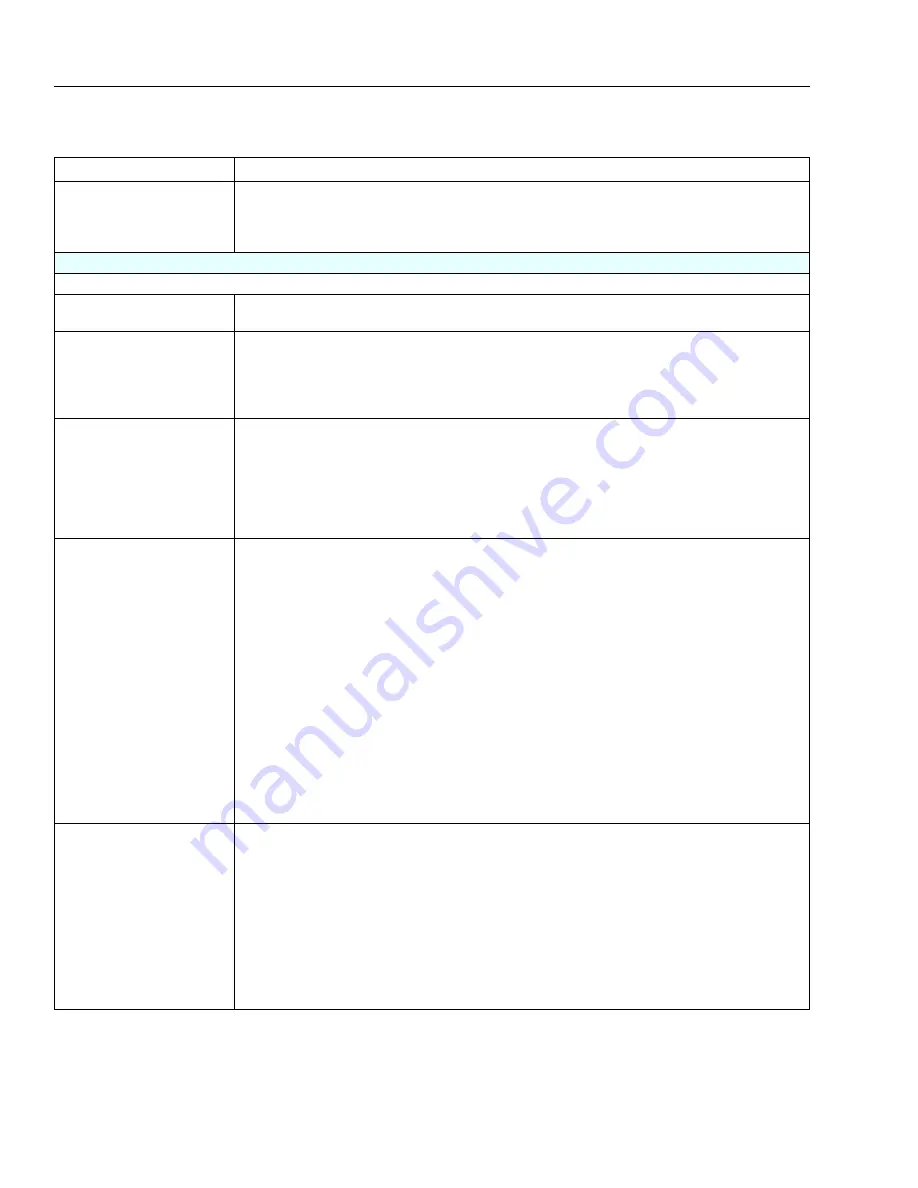
SECTION 3 - CHASSIS & TURNTABLE
3-128
– JLG Lift –
3120895
Exhaust System Checks
Check the exhaust system for a possible restriction:
- Inspect the exhaust system for damaged or collapsed pipes
- Inspect the muffler for signs of heat distress or for possible internal failure.
Check for possible plugged catalytic converter. Refer to Restricted Exhaust System Diagnosis
Hard Start
DEFINITION: The engine cranks OK, but does not start for a long time. The engine does eventually run, or may start but immediately dies.
Preliminary Checks
Refer to Important Preliminary Checks.
Make sure the vehicle's operator is using the correct starting procedure.
Sensor Checks
Check the Engine Coolant Temperature sensor with the scan tool. Compare the engine coolant temperature with the
ambient air temperature on a cold engine. IF the coolant temperature reading is more than 5 degrees greater or less than
the ambient air temperature on a cold engine, check for high resistance in the coolant sensor circuit. Refer to DTC 111
Check the Crankshaft Position (CKP) sensor.
Check the Throttle position (TPS) sensor.
Fuel System Checks
Important: A closed LPG manual fuel shut off valve will create an extended crank OR no start condition.
Verify the excess flow valve in the LPG manual shut-off valve is not tripped.
Check mixer module assembly for proper installation and leakage.
Verify proper operation of the low pressure lock-off solenoids.
Verify proper operation of the EPR
Check for air intake system leakage between the mixer and the throttle body.
Check the fuel system pressures. Refer to the Fuel System Diagnosis.
Ignition System Checks
Note: LPG being a gaseous fuel requires higher secondary ignition system voltages for the equivalent gasoline operat-
ing conditions.
Check for the proper ignition voltage output with J 26792 or the equivalent.
Verify that the spark plugs are correct for use with LPG (R42LTS)
Check the spark plugs for the following conditions:
- Wet plugs
- Cracks
- Wear
- Improper gap
- Burned electrodes
- Heavy deposits
Check for bare or shorted ignition wires.
Check for moisture in the distributor cap if applicable.
Check for loose ignition coil connections.
Important:
1. If the engine starts but then immediately stalls, Check the Crankshaft Position (CKP).
2. Check for improper gap, debris or faulty connections.
Engine Mechanical Checks
Important: The LPG Fuel system works on a fumigation principle of fuel introduction and is more sensitive to intake man-
ifold leakage than the gasoline fuel supply system.
Check for the following:
- Vacuum leaks
- Improper valve timing
- Low compression
- Bent pushrods
- Worn rocker arms
- Broken or weak valve springs
- Worn camshaft lobes.
Check the intake and exhaust manifolds for casting flash.
Table 3-12. Symptom Diagnosis
Checks
Action
Summary of Contents for JLG 400S
Page 1: ...Service and Maintenance Manual Models 400S 460SJ P N 3120895 December 6 2012...
Page 2: ......
Page 20: ...xvi JLG Lift 3120895 LIST OF TABLES TABLE NO TITLE PAGE NO This page left blank intentionally...
Page 52: ...SECTION 2 GENERAL 2 14 JLG Lift 3120895 NOTES...
Page 100: ...SECTION 3 CHASSIS TURNTABLE 3 48 JLG Lift 3120895 Figure 3 35 Swing Drive Installation...
Page 101: ...SECTION 3 CHASSIS TURNTABLE 3120895 JLG Lift 3 49 Figure 3 36 Swing Motor...
Page 105: ...SECTION 3 CHASSIS TURNTABLE 3120895 JLG Lift 3 53 Figure 3 38 Swing Brake S N 64802 to Present...
Page 107: ...SECTION 3 CHASSIS TURNTABLE 3120895 JLG Lift 3 55 Figure 3 39 Swing Torque Hub...
Page 124: ...SECTION 3 CHASSIS TURNTABLE 3 72 JLG Lift 3120895 Figure 3 44 EFI Component Location...
Page 136: ...SECTION 3 CHASSIS TURNTABLE 3 84 JLG Lift 3120895 Figure 3 49 Valve Location Chassis...
Page 137: ...SECTION 3 CHASSIS TURNTABLE 3120895 JLG Lift 3 85 Figure 3 50 Hyd Tank Installation...
Page 143: ...SECTION 3 CHASSIS TURNTABLE 3120895 JLG Lift 3 91 This page left blank intentionally...
Page 155: ...SECTION 3 CHASSIS TURNTABLE 3120895 JLG Lift 3 103 Figure 3 60 EMR2 Fault Codes Sheet 1 of 5...
Page 156: ...SECTION 3 CHASSIS TURNTABLE 3 104 JLG Lift 3120895 Figure 3 61 EMR2 Fault Codes Sheet 2 of 5...
Page 157: ...SECTION 3 CHASSIS TURNTABLE 3120895 JLG Lift 3 105 Figure 3 62 EMR2 Fault Codes Sheet 3 of 5...
Page 158: ...SECTION 3 CHASSIS TURNTABLE 3 106 JLG Lift 3120895 Figure 3 63 EMR2 Fault Codes Sheet 4 of 5...
Page 159: ...SECTION 3 CHASSIS TURNTABLE 3120895 JLG Lift 3 107 Figure 3 64 EMR2 Fault Codes Sheet 5 of 5...
Page 208: ...SECTION 3 CHASSIS TURNTABLE 3 156 JLG Lift 3120895...
Page 210: ...SECTION 3 CHASSIS TURNTABLE 3 158 JLG Lift 3120895...
Page 213: ...SECTION 3 CHASSIS TURNTABLE 3120895 JLG Lift 3 161...
Page 223: ...SECTION 3 CHASSIS TURNTABLE 3120895 JLG Lift 3 171 Sensor Transducer Type...
Page 227: ...SECTION 3 CHASSIS TURNTABLE 3120895 JLG Lift 3 175 Sensor Transducer Type...
Page 229: ...SECTION 3 CHASSIS TURNTABLE 3120895 JLG Lift 3 177...
Page 231: ...SECTION 3 CHASSIS TURNTABLE 3120895 JLG Lift 3 179...
Page 233: ...SECTION 3 CHASSIS TURNTABLE 3120895 JLG Lift 3 181...
Page 235: ...SECTION 3 CHASSIS TURNTABLE 3120895 JLG Lift 3 183...
Page 237: ...SECTION 3 CHASSIS TURNTABLE 3120895 JLG Lift 3 185...
Page 255: ...SECTION 3 CHASSIS TURNTABLE 3120895 JLG Lift 3 203...
Page 259: ...SECTION 3 CHASSIS TURNTABLE 3120895 JLG Lift 3 207...
Page 264: ...SECTION 3 CHASSIS TURNTABLE 3 212 JLG Lift 3120895 NOTES...
Page 288: ...SECTION 4 BOOM PLATFORM 4 24 JLG Lift 3120895 Figure 4 12 Rotator Counterbalance Valve...
Page 303: ...SECTION 5 HYDRAULICS 3120895 JLG Lift 5 15 Figure 5 22 Main Valve...
Page 313: ...SECTION 5 HYDRAULICS 3120895 JLG Lift 5 25 Figure 5 25 Variable Displacement Hydraulic Pump...
Page 402: ...SECTION 6 JLG CONTROL SYSTEM S N 61718 TO PRESENT 6 86 JLG Lift 3120895 NOTES...
Page 460: ...SECTION 7 BASIC ELECTRICAL INFORMATION SCHEMATICS 7 58 JLG Lift 3120895 NOTES...
Page 461: ......