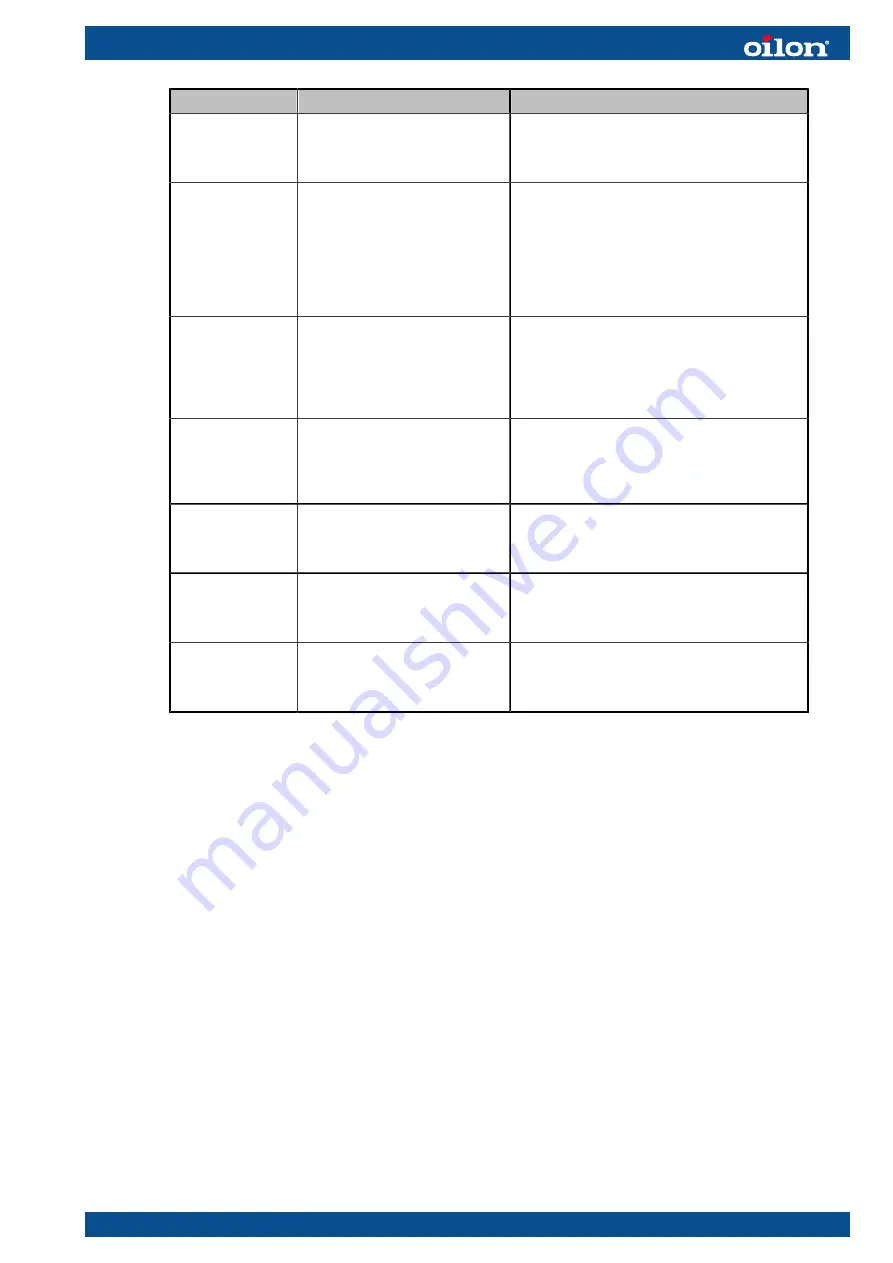
Setting
Description
Example
Inverse control
Changes the control direction of
the control valve
OFF position:
when the voltage is 0 V, the
control valve is all the way in the right position.
ON position:
when the voltage is 0 V, the
control valve is all the way in the left position.
Band
(10–600 °C)
The deviation from target
temperature at which the valve
is adjusted from one extreme
position to another.
● Factory setting for heating
circuits: 300 °C
● Factory setting for DHW
temperature limiter: 30 °C.
If the band is 140 °C and the target temperature
deviates from the current temperature by
14 °C, the valve will be adjusted to 10% of its
maximum.
● If the temperature changes too rapidly,
increase the band.
● If the temperature changes too slowly,
decrease the band.
Integration time
(5–300 s)
Interval for checking and
correcting temperature difference.
● Factory setting for heating
circuits: 50 s.
● Factory setting for DHW
limitation: 40 s.
If the integration time is 10 s, valve position will
be adjusted every 10 s (if necessary).
Derivation time
(0–10 s)
Reaction rate for correcting the
temperature difference.
Factory setting: 0
The greater the derivation time, the more the
control valve’s position will change with each
adjustment.
Note that increasing the derivation time may
increase fluctuation.
Voltage
(0–10 V)
The minimum and maximum
values for the control valve’s
control voltage signal. Factory
settings: 0.0–10.0 V AC
The setting depends on the regulator being
used.
Temperature
differential
(0–10 °C)
The maximum allowed difference
between current temperature and
target temperature.
Factory setting: 0 °C.
If set to 5 °C, the valve’s position will be changed
only when the difference between the measured
temperature and the target temperature is
greater than 5 °C.
Measurement
interval
(0–30 s)
The interval for checking current
temperature.
Factory setting: 0
If set to 15 s, the current temperature will be
checked every 15 s.
● If set to 0, temperature will be monitored
constantly.
5.4.6 Partial / full power: switching between monovalent and bivalent operation
Full power
refers to monovalent operation, which means that only the heat pump’s
compressor will be used for heating. If an external heat source has been connected,
the heat source will be used for backup heating only. This option is enabled by default.
Partial power
refers to bivalent operation, which means that an external heat source
can be used in parallel with the heat pump’s compressor.
If you select the partial power option, you can specify delays for switching on the
external heat source (or sources). Refer to section
Partial power settings
.
5.4.7 Resistor control: control method for external heat source
External heat sources connected to the ground source heating system can be
controlled with either an analog or digital control signal.
Select the signal type in the
Resistor control
view.
M8010 2204EN
53 (75)
Summary of Contents for ESi 6-17
Page 2: ......
Page 62: ...Dimensional drawings ESi 10ESI14_2 ESI 1 ver 1 10ESI14_2 ESI 2 ver 1 60 75 M8010 2204EN...
Page 63: ...Dimensional drawings EMi 10EMI28T_3 EMI ver 1 M8010 2204EN 61 75...
Page 64: ...Dimensional drawings ELi 10ELI60T_2 ELI ver 1 62 75 M8010 2204EN...
Page 78: ...76 75 M8010 2204EN...
Page 79: ......