (3 & 6) and pressure plate (4).
5.
Remove 2-off dowel pins (19).
6.
Remove springs (22 & 23).
7.
Should it be necessary to replace ball bearing (10) or
shaft seal (12), reverse remainder of brake sub-
assembly, supporting on face “c” of housing (2).
8.
Remove internal retaining ring (11).
9.
Using arbor press or similar to break Loctite seal,
remove brake shaft (1) from housing (2) and lay
aside.
10.
Reverse housing (2) and press out ball bearing (10).
Shaft seal (12) can also be removed if necessary.
Examination
All components can now be examined and inspected,
paying particular attention to the following.
1.
Inspect friction plates (3 & 6) and friction surface on
pressure plate (4) for wear or damage.
2.
Examine friction plates (3) and brake shaft (1) for wear
or damage to splines.
3.
Examine input and output splines of brake shaft (1) for
wear or damage.
4.
Examine compression springs (22 & 23) for damage or
fatigue.
5.
Check ball bearing (10) for axial float or wear.
6.
Examine O-ring seals (15 & 17) and backing rings (16
& 18) for damage.
7.
Obtain replacement parts as required.
Assembly
Clean all parts thoroughly.
Reverse procedure previously outlined in Dismantling
instructions taking particular care with.
a.
Assembly of shaft seal (12).
b.
Assembly of bearing (10).
c.
Quantity and orientation of springs (22 & 23).
d.
Assembly sequence of friction plates (3 & 6).
1.
Lightly lubricate rotary shaft seal (12) and assemble to
housing (2) taking care not to damage seal lip.
2.
Apply ring of Loctite 641 or equivalent adhesive to full
circumference of housing (2) bearing recess adja-
cent to shoulder.
Apply complete coverage of Loctite 641 to outside
diameter of bearing (10) and assemble fully in hous-
ing (2), retaining with internal retaining ring (11).
Remove excess adhesive with clean cloth.
Press shaft (1) through bearing (10), ensuring bear-
ing inner ring is adequately supported.
3.
Assemble correct quantity of springs (22 & 23) in orien-
tation required.
4.
Lubricate O-ring seals (15 & 17) with Molykote 55M (or
equivalent) silicone grease and assemble together
with backing rings (16 & 18) to piston (9). To ensure
correct brake operation, it is important that the back-
Summary of Contents for JLG 400S
Page 1: ...Service and Maintenance Manual Models 400S 460SJ P N 3120895 December 6 2012...
Page 2: ......
Page 20: ...xvi JLG Lift 3120895 LIST OF TABLES TABLE NO TITLE PAGE NO This page left blank intentionally...
Page 52: ...SECTION 2 GENERAL 2 14 JLG Lift 3120895 NOTES...
Page 100: ...SECTION 3 CHASSIS TURNTABLE 3 48 JLG Lift 3120895 Figure 3 35 Swing Drive Installation...
Page 101: ...SECTION 3 CHASSIS TURNTABLE 3120895 JLG Lift 3 49 Figure 3 36 Swing Motor...
Page 105: ...SECTION 3 CHASSIS TURNTABLE 3120895 JLG Lift 3 53 Figure 3 38 Swing Brake S N 64802 to Present...
Page 107: ...SECTION 3 CHASSIS TURNTABLE 3120895 JLG Lift 3 55 Figure 3 39 Swing Torque Hub...
Page 124: ...SECTION 3 CHASSIS TURNTABLE 3 72 JLG Lift 3120895 Figure 3 44 EFI Component Location...
Page 136: ...SECTION 3 CHASSIS TURNTABLE 3 84 JLG Lift 3120895 Figure 3 49 Valve Location Chassis...
Page 137: ...SECTION 3 CHASSIS TURNTABLE 3120895 JLG Lift 3 85 Figure 3 50 Hyd Tank Installation...
Page 143: ...SECTION 3 CHASSIS TURNTABLE 3120895 JLG Lift 3 91 This page left blank intentionally...
Page 155: ...SECTION 3 CHASSIS TURNTABLE 3120895 JLG Lift 3 103 Figure 3 60 EMR2 Fault Codes Sheet 1 of 5...
Page 156: ...SECTION 3 CHASSIS TURNTABLE 3 104 JLG Lift 3120895 Figure 3 61 EMR2 Fault Codes Sheet 2 of 5...
Page 157: ...SECTION 3 CHASSIS TURNTABLE 3120895 JLG Lift 3 105 Figure 3 62 EMR2 Fault Codes Sheet 3 of 5...
Page 158: ...SECTION 3 CHASSIS TURNTABLE 3 106 JLG Lift 3120895 Figure 3 63 EMR2 Fault Codes Sheet 4 of 5...
Page 159: ...SECTION 3 CHASSIS TURNTABLE 3120895 JLG Lift 3 107 Figure 3 64 EMR2 Fault Codes Sheet 5 of 5...
Page 208: ...SECTION 3 CHASSIS TURNTABLE 3 156 JLG Lift 3120895...
Page 210: ...SECTION 3 CHASSIS TURNTABLE 3 158 JLG Lift 3120895...
Page 213: ...SECTION 3 CHASSIS TURNTABLE 3120895 JLG Lift 3 161...
Page 223: ...SECTION 3 CHASSIS TURNTABLE 3120895 JLG Lift 3 171 Sensor Transducer Type...
Page 227: ...SECTION 3 CHASSIS TURNTABLE 3120895 JLG Lift 3 175 Sensor Transducer Type...
Page 229: ...SECTION 3 CHASSIS TURNTABLE 3120895 JLG Lift 3 177...
Page 231: ...SECTION 3 CHASSIS TURNTABLE 3120895 JLG Lift 3 179...
Page 233: ...SECTION 3 CHASSIS TURNTABLE 3120895 JLG Lift 3 181...
Page 235: ...SECTION 3 CHASSIS TURNTABLE 3120895 JLG Lift 3 183...
Page 237: ...SECTION 3 CHASSIS TURNTABLE 3120895 JLG Lift 3 185...
Page 255: ...SECTION 3 CHASSIS TURNTABLE 3120895 JLG Lift 3 203...
Page 259: ...SECTION 3 CHASSIS TURNTABLE 3120895 JLG Lift 3 207...
Page 264: ...SECTION 3 CHASSIS TURNTABLE 3 212 JLG Lift 3120895 NOTES...
Page 288: ...SECTION 4 BOOM PLATFORM 4 24 JLG Lift 3120895 Figure 4 12 Rotator Counterbalance Valve...
Page 303: ...SECTION 5 HYDRAULICS 3120895 JLG Lift 5 15 Figure 5 22 Main Valve...
Page 313: ...SECTION 5 HYDRAULICS 3120895 JLG Lift 5 25 Figure 5 25 Variable Displacement Hydraulic Pump...
Page 402: ...SECTION 6 JLG CONTROL SYSTEM S N 61718 TO PRESENT 6 86 JLG Lift 3120895 NOTES...
Page 460: ...SECTION 7 BASIC ELECTRICAL INFORMATION SCHEMATICS 7 58 JLG Lift 3120895 NOTES...
Page 461: ......