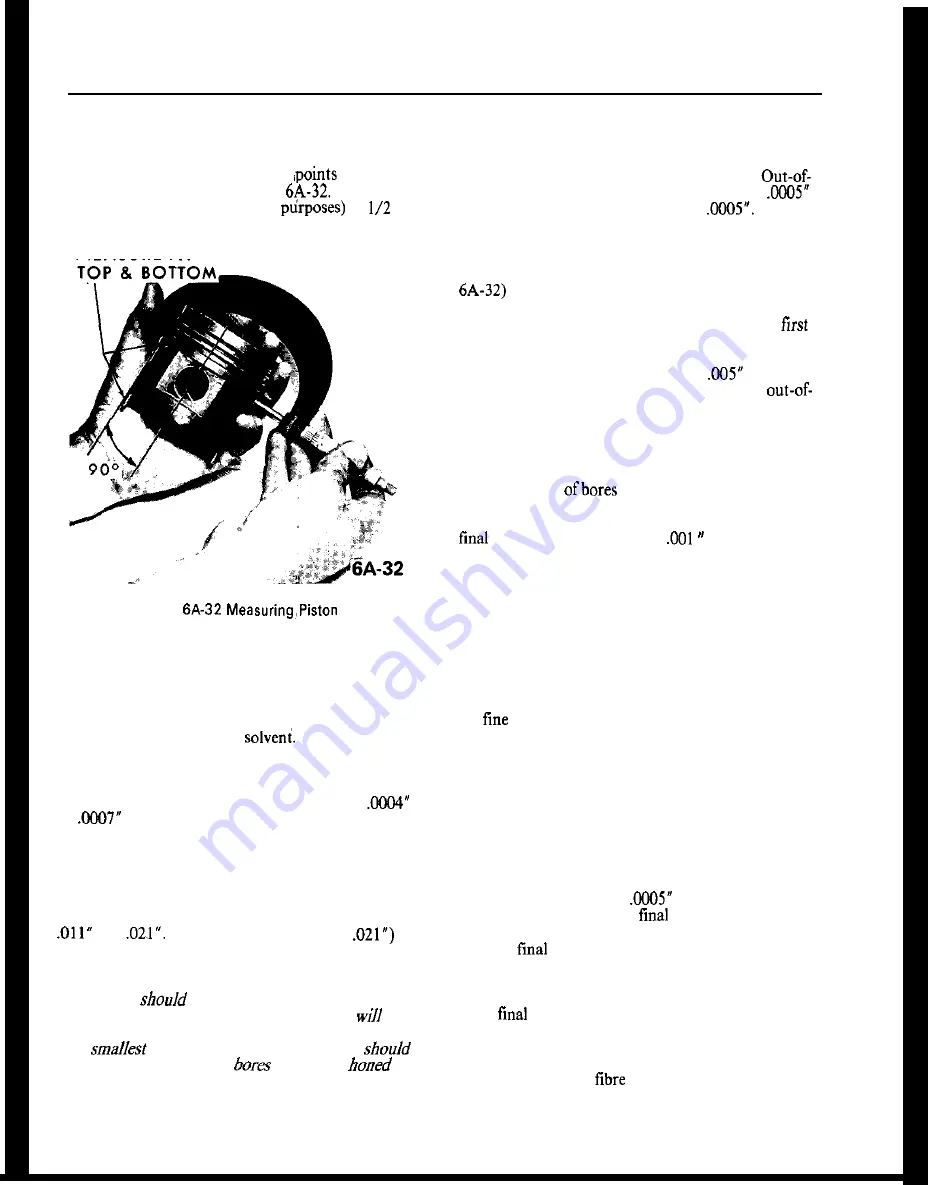
6A. 20
1973 OPEL SERVICE MANUAL
diameter at the right angle to the piston pin is greater
than the diameter parallel to the piston pin. When a
piston is checked for size, it must be measured with
micrometers applied to the skirt at
90 degrees
to the piston pin. See Figure
The piston
should be measured (for fitting
2
in-
ches below the top of piston.
MEASURE AT
Figure
Inspect bearing surfaces of piston pins. Check for
wear by measuring worn and unworn surfaces with
micrometers. Rough or worn pins should be re-
placed. Check fit of piston pins in piston
bosses.
Occasionally pins will be found tight due to gum or
varnish deposits. This may be corrected by removing
the deposit with a suitable
If piston bosses
are worn out-of-round or oversize, the piston and pin
assembly must be replaced. Oversize pins are not
practical because the pin is a press fit
in
the
connect-
ing rod. Piston pins must tit the piston with
to
clearance.
Examine all piston rings for scores, chips or cracks.
Check compression rings for tension by comparing
with new rings. Check gap of compression rings by
placing rings in bore at bottom of ring travel. Meas-
ure gap with feeler gage. Gap should be between
and
If gaps are excessive (over
it
indicates the rings have worn considerably and
should
b e
replaced.
No attempt
be made to cut down oversize
pistons to fit cylinder bores. This practice
de-
stroy the surface treatment and affect the weight.
The
possible oversize service pistons
be used and the cylinder
should be
to
size for proper clearance.
1. Before installing piston, piston rings, or reboring
cylinders, observe the following:
Cylinder bores may not be the same size. Standard
replacement piston sizes are in the midpoint of the
cylinder bore size range. Therefore, it may be neces-
sary to hone cylinders for correct piston tit.
round on cylinder bore must not exceed
maximum with a taper of not over
Before the honing or reboring operation is started,
measure all new pistons with micrometer contacting
at points exactly 90 degrees to piston pin (Figure
then select the smallest piston for the first
fitting. The slight variation usually found between
pistons in
a set
may provide for correction if the
piston has excessive clearance.
If wear of cylinder does not exceed
honing is
recommended for truing the bore. If wear or
round exceeds these limits, the bore should be trued
up with a fly cutter boring
bar
and then finish honed.
When reboring cylinders, all crankshaft bearing caps
must be in place and tightened to proper torque to
avoid distortion
in final assembly. Always be
certain the crankshaft is out of the way of the boring
cutter when boring each cylinder. When making the
cut with boring bar, leave
on the diameter
for finish honing to give the required clearance speci-
fied.
When honing cylinders, use clean sharp stones of
proper grade for the required amount of metal to be
removed, in accordance with instructions of the hone
manufacturer. Dull or dirty stones cut unevenly and
generate excessive heat. When using coarse or
medium grade stones use care to leave sufficient
metal so that all stone marks may be removed with
the
stones used for finishing in order to maintain
proper clearance.
When finish honing, pass the hone through the entire
length of cylinder at the rate of approximately 60
cycles per minute. This should produce the desired
45 degree cross hatch pattern on cylinder walls
which will insure maximum ring life and minimum
oil consumption.
It is of the greatest importance that refinished cylin-
der bores have not over
out-of-round or ta-
pered. Each bore must be
honed to remove all
stone or cutter marks and provide a smooth surface.
During
honing, each piston must be fitted in-
dividually to the bore in which it will be installed and
should be marked to insure correct installation.
After
honing and before the piston is checked
for fit, each cylinder bore must be
thoroughly
washed to remove all traces of abrasive and then
dried. The dry bore should then be brushed clean
with a power-driven
brush. If all traces of abra-
sive are not removed, rapid wear of new pistons and
rings will result. Fit new pistons in the following
manner:
Summary of Contents for 1900 1973
Page 1: ......
Page 7: ......
Page 9: ......
Page 48: ...IGNITION SYSTEM lC 27 9 3OlC19 Figure 1 C l 3 Distributor Exploded...
Page 57: ...I I 1 D 36 1973 OPEL SERVICE MANUAL I Figure 1 D 27 Alternator Exploded View 301D27...
Page 95: ...j 1J 74 1973 OPEL SERVICE MANUAL i I m Figure 13 1 Windshield Wiper and Horn Opel 1900 Manta...
Page 96: ...I I WIRING DIAGRAMS lJ 75 Figure lJ 2 Windshield Wiper and Horn Rallye...
Page 97: ...1 J 76 1973 OPEL SERVICE IMANUAL L J Figure lJ 3 Wind hield Wiper and Horn Gl...
Page 98: ...I I I WIRING DIAGRAMS 1J 77 I I Figure 1 J 4 Turn Signal and Hazard Flasher Opel 1900 Manta I...
Page 99: ...I i L I lJ 78 1873 OPEL SERVICE MANUAL Figure lJ 5 Turn Signal and Hazard Flasher GT...
Page 100: ...I WIRING DIAGRAMS 15 79 I I Figure lJ 6 Oil Fuel Temp Tach Stop and Brake Warning Light GT I...
Page 101: ......
Page 102: ...I WIRING DIAGRAMS lJ 81 r Figure 1 J 8 Blower and Lighter GT...
Page 103: ...I I lJ 82 1973 OPEL SERVICE MANUAL Figure lJ 9 indicator Lights and Gauges Opel 1900 Manta...
Page 104: ...I I WIRING DIAGRAMS IJ 83 I Figure 1 J 10 Indicator Lights and Gauges Ratlye...
Page 106: ...EhMB SWITCH R GHiDOOR 301J12...
Page 107: ...1 J 86 1973 OPEL SERVICE MANUAL i Figure 1 J l 3 Headlamps Opel 1900...
Page 108: ...I I I WIRING DIAGRAMS lJ 87 Figure lJ 14 Headlamps Manta...
Page 109: ...1 J 88 1973 OPEL SERVICE MANUAL I 1 Figure lJ 15 Headlamp and Fog Lights Rallye...
Page 110: ...301516...
Page 111: ......
Page 113: ...1 J 92 1973 OPEL SERVICE MANUAL d 5 Figure 1 19 Starting lgniiion and Charging Opel 1900 Manta...
Page 114: ...I I WIRING DIAGRAMS lJ 93 I Figure lJ 20 Starting Ignition and Charging GT...
Page 115: ...1 J 94 1973 OPEL SERVICE MANUAL i I I Figure lJ 21 Instrument Panel GT...
Page 116: ...I I 1 I WIRING DIAGRAMS lJ 95 Figure lJ 22 A C Generator and Regulator All Models...
Page 117: ...301523...
Page 119: ...I I I 10 RED AMP GAGE 301J25...
Page 120: ...WIRING DIAGRAMS lJ 99 Figure lJ 26 Seat Belt Warning System Automatic Transmissionl GT...
Page 121: ...lJ 100 1973 OPEL SERVICES MANUAL I Figure 1 J 27 Heated Rear Glass Opel 1900 Manta...
Page 122: ...I WIRING DIAGRAMS 1 J 101...
Page 123: ...1 J 102 1973 OPEL 9ER IC MANUAL...
Page 128: ...SPECIAL BODY TOOLS GENERAL INFORMATION 2A 5 W REGULATOR INING INSTALLER J 21828 J 21549 2A 1...
Page 167: ......
Page 231: ......
Page 259: ......
Page 285: ...5C 26 1973 OPEL SERVICE MANUAL...
Page 322: ...ENGINE MECHANICAL AND MOUNTS 6A 31...
Page 350: ...CARBURETOR AND THROTTLE LINKAGE 6E 59 Figure 6E 37 Carburetor Specifications...
Page 361: ......
Page 372: ...Figure 7A 9 Exploded View of Clutch Pedal and Housing...
Page 423: ...Third Clutch Applied Low Band Released...
Page 424: ...AUTOMATIC TRANSMISSION C 63...
Page 425: ...712 64 1973 OPEL SERVICE MANUAL HYDRAULIC OPERATION I r n...
Page 427: ...7C 66 1973 OPEL SERVICE MANUAL...
Page 428: ......
Page 429: ...7C 68 1973 OPEL SERVICE MANUAL II II I...
Page 431: ...7C 70 1973 OPEL SERVICE MANUAL d...
Page 433: ...7C 72 1973 OPEL SERVICE MANUAL...
Page 435: ...7C 74 1973 OPEL SERVICE MANUAL...
Page 437: ...712 76 1973 OPEL SERVICE MANUAL...
Page 439: ...a 1973 OPEL SERVICE MANUAL...
Page 441: ...7C 80 1973 OPEL SERVICE MANUAL...
Page 499: ...7C 138 1973 OPEL SERVICE MANUAL 4 5 I Figure 7C 234 Special Tools Automatic Transmission 7C223...
Page 509: ......
Page 596: ...98 88 1973 OPEL SERVICE MANUAL Figure gB 165 Special Tools...
Page 620: ......