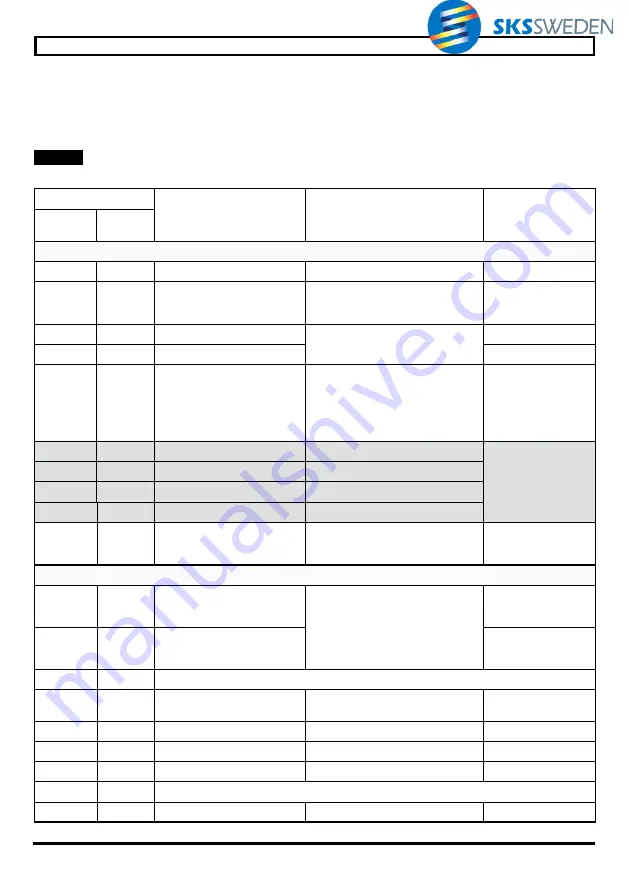
31
Installation and quick start commissioning guide - Commander ID300/302
5511 en - 2017.06 / a
QUICK START COMMISSIONING
4.3 - Basic parameters of STANDARD AV/AI configuration
By default, only Menu 0 is available and used to bring together various commonly used parameters for basic easy
set up of the drive. All the parameters in Menu 0 appear in other menus (advanced menus) which can provide more
precise settings. For more details about Menu 0 parameters or advanced menus, please refer to the user and
technical guide ref.5512 available on www.commanderID300.info.
NOTE
The drive must be disabled during the setting of parameters (terminal 8 or terminals 31 & 34 open).
Parameter
Function
Range
Default value
Menu 0
Adv.
menu
Common parameters
00.001
01.007
Minimum Speed
0.00 to Pr
00.002
10.00 Hz
00.002
01.006
Maximum Speed
0.00 to 150.00 Hz
• 50.00 Hz
• 80.00 Hz for
gear-motor
00.003
02.011
Acceleration Rate
0.0 to 32000.0 s/100 Hz
5.0 s/100 Hz
00.004
02.021
Deceleration Rate
10.0 s/100 Hz
00.005
11.034
Drive Configuration
STANDARD AV/AI, AV with brake,
3PS/1Ana brake,
3PS/1Ana Nobrake, 8 Presets,
Keypad, Keypad Ref,
Electronic Pot, Torque Control,
Pid Control, Local/Remote, Pump
STANDARD AV/AI
00.006
05.007
Motor Rated Current
0.00 to Drive rating (A)
Dependent of the
motor. Factory-set,
do not alter.
00.007
05.008
Motor Rated Speed
0.0 to 9,000.0 rpm
00.008
05.009
Motor Rated Voltage
0 to 240 V or 0 to 480 V
00.009
05.010
Motor Rated Power Factor
0.00 to 1.00
00.010
11.044
User Security Status
Level 1, Level 2, All Menus,
Status Only,
No Access
Level 1
STANDARD AV/AI Preset configuration parameters
00.011
07.007
ADI1 Mode
4-20mA Stop, 20-4mA Stop
4-20mA Low, 20-4mA Low
4-20mA Hold, 20-4mA Hold
0-20mA, 20-0mA
4-20mA Trp, ,20-4mA Trp
4-20mA, 20-4mA, Voltage, Digital
Voltage
00.012
07.011
ADI2 Mode
4-20mA
00.013
-
Not used
00.014
07.045
ADI2 Thermistor Mode
An/Dig Input, Therm Short Cct,
Thermistor, Therm No Trip
An/Dig Input
00.015
07.047
Thermistor Feedback
0 to 4000 Ω
-
00.016
07.008
ADI1 Scaling
0 to 10.000
1.000
00.017
07.012
ADI2 Scaling
0 to 10.000
1.000
00.018
-
Not used
00.019
07.009
ADI1 Invert
0 or 1
0