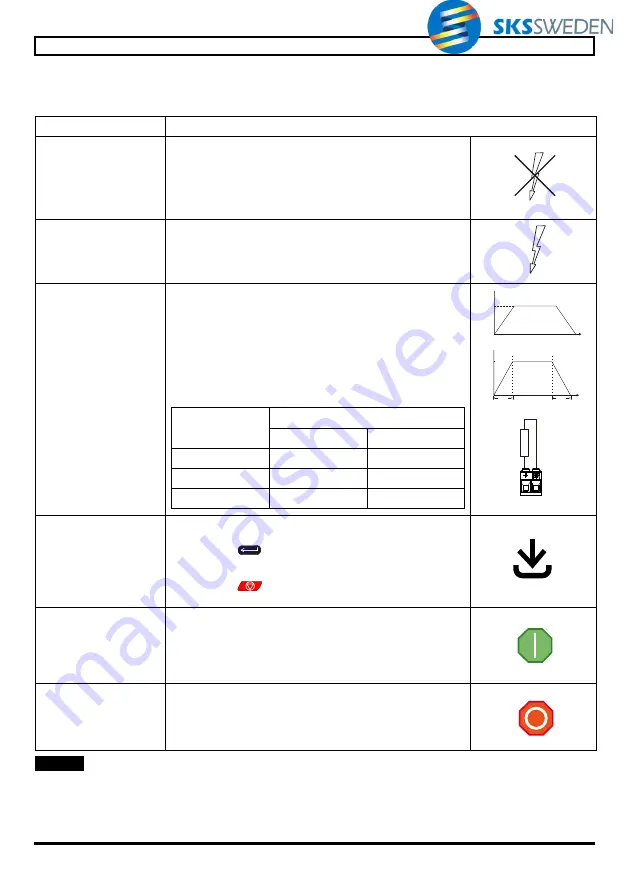
30
Installation and quick start commissioning guide - Commander ID300/302
5511 en - 2017.06 / a
QUICK START COMMISSIONING
4.2.7 - Quick start-up procedure with Field Keypad RTC, ID-SIZEx-Keypad or “Connect” software
Quick start procedure
Action
Details
Before power-up
• Power connections are made (according to section 3.5).
• Control connections (Enable or STO terminals included)
are made (according to section 3.6)
• The Enable signal is not given (terminal 8 for Commander
ID300, and terminals 31 & 34 for Commander ID302)
• Run signal is not given
Power-up the
Commander
ID300/302
• Keep the drive disabled during the setting of parameters
(terminal 8 or terminals 31 & 34 open)
Set Max/Min
frequency and
Acceleration/
Deceleration rates
• Enter the Maximum frequency in Pr
00.002
(Hz). For
gear-motors, keep the value of 80 Hz.
• Enter the Minimum frequency in Pr
00.001
(Hz) if needed
• Enter Acceleration rate in Pr
00.003
(s/100 Hz) and
Deceleration rate in Pr
00.004
(s/100 Hz)
If a braking resistor is installed:
• Set Pr
00.010
= All Menus
• Pr
10.030
, Pr
10.031
and Pr
10.061
should be set
correctly, otherwise premature ‘Brake R Too Hot’ trips may
be seen.
Pr
Braking Resistors
ID-SIZE1-DBR200 ID-SIZE3-DBR400
10.030
0.1
0.2
10.031
600
600
10.061
200
100
100Hz
t
00.003
00.004
t
00.002
Save parameters
If only Menu 0 parameters have been set (Pr
00.xxx
), their
new values are automatically saved when pressing the
Enter button
.
If some advanced parameters have been set, the new
values must be saved. Select 'SAVE' in Pr
00.000
and press
the red reset
button of the keypad.
Start the motor
The drive is now ready to run the motor.
• Close the Enable terminal 8 or the STO terminals 31 & 34.
• Give a Run Forward or Run Reverse command by closing
either terminal 9 or 10.
• Adjust the frequency reference by tuning the potentiome-
ter until the correct speed reference is reached.
Stop the motor
• Remove the Run command by opening terminal 9 or 10 to
stop the motor under ramp control
or
• Remove the Enable signal by opening terminal 8 or 31 &
34 and the motor will coast to a stop.
NOTE
This quick start procedure is dedicated to standard configuration with Pr
00.005
set to ‘STANDARD AV/AI’. Other
preset configurations are available, refer to the user and technical guide ref.5512.