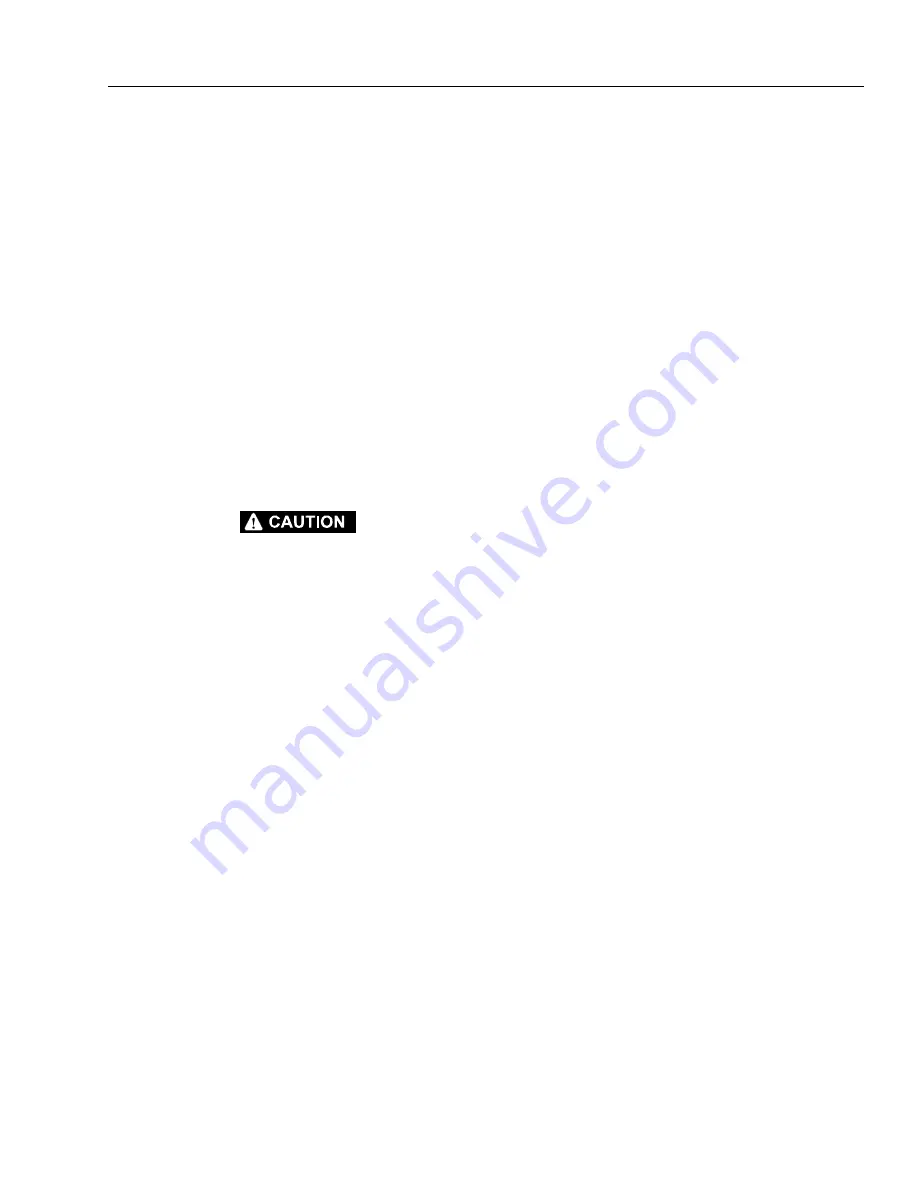
SECTION 5 - HYDRAULICS
3120895
– JLG Lift –
5-17
Relief Valves
Relief valves are installed at various points within the
hydraulic system to protect associated systems and com-
ponents against excessive pressure. Excessive pressure
can be developed when a cylinder reaches its limit of
travel and the flow of pressurized fluid continues from the
system control. The relief valve provides an alternate path
for the continuing flow from the pump, thus preventing
rupture of the cylinder, hydraulic line or fitting. Complete
failure of the system pump is also avoided by relieving cir-
cuit pressure. The relief valve is installed in the circuit
between the pump outlet (pressure line) and the cylinder
of the circuit, generally as an integral part of the system
valve bank. Relief pressures are set slightly higher than
the load requirement, with the valve diverting excess
pump delivery back to the reservoir when operating pres-
sure of the component is reached.
1.
Remove the boom from the turntable as follows:
a.
Disconnect wiring harness from ground control
harness connector.
HYDRAULIC LINES AND PORTS SHOULD BE CAPPED IMMEDI-
ATELY AFTER DISCONNECTING LINES TO AVOID ENTRY OF CON-
TAMINANTS INTO SYSTEM.
b.
Tag and disconnect hydraulic lines from boom
to control valve. Use a suitable container to
retain any residual hydraulic fluid. Cap all
hydraulic lines and ports.
c.
Using a suitable lifting equipment, adequately
support boom weight along entire length.
d.
Remove the bolts and keeper pins securing the
lift cylinder pivot pin. Using a suitable brass drift
and hammer, remove the pivot pin from the
lower boom.
e.
Remove hardware securing the level link pivot
pin. Using a suitable brass drift and hammer,
remove the pin from the level link and turntable.
f.
Remove hardware securing the boom pivot pin.
Using a suitable brass drift and hammer, remove
pin from the turntable.
Using all applicable safety precautions, carefully lift boom
assembly clear of turntable and lower to ground or suit-
able supported work surface.
5.4 PRESSURE SETTING PROCEDURES
Cold temperatures have a significant impact on pressure
readings.JLG Industries Inc. recommends operating the
machine until hydraulic system has warmed to normal
operating temperatures prior to checking pressures. We
also recommend using a calibrated gauge. Pressure read-
ings are acceptable if /- 5% of specified pres-
sures.
NOTE:
Engine RPM’s must be correct. Mid engine 1800,
and High engine 2800 for Deutz engines; 2900 for
Ford engines. The adjustable resistor at the ground
control for lift and swing should be set to maximum
speed for these functions while setting pressures.
After this procedure is done, it can be reset.
1. Bang-Bang Main Relief Valve;
This valve will be reset at the end of this procedure. In
order to be able to set other pressures, we need to set this
valve to 3000 psi. Install a high pressure gauge at the port
marked “M1” located behind the tank port. Activate tele-
scope in. Adjust the valve to 3000 psi, located on top of
main valve, 3
rd
relief valve to the left of the tank port. Turn
clockwise to increase and counterclockwise to decrease.
2. Steer;
Install a high pressure gauge at the port marked “M5”.
Activate steer and adjust the relief valve to 2500 psi. The
relief valve is located on the top of the main valve, the 5
th.
relief valve down from the tank port. Turn clockwise to
increase and counterclockwise to decrease.
3. Platform Level Up;
Install a high pressure gauge at the port marked “M3,
located on the front face of the block at the top right cor-
ner. There is pressure trapped at this test port. To release
this pressure, activate level down to the end of stroke. (the
pressure in the up side goes to 0) This will allow you to
snap a gauge on this port. Activate level up to the end of
stroke, you should read 2800 psi. The level up relief valve
is located on the top of the main valve and is the 1
st.
relief
valve to the left of the tank port. Turn clockwise to
increase, and counterclockwise to decrease.
4. Platform Level Down;
Install a high pressure gauge at the port marked “M4,
located at the front face, bottom right corner. To get a
gauge on this point, activate level up to the end of stroke,
(the pressure in the down side goes to 0)allowing you to
snap on a gauge. Activate level down to the end of stroke,
you should read 1800 psi. The level down relief valve is
located on the top of the main valve and is the 2
nd.
relief
valve to the left of the tank port. Turn clockwise to
increase, and counterclockwise to decrease.
5. Articulating Jib Up;
Install a high pressure gauge on “M” port of jib block,
located on the left side of the main valve. Activate jib up,
reading should be 2500 psi. The up relief valve is the front
Summary of Contents for JLG 400S
Page 1: ...Service and Maintenance Manual Models 400S 460SJ P N 3120895 December 6 2012...
Page 2: ......
Page 20: ...xvi JLG Lift 3120895 LIST OF TABLES TABLE NO TITLE PAGE NO This page left blank intentionally...
Page 52: ...SECTION 2 GENERAL 2 14 JLG Lift 3120895 NOTES...
Page 100: ...SECTION 3 CHASSIS TURNTABLE 3 48 JLG Lift 3120895 Figure 3 35 Swing Drive Installation...
Page 101: ...SECTION 3 CHASSIS TURNTABLE 3120895 JLG Lift 3 49 Figure 3 36 Swing Motor...
Page 105: ...SECTION 3 CHASSIS TURNTABLE 3120895 JLG Lift 3 53 Figure 3 38 Swing Brake S N 64802 to Present...
Page 107: ...SECTION 3 CHASSIS TURNTABLE 3120895 JLG Lift 3 55 Figure 3 39 Swing Torque Hub...
Page 124: ...SECTION 3 CHASSIS TURNTABLE 3 72 JLG Lift 3120895 Figure 3 44 EFI Component Location...
Page 136: ...SECTION 3 CHASSIS TURNTABLE 3 84 JLG Lift 3120895 Figure 3 49 Valve Location Chassis...
Page 137: ...SECTION 3 CHASSIS TURNTABLE 3120895 JLG Lift 3 85 Figure 3 50 Hyd Tank Installation...
Page 143: ...SECTION 3 CHASSIS TURNTABLE 3120895 JLG Lift 3 91 This page left blank intentionally...
Page 155: ...SECTION 3 CHASSIS TURNTABLE 3120895 JLG Lift 3 103 Figure 3 60 EMR2 Fault Codes Sheet 1 of 5...
Page 156: ...SECTION 3 CHASSIS TURNTABLE 3 104 JLG Lift 3120895 Figure 3 61 EMR2 Fault Codes Sheet 2 of 5...
Page 157: ...SECTION 3 CHASSIS TURNTABLE 3120895 JLG Lift 3 105 Figure 3 62 EMR2 Fault Codes Sheet 3 of 5...
Page 158: ...SECTION 3 CHASSIS TURNTABLE 3 106 JLG Lift 3120895 Figure 3 63 EMR2 Fault Codes Sheet 4 of 5...
Page 159: ...SECTION 3 CHASSIS TURNTABLE 3120895 JLG Lift 3 107 Figure 3 64 EMR2 Fault Codes Sheet 5 of 5...
Page 208: ...SECTION 3 CHASSIS TURNTABLE 3 156 JLG Lift 3120895...
Page 210: ...SECTION 3 CHASSIS TURNTABLE 3 158 JLG Lift 3120895...
Page 213: ...SECTION 3 CHASSIS TURNTABLE 3120895 JLG Lift 3 161...
Page 223: ...SECTION 3 CHASSIS TURNTABLE 3120895 JLG Lift 3 171 Sensor Transducer Type...
Page 227: ...SECTION 3 CHASSIS TURNTABLE 3120895 JLG Lift 3 175 Sensor Transducer Type...
Page 229: ...SECTION 3 CHASSIS TURNTABLE 3120895 JLG Lift 3 177...
Page 231: ...SECTION 3 CHASSIS TURNTABLE 3120895 JLG Lift 3 179...
Page 233: ...SECTION 3 CHASSIS TURNTABLE 3120895 JLG Lift 3 181...
Page 235: ...SECTION 3 CHASSIS TURNTABLE 3120895 JLG Lift 3 183...
Page 237: ...SECTION 3 CHASSIS TURNTABLE 3120895 JLG Lift 3 185...
Page 255: ...SECTION 3 CHASSIS TURNTABLE 3120895 JLG Lift 3 203...
Page 259: ...SECTION 3 CHASSIS TURNTABLE 3120895 JLG Lift 3 207...
Page 264: ...SECTION 3 CHASSIS TURNTABLE 3 212 JLG Lift 3120895 NOTES...
Page 288: ...SECTION 4 BOOM PLATFORM 4 24 JLG Lift 3120895 Figure 4 12 Rotator Counterbalance Valve...
Page 303: ...SECTION 5 HYDRAULICS 3120895 JLG Lift 5 15 Figure 5 22 Main Valve...
Page 313: ...SECTION 5 HYDRAULICS 3120895 JLG Lift 5 25 Figure 5 25 Variable Displacement Hydraulic Pump...
Page 402: ...SECTION 6 JLG CONTROL SYSTEM S N 61718 TO PRESENT 6 86 JLG Lift 3120895 NOTES...
Page 460: ...SECTION 7 BASIC ELECTRICAL INFORMATION SCHEMATICS 7 58 JLG Lift 3120895 NOTES...
Page 461: ......