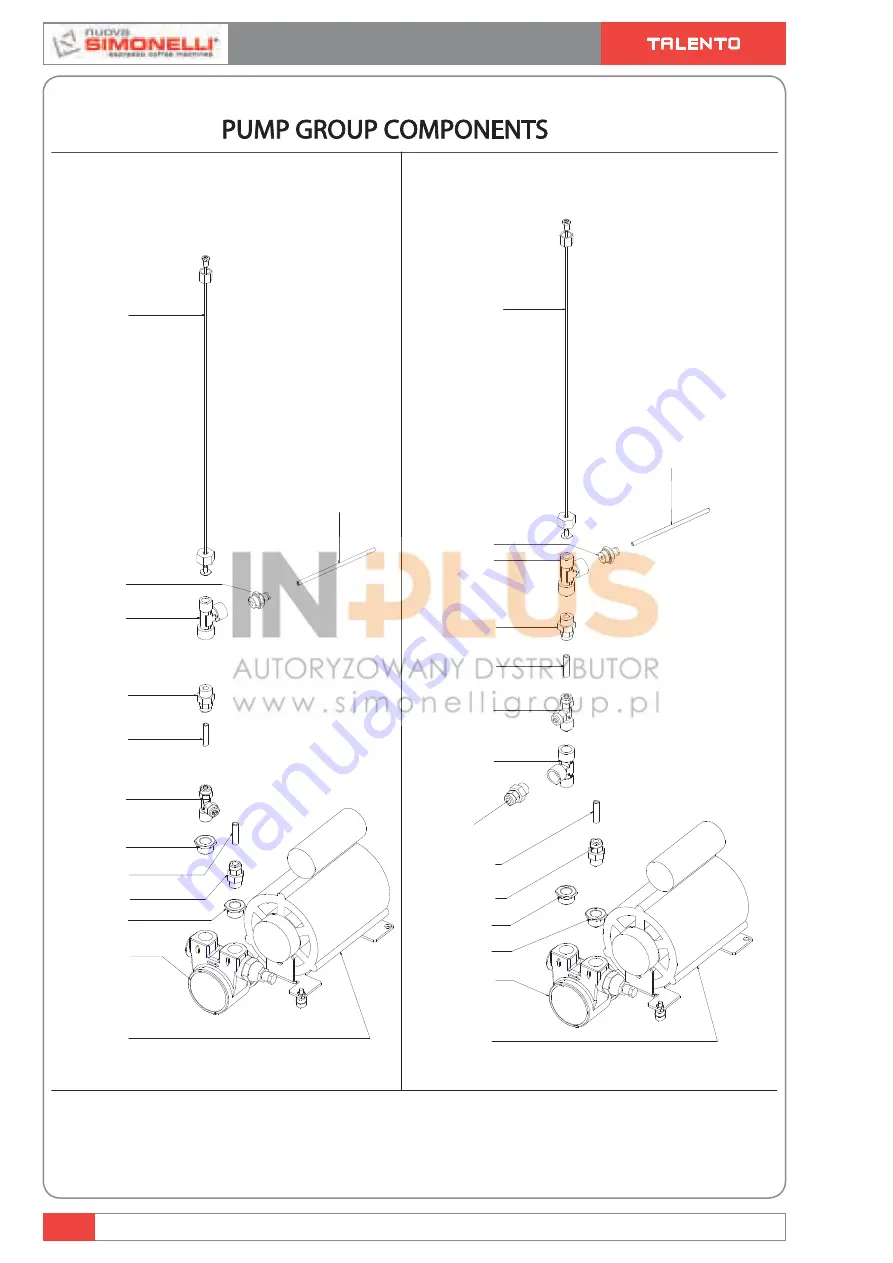
Edition 02 to 12/2013
17.6
SERVICE MANUAL
TAV 04
98030075
07300538
07300365
07300362
11740001
07300716
07300365
07300362
11740001
07300362
07300099
01300004
04500033
11740002
STANDARD VERSION
ECONOMIZER VERSION
98030075
11740002
07300538
07300365
07300362
11740001
07300716
07300099
11740001
07300362
07300099
07300099
01300004
04500033
Summary of Contents for TALENTO
Page 1: ...SERVICE MANUAL ...
Page 2: ...Edition Date Changes on last versions 02 12 2013 Inserimento specifiche Talento Special ...
Page 6: ...Edition 02 to 12 2013 IV SERVICE MANUAL ...
Page 67: ...Edition 02 to 12 2013 6 5 SERVICE MANUAL Fig 10 ...
Page 69: ...Edition 02 to 12 2013 6 7 SERVICE MANUAL Fig 15 ...
Page 108: ...Edition 02 to 12 2013 10 8 SERVICE MANUAL ...
Page 111: ...Edition 02 to 12 2013 11 3 SERVICE MANUAL ...
Page 124: ...Edition 02 to 12 2013 11 16 SERVICE MANUAL ...
Page 135: ...Edition 02 to 12 2013 13 5 SERVICE MANUAL 13 3 FLOWCHART Fig 1 ...
Page 136: ...Edition 02 to 12 2013 13 6 SERVICE MANUAL Fig 2 ...
Page 137: ...Edition 02 to 12 2013 13 7 SERVICE MANUAL Fig 3 ...
Page 138: ...Edition 02 to 12 2013 13 8 SERVICE MANUAL Fig 4 ...
Page 139: ...Edition 02 to 12 2013 13 9 SERVICE MANUAL Fig 5 ...
Page 140: ...Edition 02 to 12 2013 13 10 SERVICE MANUAL Fig 6 ...
Page 141: ...Edition 02 to 12 2013 13 11 SERVICE MANUAL Fig 7 ...
Page 142: ...Edition 02 to 12 2013 13 12 SERVICE MANUAL Fig 8 ...
Page 143: ...Edition 02 to 12 2013 13 13 SERVICE MANUAL Fig 9 ...
Page 144: ...Edition 02 to 12 2013 13 14 SERVICE MANUAL Fig 10 ...
Page 145: ...Edition 02 to 12 2013 13 15 SERVICE MANUAL Fig 11 ...
Page 146: ...Edition 02 to 12 2013 13 16 SERVICE MANUAL Fig 12 ...
Page 156: ...Edition 02 to 12 2013 14 10 SERVICE MANUAL ...
Page 157: ...Edition 02 to 12 2013 15 1 SERVICE MANUAL Fig 1 15 BEVERAGE PREPARATION Fig 2 ...
Page 163: ...Edition 02 to 12 2013 16 3 SERVICE MANUAL Fig 3 16 3 Hydraulic schematic Talento Plus ...
Page 164: ...Edition 02 to 12 2013 16 4 SERVICE MANUAL Fig 4 16 4 Hydraulic schematic Talento special ...
Page 180: ...Edition 02 to 12 2013 17 16 SERVICE MANUAL 17 2 Fridge ...
Page 181: ...Edition 02 to 12 2013 17 17 SERVICE MANUAL ...
Page 182: ...Edition 02 to 12 2013 17 18 SERVICE MANUAL 17 3 CUP WARMER ...
Page 183: ...Edition 02 to 12 2013 17 19 SERVICE MANUAL ...
Page 184: ...Edition 02 to 12 2013 17 20 SERVICE MANUAL ...
Page 196: ...Edition 02 to 12 2013 18 12 SERVICE MANUAL ...
Page 197: ...Edition 02 to 12 2013 19 1 SERVICE MANUAL 19 UPDATES ...
Page 198: ...Edition 02 to 12 2013 19 2 SERVICE MANUAL ...
Page 199: ......