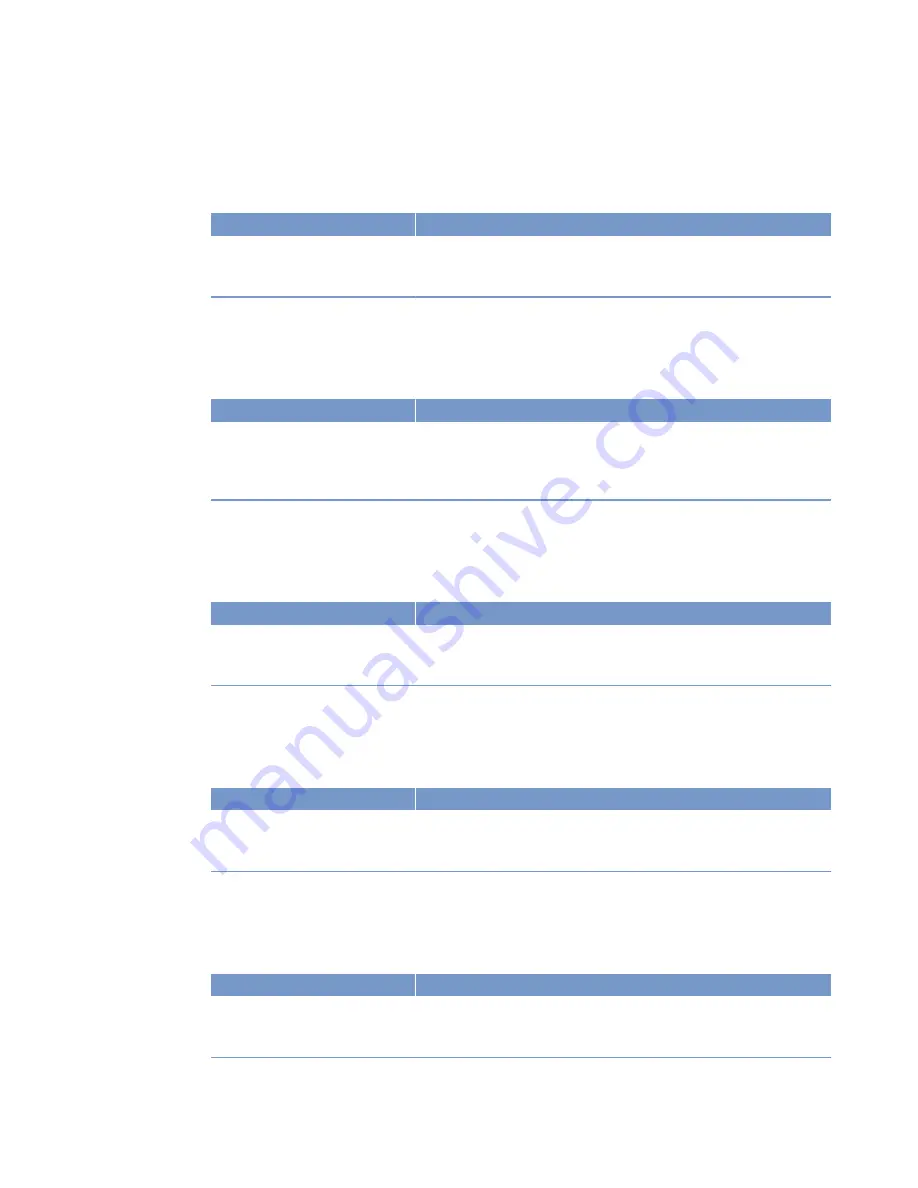
214 – SD P-CrankCase
ZKP-Number: 1.8004.568
Yellow alarm; warning
Cause
Corrective action
Crankcase pressure sensor
faulty; short circuit or wire
break.
u
Check sensor B50 and wiring, replace as necessary
(→ Page 119).
215 – SD P-HD High Pressure Fuel
ZKP-Number: 1.8004.567
Yellow alarm; power limitation < 20%;
Cause
Corrective action
Rail pressure sensor faulty; high-
pressure regulator emergency
mode; short circuit or wire
break.
u
Check sensors B48.1, B48.2, and cabling , replace if necessary
(→ Page 119).
216 – SD T-Lube Oil
ZKP-Number: 1.8004.575
Yellow alarm; warning
Cause
Corrective action
Lube oil temperature sensor
faulty; short circuit or wire
break.
u
Check sensor B7 and wiring, replace as necessary
(→ Page 119).
219 – SD T-Intake Air
ZKP-Number: 1.8004.573
Yellow alarm; warning
Cause
Corrective action
Intake air temperature sensor
faulty; short circuit or wire
break.
u
Check sensor B90 and wiring, replace as necessary
(→ Page 119).
221 – SD Dif Lube Oil
ZKP-Number: 1.8004.585
Yellow alarm; warning
Cause
Corrective action
Lube oil pressure differential
sensor faulty; short circuit or
wire break.
u
Check sensor B93 and wiring, replace as necessary
(→ Page 119).
MS15033/02E 2015-02
| Troubleshooting | 53
TIM-ID: 0000047144 - 003