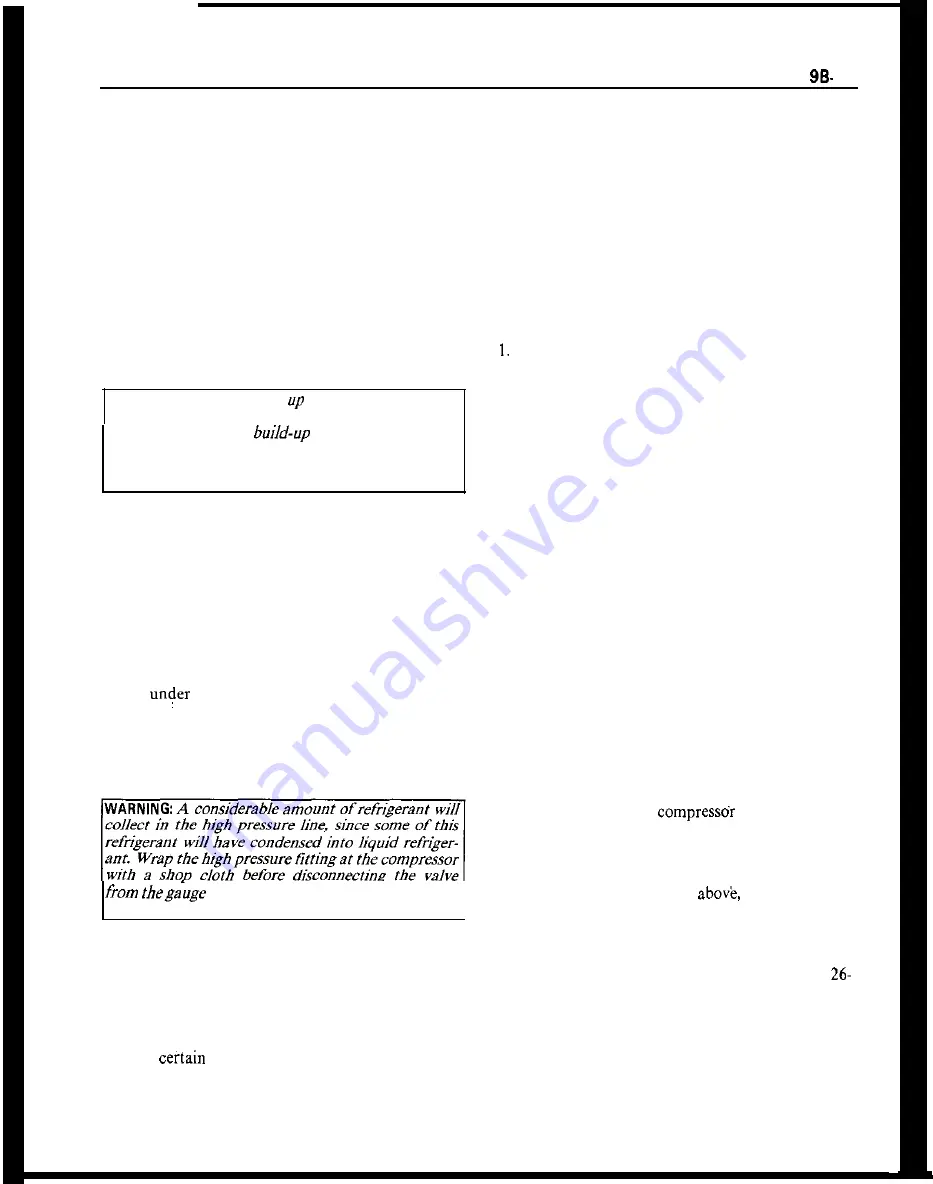
REFRIGERANT COMPONENTS ALL MODELS
45
B.
If system is charged using J-6272-02, close the
valve of opener after all cans are empty. Release the
locking lever and discard the three (3) empty cans.
If this tool will be used to complete the charge with
additional cans to provide the required refrigerant
charge, leave the empty cans in position, locate one
full can and lock the lever into place. These empty
cans balance the assembly and prevent the loss of
refrigerant through the open “series” passage. Align
the pierced hole in the empty can with the punch in
the cover of the tool.
If the J-6271 valve for single cans is available, com-
plete charging as explained in 4a above.
5. Close high side valve on manifold gauge set,
WARNING:
Prior to starting
engine, the high side
valve on the charging manifold must be closed due
to excessive pressure
which can result in
bursting of the container(s) causing serious injury. If
you are inexperienced in the use of this procedure,
seek professional assistance.
6. Operate engine at 2000 RPM with temperature
control knob at full cold position and blower speed
on Max Hi. If air inlet temperature at the condenser
is below 70 degrees F. when this check is made,
bubbles may appear, even though the proper amount
of refrigerant is in the system. Air inlet temperature
must be 70 degrees F. or above to make an accurate
check.
7. When refrigerant has been installed, continue to
operate system and test for proper operation as ou-
tlined
“Operational Test”.
8. When satisfied that the air conditioning system
is operating properly, stop engine, remove gauge set
and replace protective caps on suction and discharge
fittings.
fitting to prevent damage-or injury to
personnel.
9. Using a leak detector, check complete system for
leaks.
Charging Station Method
INSTALLING J-8393-02
1. Be
compressor hand shut-off valves to
gauge fittings are closed (counterclockwise).
2. Be certain all valves on charging station are
closed.
3. Connect high pressure gauge line to compressor
high pressure gauge fitting.
4. Turn high pressure hand shut-off valve one turn
clockwise, and high pressure control one turn coun-
terclockwise (open). Crack open low pressure con-
trol and allow refrigerant gas to hiss from low
pressure gauge line for three seconds, then connect
low pressure gauge line to low pressure gauge fitting
on compressor adapter fitting. (Place J-9459 adapter
on hose, then attach adapter to gauge fitting.)
FILLING CHARGING CYLINDER
Open Control valve on refrigerant container.
2. Open valve on bottom of charging cylinder, al-
lowing refrigerant to enter cylinder.
3. Bleed charging cylinder to valve (behind control
panel) only as required to allow refrigerant to enter
cylinder. When refrigerant reaches desired charge
level, close valve at bottom of charging cylinder and
be certain cylinder bleed valve is closed securely.
While filling the cylinder, it will be necessary to close
the bleed valve periodically to allow boiling to sub-
side so that refrigerant level in the charging cylinder
can be accurately read.
CHARGING THE SYSTEM USING J-8393-02
1. With charging station connected, as previously
described, remove low pressure gauge line at com-
pressor adapter fitting.
2. Crack open high and low pressure control valves
on station and allow refrigerant gas to purge from
system. Purge slowly enough so, that oil does not
escape from system along with refrigerant.
3. When refrigerant flow nearly stops, connect low
pressure gauge line to
adapter fitting.
4. Turn on vacuum pump and open vacuum control
valve.
5. With system purged as
run pump until
26-28 inches of vacuum is obtained Continue to run
pump for 15 minutes after the system reaches 26-28
inches vacuum.
In all evacuating procedures, the specification of
28 inches of mercury vacuum is used. These figures
are only attainable at or near sea level. For each 1000
feet above sea level where this operation is being
performed, the specifications should be lowered by 1
inch. For example, at 5000 feet elevation, only 21 to
23 inches vacuum can normally be obtained.
6. If 26-28 inches vacuum (corrected to sea level)
cannot be obtained, close vacuum: control valve and
Summary of Contents for 1900 1973
Page 1: ......
Page 7: ......
Page 9: ......
Page 48: ...IGNITION SYSTEM lC 27 9 3OlC19 Figure 1 C l 3 Distributor Exploded...
Page 57: ...I I 1 D 36 1973 OPEL SERVICE MANUAL I Figure 1 D 27 Alternator Exploded View 301D27...
Page 95: ...j 1J 74 1973 OPEL SERVICE MANUAL i I m Figure 13 1 Windshield Wiper and Horn Opel 1900 Manta...
Page 96: ...I I WIRING DIAGRAMS lJ 75 Figure lJ 2 Windshield Wiper and Horn Rallye...
Page 97: ...1 J 76 1973 OPEL SERVICE IMANUAL L J Figure lJ 3 Wind hield Wiper and Horn Gl...
Page 98: ...I I I WIRING DIAGRAMS 1J 77 I I Figure 1 J 4 Turn Signal and Hazard Flasher Opel 1900 Manta I...
Page 99: ...I i L I lJ 78 1873 OPEL SERVICE MANUAL Figure lJ 5 Turn Signal and Hazard Flasher GT...
Page 100: ...I WIRING DIAGRAMS 15 79 I I Figure lJ 6 Oil Fuel Temp Tach Stop and Brake Warning Light GT I...
Page 101: ......
Page 102: ...I WIRING DIAGRAMS lJ 81 r Figure 1 J 8 Blower and Lighter GT...
Page 103: ...I I lJ 82 1973 OPEL SERVICE MANUAL Figure lJ 9 indicator Lights and Gauges Opel 1900 Manta...
Page 104: ...I I WIRING DIAGRAMS IJ 83 I Figure 1 J 10 Indicator Lights and Gauges Ratlye...
Page 106: ...EhMB SWITCH R GHiDOOR 301J12...
Page 107: ...1 J 86 1973 OPEL SERVICE MANUAL i Figure 1 J l 3 Headlamps Opel 1900...
Page 108: ...I I I WIRING DIAGRAMS lJ 87 Figure lJ 14 Headlamps Manta...
Page 109: ...1 J 88 1973 OPEL SERVICE MANUAL I 1 Figure lJ 15 Headlamp and Fog Lights Rallye...
Page 110: ...301516...
Page 111: ......
Page 113: ...1 J 92 1973 OPEL SERVICE MANUAL d 5 Figure 1 19 Starting lgniiion and Charging Opel 1900 Manta...
Page 114: ...I I WIRING DIAGRAMS lJ 93 I Figure lJ 20 Starting Ignition and Charging GT...
Page 115: ...1 J 94 1973 OPEL SERVICE MANUAL i I I Figure lJ 21 Instrument Panel GT...
Page 116: ...I I 1 I WIRING DIAGRAMS lJ 95 Figure lJ 22 A C Generator and Regulator All Models...
Page 117: ...301523...
Page 119: ...I I I 10 RED AMP GAGE 301J25...
Page 120: ...WIRING DIAGRAMS lJ 99 Figure lJ 26 Seat Belt Warning System Automatic Transmissionl GT...
Page 121: ...lJ 100 1973 OPEL SERVICES MANUAL I Figure 1 J 27 Heated Rear Glass Opel 1900 Manta...
Page 122: ...I WIRING DIAGRAMS 1 J 101...
Page 123: ...1 J 102 1973 OPEL 9ER IC MANUAL...
Page 128: ...SPECIAL BODY TOOLS GENERAL INFORMATION 2A 5 W REGULATOR INING INSTALLER J 21828 J 21549 2A 1...
Page 167: ......
Page 231: ......
Page 259: ......
Page 285: ...5C 26 1973 OPEL SERVICE MANUAL...
Page 322: ...ENGINE MECHANICAL AND MOUNTS 6A 31...
Page 350: ...CARBURETOR AND THROTTLE LINKAGE 6E 59 Figure 6E 37 Carburetor Specifications...
Page 361: ......
Page 372: ...Figure 7A 9 Exploded View of Clutch Pedal and Housing...
Page 423: ...Third Clutch Applied Low Band Released...
Page 424: ...AUTOMATIC TRANSMISSION C 63...
Page 425: ...712 64 1973 OPEL SERVICE MANUAL HYDRAULIC OPERATION I r n...
Page 427: ...7C 66 1973 OPEL SERVICE MANUAL...
Page 428: ......
Page 429: ...7C 68 1973 OPEL SERVICE MANUAL II II I...
Page 431: ...7C 70 1973 OPEL SERVICE MANUAL d...
Page 433: ...7C 72 1973 OPEL SERVICE MANUAL...
Page 435: ...7C 74 1973 OPEL SERVICE MANUAL...
Page 437: ...712 76 1973 OPEL SERVICE MANUAL...
Page 439: ...a 1973 OPEL SERVICE MANUAL...
Page 441: ...7C 80 1973 OPEL SERVICE MANUAL...
Page 499: ...7C 138 1973 OPEL SERVICE MANUAL 4 5 I Figure 7C 234 Special Tools Automatic Transmission 7C223...
Page 509: ......
Page 596: ...98 88 1973 OPEL SERVICE MANUAL Figure gB 165 Special Tools...
Page 620: ......