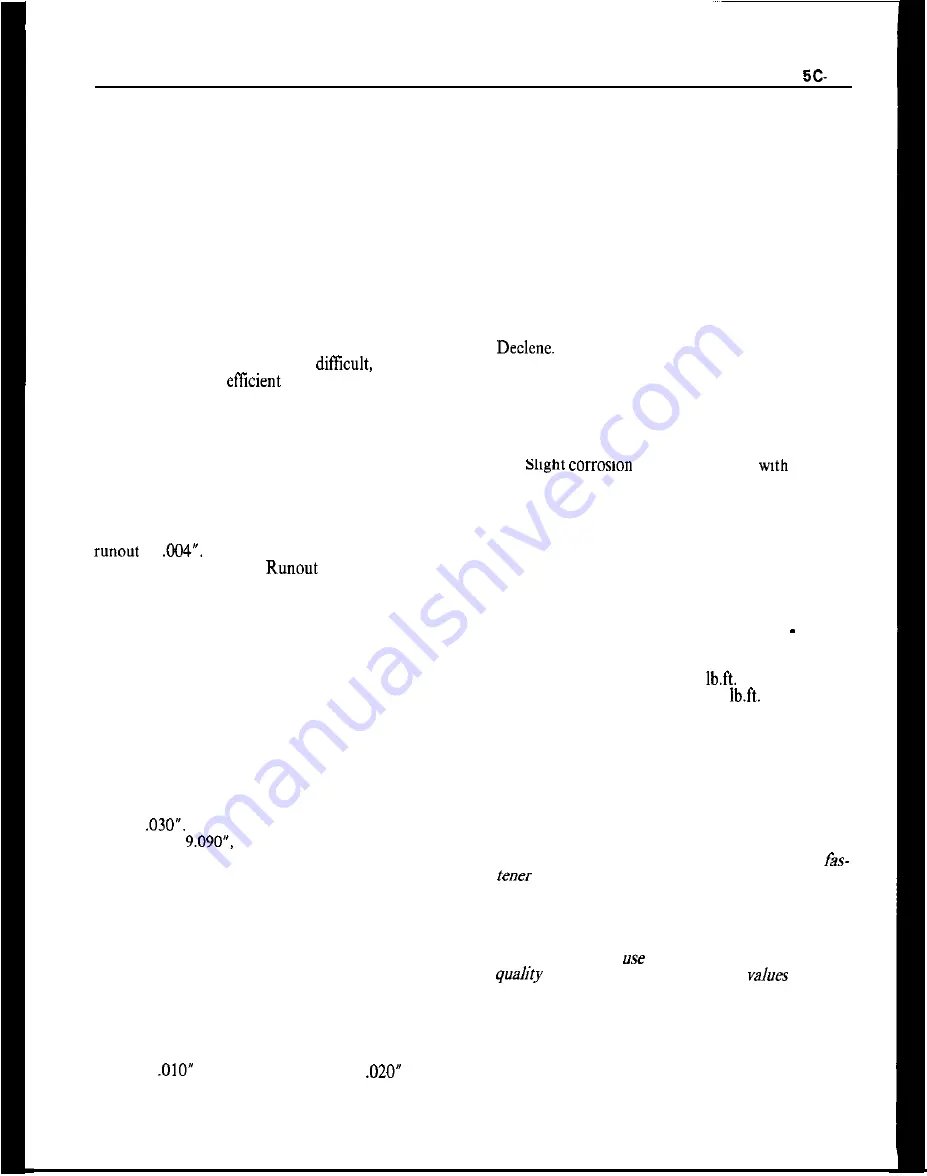
DRUM BRAKES
31
remove grooves, and the ridges in the lining should
be lightly removed with a lining grinder.
If brake linings are more than half worn, but do not
need replacement, the drum should be polished with
fine emery cloth but should not be rebored. At this
stage, eliminating the grooves in drum and smooth-
ing the ridges on lining would necessitate removal of
too much metal and lining, while if left alone, the
grooves and ridges match and satisfactory service
can be obtained.
If brake linings are to be replaced, a grooved drum
should be rebored for use with oversize linings. A
grooved drum, if used with new lining, will not only
wear the lining but will make it
if not im-
possible, to obtain
brake performance.
Out-of-Round Drum
An out-of-round drum makes accurate brake shoe
adjustment impossible and is likely to cause excessive
wear of other parts of brake mechanism due to its
eccentric action. An out-of-round drum can also
cause brake pulsation. Maximum permissible drum
is
A drum that has more run-out than
this
should be rebored.
can be accurately
checked by using an inside micrometer fitted with
proper extension rods.
When measuring a drum for run-out, take measure-
ments at open and closed edges of machined surface
and at right angles to each other.
Turning Brake Drums
If a brake drum is to be turned, enough metal should
be removed to obtain a true, smooth braking surface.
Measure brake drum diameter; standard drum inner
diameter is 9.060”. Drums may be turned to an over-
size of
If maximum inner diameter after turn-
ing exceeds
brake drum will have to be
replaced. Removal of more metal will affect dissipa-
tion of heat and may cause distortion of the drum.
1. Remove rear wheels and drums.
2. Mount brake drum on brake drum lathe and turn
drums as necessary, within limits.
3. After turning, check drum diameter. Inner diame-
ter not to exceed 9.090.
4. A newly-bored drum should always have center
contact with brake shoes. For this reason, arc grind
linings to
under drum radius, or to
under
drum diameter.
5. Clean and install drums and wheels.
BRAKE WHEEL CYLINDER OVERHAUL
1. Remove wheel, drum, and brake shoes. Be careful
not to get grease or dirt on brake lining.
2. Disconnect brake pipe or hose from wheel cylinder
and cover opening with tape to prevent entrance of
dirt. Remove wheel cylinder from backing plate.
3. Remove boots, pistons, cups, and spring from cyl-
inder. Remove bleeder valve.
4. Discard rubber boots and piston cups. Thoroughly
clean all other parts with hydraulic brake fluid or
Do not use anti-freeze, alcohol, gasoline,
kerosene, or any other cleaning fluid that might con-
tain even a trace of mineral oil.
5. Inspect pistons and cylinder bore for scores, scrat-
ches, or corrosion. Light scratches may be polished
with crocus cloth. Do not use emery cloth or sandpa-
per.
may
be cleaned
tine steel
wool. If scratches or corroded spots are too deep to
be polished satisfactorily, the cylinder should be re-
placed since honing is not recommended.
6. Dip internal parts in brake fluid and reassembly
wheel cylinder. When installing piston cups, use care
to avoid damaging the edges.
7. If the rear wheel backing plate is removed: Always
install new paper gaskets one on each side on the
backing plate. Prior to installation, lightly coat paper
gaskets with chassis lubricant. Torque backing plate
to rear axle housing bolts to 43
and wheel brake
cylinder to backing plate bolts to 5
Install wheel
cylinder on brake backing plate and connect brake
pipe or hose.
8. Install brake shoes, drum, and wheel, then flush
and bleed hydraulic system.
9. Adjust brakes, then road test car for brake per-
formance.
C A U T I O N :
This brake backing plate to rear axle
is an important attaching part in that it could
affect the performance of vital components and sys-
tems, and/or could result in major repair expense. It
must be replaced with one of the same part number
or with an equivalent part, if replacement becomes
necessary. Do not
a replacement part of lesser
or substitute design. Torque
must be
used as specified during reassembly to assure proper
retention of this part.
REPLACING BRAKE PIPES
Any brake pipe assembly which is needed must be
made up from service bulk tubing and fittings. All
brake pipes must be made of tin or copper coated
wrapped steel tubing with the ends double lap flared.
Summary of Contents for 1900 1973
Page 1: ......
Page 7: ......
Page 9: ......
Page 48: ...IGNITION SYSTEM lC 27 9 3OlC19 Figure 1 C l 3 Distributor Exploded...
Page 57: ...I I 1 D 36 1973 OPEL SERVICE MANUAL I Figure 1 D 27 Alternator Exploded View 301D27...
Page 95: ...j 1J 74 1973 OPEL SERVICE MANUAL i I m Figure 13 1 Windshield Wiper and Horn Opel 1900 Manta...
Page 96: ...I I WIRING DIAGRAMS lJ 75 Figure lJ 2 Windshield Wiper and Horn Rallye...
Page 97: ...1 J 76 1973 OPEL SERVICE IMANUAL L J Figure lJ 3 Wind hield Wiper and Horn Gl...
Page 98: ...I I I WIRING DIAGRAMS 1J 77 I I Figure 1 J 4 Turn Signal and Hazard Flasher Opel 1900 Manta I...
Page 99: ...I i L I lJ 78 1873 OPEL SERVICE MANUAL Figure lJ 5 Turn Signal and Hazard Flasher GT...
Page 100: ...I WIRING DIAGRAMS 15 79 I I Figure lJ 6 Oil Fuel Temp Tach Stop and Brake Warning Light GT I...
Page 101: ......
Page 102: ...I WIRING DIAGRAMS lJ 81 r Figure 1 J 8 Blower and Lighter GT...
Page 103: ...I I lJ 82 1973 OPEL SERVICE MANUAL Figure lJ 9 indicator Lights and Gauges Opel 1900 Manta...
Page 104: ...I I WIRING DIAGRAMS IJ 83 I Figure 1 J 10 Indicator Lights and Gauges Ratlye...
Page 106: ...EhMB SWITCH R GHiDOOR 301J12...
Page 107: ...1 J 86 1973 OPEL SERVICE MANUAL i Figure 1 J l 3 Headlamps Opel 1900...
Page 108: ...I I I WIRING DIAGRAMS lJ 87 Figure lJ 14 Headlamps Manta...
Page 109: ...1 J 88 1973 OPEL SERVICE MANUAL I 1 Figure lJ 15 Headlamp and Fog Lights Rallye...
Page 110: ...301516...
Page 111: ......
Page 113: ...1 J 92 1973 OPEL SERVICE MANUAL d 5 Figure 1 19 Starting lgniiion and Charging Opel 1900 Manta...
Page 114: ...I I WIRING DIAGRAMS lJ 93 I Figure lJ 20 Starting Ignition and Charging GT...
Page 115: ...1 J 94 1973 OPEL SERVICE MANUAL i I I Figure lJ 21 Instrument Panel GT...
Page 116: ...I I 1 I WIRING DIAGRAMS lJ 95 Figure lJ 22 A C Generator and Regulator All Models...
Page 117: ...301523...
Page 119: ...I I I 10 RED AMP GAGE 301J25...
Page 120: ...WIRING DIAGRAMS lJ 99 Figure lJ 26 Seat Belt Warning System Automatic Transmissionl GT...
Page 121: ...lJ 100 1973 OPEL SERVICES MANUAL I Figure 1 J 27 Heated Rear Glass Opel 1900 Manta...
Page 122: ...I WIRING DIAGRAMS 1 J 101...
Page 123: ...1 J 102 1973 OPEL 9ER IC MANUAL...
Page 128: ...SPECIAL BODY TOOLS GENERAL INFORMATION 2A 5 W REGULATOR INING INSTALLER J 21828 J 21549 2A 1...
Page 167: ......
Page 231: ......
Page 259: ......
Page 285: ...5C 26 1973 OPEL SERVICE MANUAL...
Page 322: ...ENGINE MECHANICAL AND MOUNTS 6A 31...
Page 350: ...CARBURETOR AND THROTTLE LINKAGE 6E 59 Figure 6E 37 Carburetor Specifications...
Page 361: ......
Page 372: ...Figure 7A 9 Exploded View of Clutch Pedal and Housing...
Page 423: ...Third Clutch Applied Low Band Released...
Page 424: ...AUTOMATIC TRANSMISSION C 63...
Page 425: ...712 64 1973 OPEL SERVICE MANUAL HYDRAULIC OPERATION I r n...
Page 427: ...7C 66 1973 OPEL SERVICE MANUAL...
Page 428: ......
Page 429: ...7C 68 1973 OPEL SERVICE MANUAL II II I...
Page 431: ...7C 70 1973 OPEL SERVICE MANUAL d...
Page 433: ...7C 72 1973 OPEL SERVICE MANUAL...
Page 435: ...7C 74 1973 OPEL SERVICE MANUAL...
Page 437: ...712 76 1973 OPEL SERVICE MANUAL...
Page 439: ...a 1973 OPEL SERVICE MANUAL...
Page 441: ...7C 80 1973 OPEL SERVICE MANUAL...
Page 499: ...7C 138 1973 OPEL SERVICE MANUAL 4 5 I Figure 7C 234 Special Tools Automatic Transmission 7C223...
Page 509: ......
Page 596: ...98 88 1973 OPEL SERVICE MANUAL Figure gB 165 Special Tools...
Page 620: ......